filmov
tv
Traditional Stepper vs. StepSERVO motors
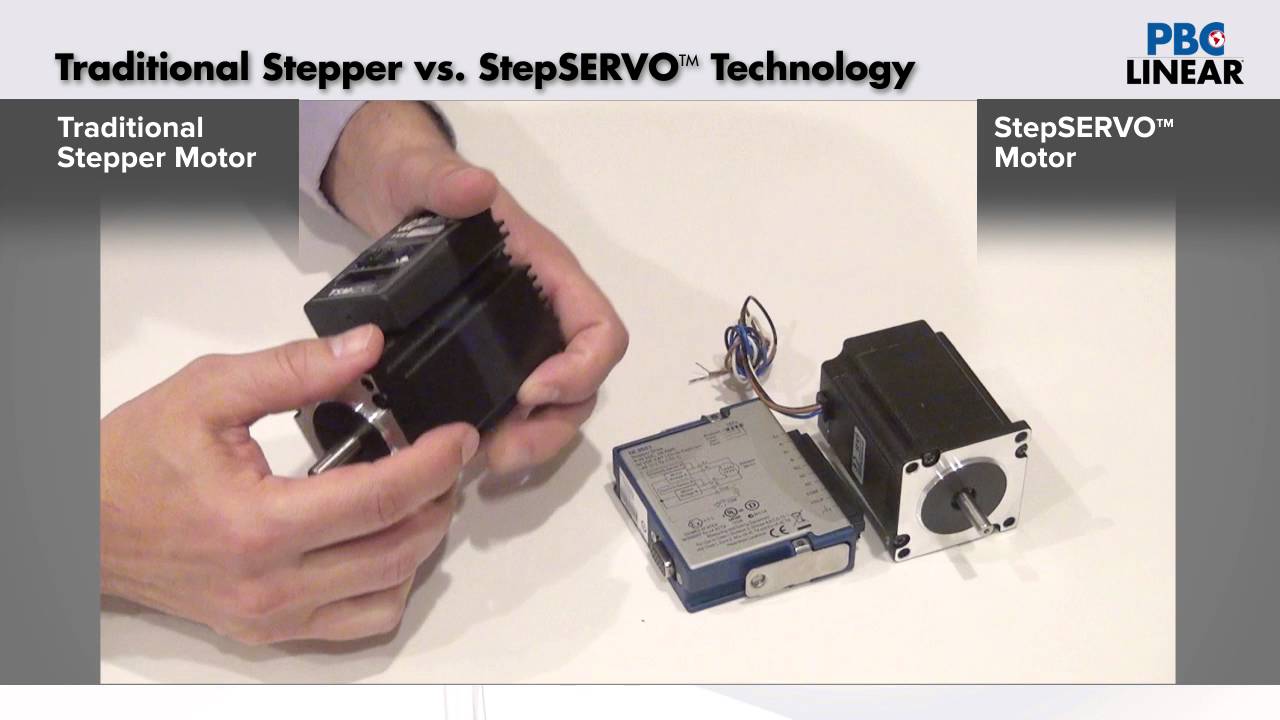
Показать описание
Traditional Stepper vs. StepSERVO motors
Traditional Stepper vs. Step Servo Technology by Eltrex Motion
Stepper Motors vs Servo Motors: A Quick Comparison
What The Differences Between Stepper Motors And Servo Motors
Applied Motion’s StepSERVO Closed Loop Integrated Motors
Servo vs Stepper Motors
Servo vs Stepper Motor
Servo vs Stepper Motors - A Galco TV Tech Tip | Galco
Webinar on StepSERVO™ Integrated Stepper Motors from Applied Motion
Webinar - Under the Hood of Closed-Loop Step Motor Control - 6/4/20
Difference between servo and stepper motors in CNC router
SV200 and StepSERVO 3-Axis Demo
Leadshine hybrid servo vs stepper motor
Stepper Motors vs. Servo Motors - A ClearPath Demonstration
SS-EC Step-Servo & Integrated Motor
Sequre 42 Stepper motor
Closed Loop vs. Open Loop Stepper Motor Driver (HBS860H vs. DM542A)
Inside the Lab: Greater Torque With StepSERVO
Closed loop stepper motor, 8 axis motion, motion control
Introduction to motors. DC, Servo & Stepper.
How to Understand the Difference Between Servo & Stepper Systems
Integrated Drive Step Servo Motor | Digital pulse drive with encoder | 100W | Bholanath | Eng
Servo Motor vs Stepper Motor 2018
MOONS' RS Series Step-Servo System Wiring Introduction
Комментарии