filmov
tv
Skimming an Engine Block
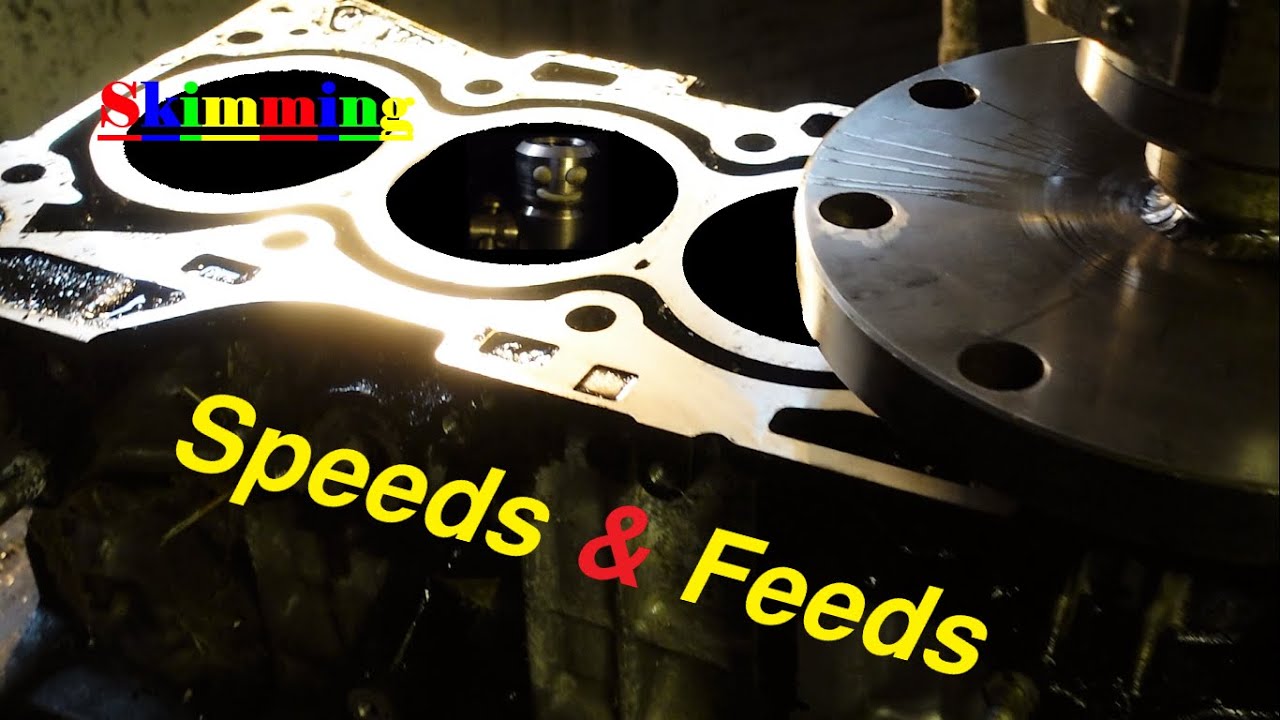
Показать описание
Well i finally had a go at skimming an engine block .....
And i don't think it went to bad at all even managed to learn something in the process witch resulted in a near perfect Finnish.....
First pass:
RPM: 800
Feed: 75 mm/min
DoC: 0.02 (roughly)
Finnishing:
RPM: 1160
Feed: 15 mm/min
DoC: 0.01 (roughly)
OIL:
wd-40
used engine oil
iso 68
Twitter:
Don't like talking in Videos ................. We will see how it goes ?.......
And i don't think it went to bad at all even managed to learn something in the process witch resulted in a near perfect Finnish.....
First pass:
RPM: 800
Feed: 75 mm/min
DoC: 0.02 (roughly)
Finnishing:
RPM: 1160
Feed: 15 mm/min
DoC: 0.01 (roughly)
OIL:
wd-40
used engine oil
iso 68
Twitter:
Don't like talking in Videos ................. We will see how it goes ?.......
Skimming an engine block
Skimming an Engine Block
Head Skimming on a 2016 Ford Transit engine
Skimming engine blocks
Machining On the mill - Resurfacing (skimming) A-series cylinder head
Honda Civic Block Resurfacing Without Removing Engine
Opel Vectra head resurfacing
Cylinder head resurface, best skills!
Reconditioning of Engine Block and Complete Procedure of Boring and Honing Engine Block
engine overhaul|| engine head reface ||head gasket replacement ||engine overheat||#shorts #reels.
Cylinder Heads Resurfacing
How to Resurface Head or Cylinder Block
How do WE clean YOUR engine parts in our machine shop? @JAMSIONLINE
ENGINE BLOCK SKIMMING
Piedmont Trucks Machine Shop- Head Resurfacing
Engine Block Resurfacing
How to Resurface a Cylinder Head at Home
Check an Engine Cylinder Head And Block for Warpage
Engine Block Decking on Bridgeport Milling Machine
Skimming an Engine block
Cylinder head milling at home
Cleaning head gasket surfaces
Cylinder head resurfaced in the Backyard? This guy is a genius!!
Engine block transformation after chemical dipping
Комментарии