filmov
tv
Best Plastic Welder? Weld Repair Stronger Than New? Let’s find out!
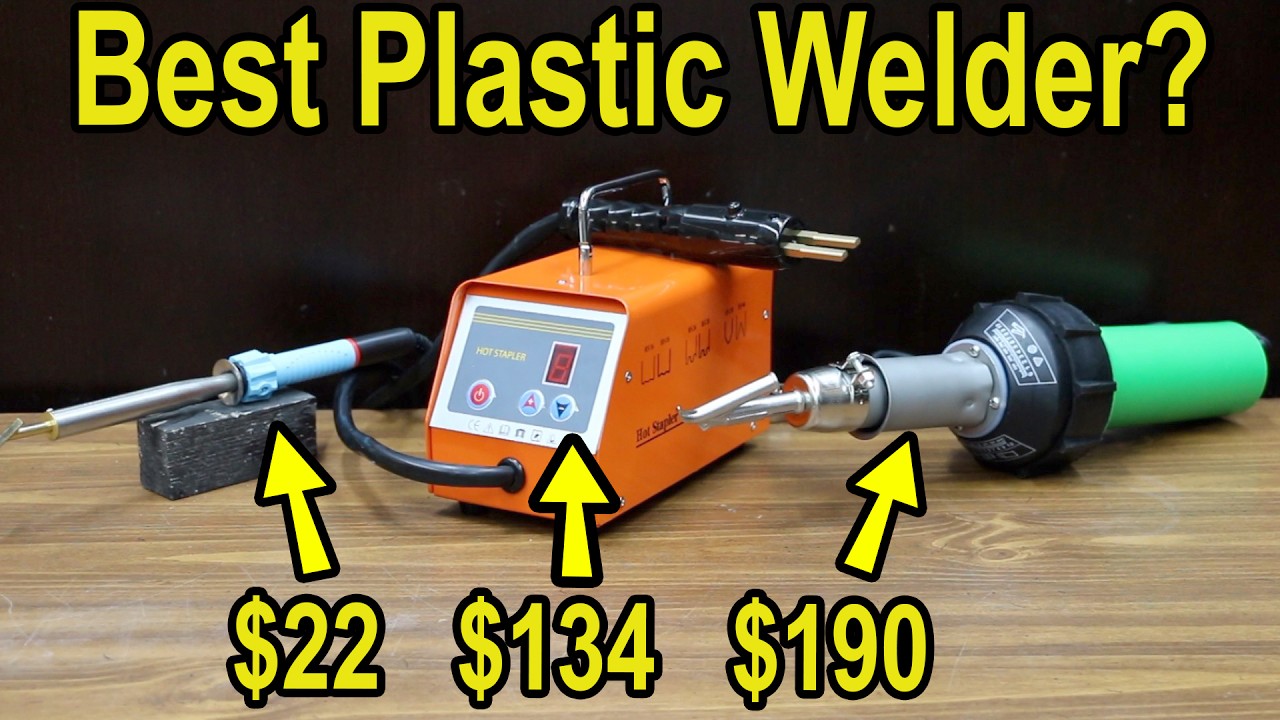
Показать описание
Can the welders restore plastic to it's original strength or even stronger? Let's find out! Let’s compare several plastic repair options using two types of plastic welders. Plastic welders compared for repair strength on HDPE, ABS, and Polycarbonate.
I bought all of the products and supplies used to compare the welders to ensure an unbiased review. So, thank you for supporting the channel!
➡ Thank you for supporting the channel through memberships:
➡ As an Amazon Associate I earn from qualifying purchases.
➡ Products Tested In This Video (in no particular order):
Videography Equipment:
This video is only for entertainment purposes. If you rely on the information portrayed in this video, you assume the responsibility for the results. Project Farm LLC
I bought all of the products and supplies used to compare the welders to ensure an unbiased review. So, thank you for supporting the channel!
➡ Thank you for supporting the channel through memberships:
➡ As an Amazon Associate I earn from qualifying purchases.
➡ Products Tested In This Video (in no particular order):
Videography Equipment:
This video is only for entertainment purposes. If you rely on the information portrayed in this video, you assume the responsibility for the results. Project Farm LLC
Best Plastic Welder? Weld Repair Stronger Than New? Let’s find out!
The best plastic repair? We try out a hot plastic welder - how to / review / tutorial
The STRONGEST Plastic Weld Fix To ANY Broken Or Cracked Plastic Pieces! How To DIY
AMAZONS BEST PLASTIC WELDER
Reviewing the Best Plastic Welders 2024 [ for Easiest Weld Repairs ]
✅ Best Plastic Welders in 2022-2023 | Top 6 Best Handheld Plastic Welder Reviews
Which Is The Best Plastic Welders To Buy
Plastic Welding Repair - one minute tutorial
Smartly save your money & time with just 1 thing🔥|plastic ke bartan jodne ka tarika|life hacks...
Amazon Plastic Welder Review
Top 5 best Plastic Welders 2023 🔥
Achieving Good Plastic Welding. Repost from @AutoPro1112 #yeswelder #shorts #welding #weld #plastic
5 Best Plastic Welders
✅ Top 5: Best Plastic Welders On Amazon 2023
TOP 5 Best Plastic Welders 2023 💥 Best Plastic Welders 💥
Use This Plastic Welding Technique, Become A Master Welder - PVC Welding Tutorial
Polyvance's 5700HT Mini-Weld Model 7 Airless Plastic Welder
Plastic Welding 101 [How to Plastic Weld]
JB Plastic Weld Trying To Mend The Impossible
Bumper Repair with Hot Air Plastic Welder
How to Easily Fix Cracks by Plastic Welding!
5 Best Plastic Welders 2024 Best PVC Welding
DIY Plastic Repair Welder
TOOL test: Plastic Welder - Hot stapel welding - Bumper Repair - Welding Machine Gun - Bildilla Mag
Комментарии