filmov
tv
Simplify 3+2 and 5-Axis Machining with DWO/TCPC – Haas Automation Tip of the Day
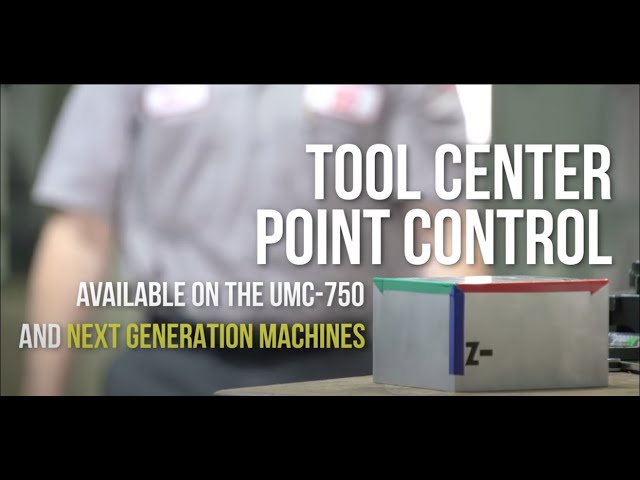
Показать описание
On today’s Tip of the Day, Mark shows how the Haas DWO/TCPC option can greatly simplify 3+2, 4+1, or simultaneous 4- and 5-axis jobs. By using DWO/TCPC (Dynamic Work Offsets / Tool Center Point Control), you can now create your CAM program ahead of time, and then place the workholding and part anywhere on the table, with no need to repost your program! If you’ve ever been frustrated by having to repost your program every time you set up the job, this video is for you.
If you enjoyed this video, please hit the like button and share it with a friend who’ll find it helpful . . . and thanks!
Follow Haas:
If you enjoyed this video, please hit the like button and share it with a friend who’ll find it helpful . . . and thanks!
Follow Haas:
Simplify 3+2 and 5-Axis Machining with DWO/TCPC – Haas Automation Tip of the Day
The Advantages Of 3+2 Machining On 5-Axis Machines
5-Axis Made Easy - Parts 1, 2 and 3
5-Axis 3+2 Machining Conversational Program Demo | Milltronics VM4222IL with Rotary/Tilt Table
3+2 5 AXIS CNC MACHINING CENTER VMC1370
Demonstration of 5-Axis Tool Center Point Control on Haas VF-2
Manufacturing Features: 3+2
3+2 axis machining
Budget CNC Router Build Ep 2 – Free Tools & Fusion 360
3+2 Machining on 5 Axis Haas - Robey Tool & Machine
The Basics of 5-Axis Machining
3+ 2 5 Axis Milling
TCPM | Tool Center Point Mgmt | 5 axis machining concepts | CNC-Learning | Rajeev Sreedharan
3+2 Machining Versus Continuous 5 Axis When to Use Which One and Why
How to realize 5-axis CNC machining with 3+2 axes?. #CNC #cncservice #5axis#5axiscnc
Workholding Techniques: Window Machining & Tabs for 3,4, and 5-Axis Applications!
5 axis positioning on 3 and 4 axis machine tools
3+2 Machining Versus Continuous 5-Axis When to Use Which One and Why?
Simplify 5-Axis Programming with GibbsCAM Webinar
Making the Cut: TITANS of CNC Efficient 3+2 Programming and Multiaxis Roughing
TOP 5 tips to become a Master CNC Machine Programmer | DVF 5000 5 Axis Mill
CNC Machining - 3, 4 & 5th Axis? Explained
3+2 and Simultaneous 5-Axis Machining | AVA Fusion 360
EXTREMELY TIGHT 5-Axis Machining Clearance!!
Комментарии