filmov
tv
How Toyota Changed The Way We Make Things
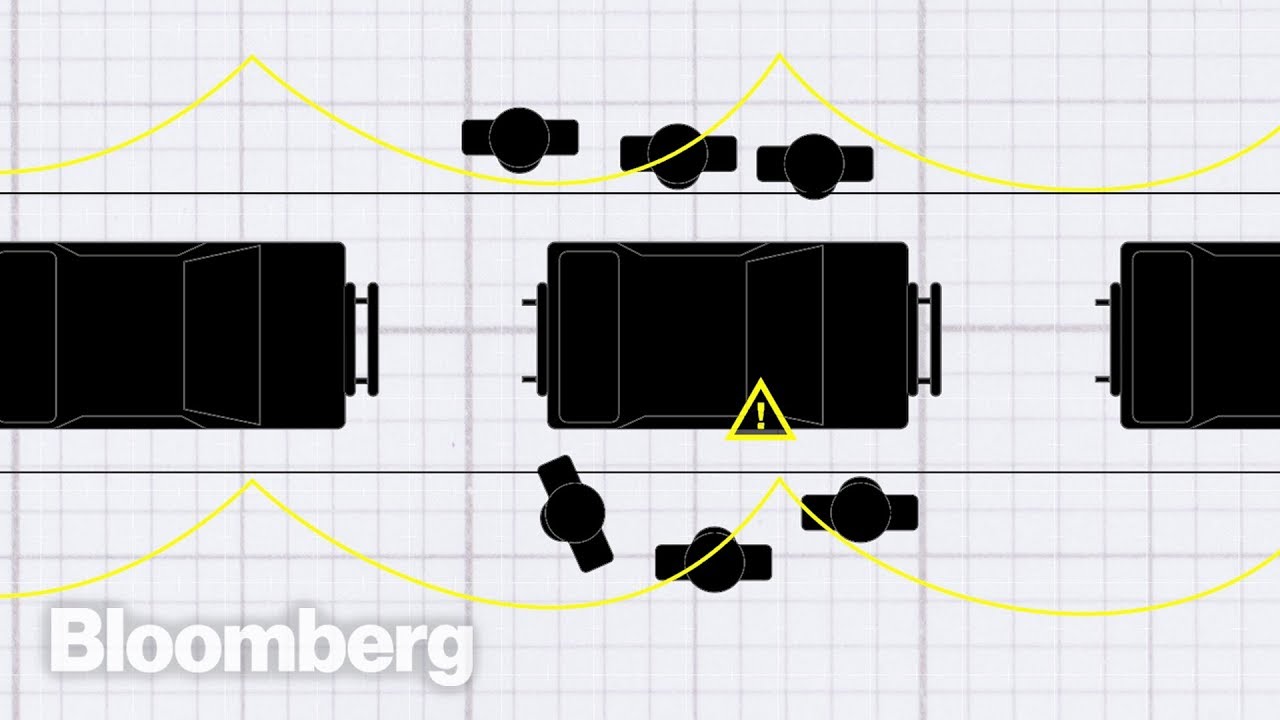
Показать описание
The Japanese Car Company is a corporate behemoth - but it's done much more than just give us Corollas or Land Cruisers. It's changed the way the world makes products. Here's how.
Video by Tom Gibson
Connect with us on...
QuickTake Originals is Bloomberg's official premium video channel. We bring you insights and analysis from business, science, and technology experts who are shaping our future. We’re home to Hello World, Giant Leap, Storylines, and the series powering CityLab, Bloomberg Businessweek, Bloomberg Green, and much more.
Subscribe for business news, but not as you've known it: exclusive interviews, fascinating profiles, data-driven analysis, and the latest in tech innovation from around the world.
Visit our partner channel QuickTake News for breaking global news and insight in an instant.
Video by Tom Gibson
Connect with us on...
QuickTake Originals is Bloomberg's official premium video channel. We bring you insights and analysis from business, science, and technology experts who are shaping our future. We’re home to Hello World, Giant Leap, Storylines, and the series powering CityLab, Bloomberg Businessweek, Bloomberg Green, and much more.
Subscribe for business news, but not as you've known it: exclusive interviews, fascinating profiles, data-driven analysis, and the latest in tech innovation from around the world.
Visit our partner channel QuickTake News for breaking global news and insight in an instant.
How Toyota Changed The Way We Make Things
Toyota Kaizen Clip
Learning from Toyota | Simon Sinek
📖💡Ever wondered why 'The Toyota Way' holds a revered spot in our library, akin to a sacred...
How Does Toyota’s Suspension System Work? Great for Off-Roading and On-Roading | Toyota
Toyota's Reliability Secrets REVEALED
What is Toyota Hybrid System
What Is B Gear On A Toyota Prius?
2024 Toyota Tacoma TRD Off-Road 4x4 in Ice Cap
Toyota Way Principle #14 | Bold Strategy, Large Leaps, and Small Steps
Never do THIS to your Toyota Hybrid New edition!
2021 Toyota Mirai - how it works and what's changed
TOYOTA OWNERS! Please NEVER Do THIS to Your Toyota!
Never do THIS to your New Toyota and Toyota Hybrid
TOYOTA OWNERS! PLEASE Don't Make These Mistakes With Oil Filters!
How to reset the idle on a toyota camry (after battery or terminal change)
How to ● change your 2008 - 2013 Toyota Corolla Engine Air Filter
2014 Corolla How-To: M Gear Shift Position | Toyota
HOW TO RESET OIL LIFE!! - Toyota Camry 2007-2011
Dont do this to your Toyota Hybrid
2014 Tundra How-To: On Demand 4 Wheel Drive | Toyota
How to make your Toyota Last Over 300k Miles without Major Repairs
Toyota How-To: Turn Signal Functions | Toyota
How to ● change your 2008 - 2013 Toyota Corolla Cabin Air Filter. Dust and Pollen.
Комментарии