filmov
tv
DIY CNC Engraving Machine Details & Design
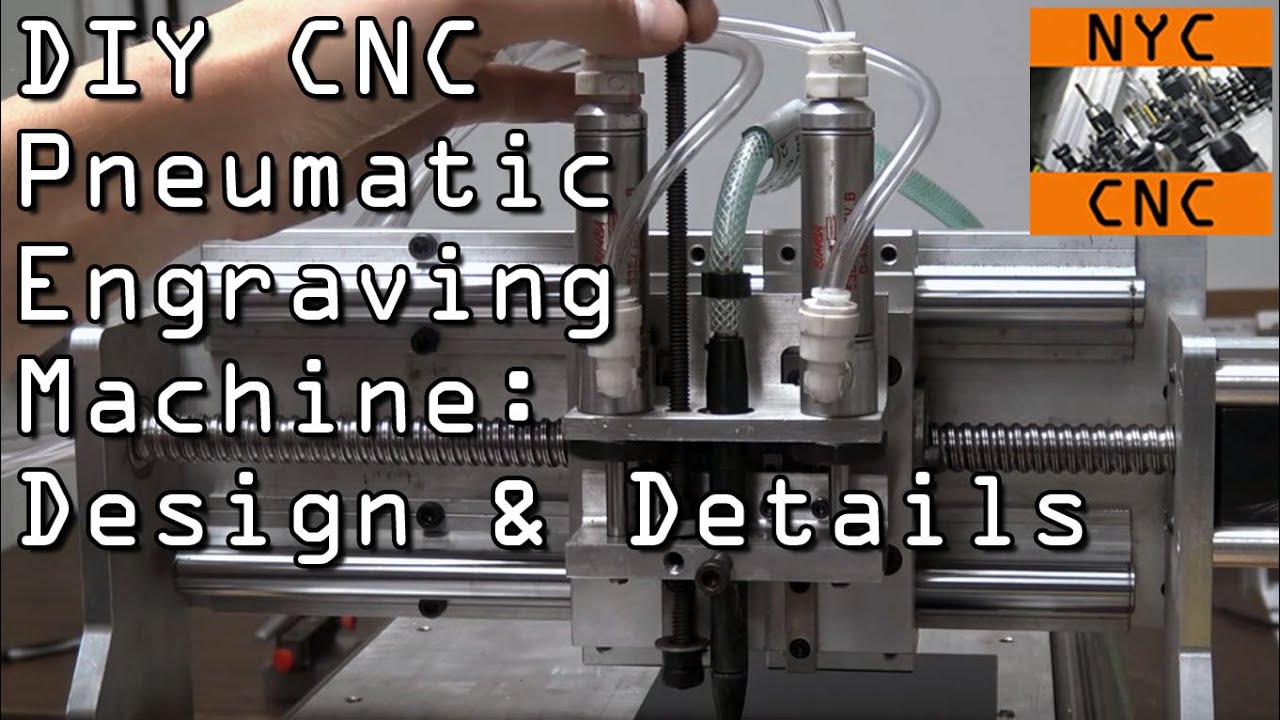
Показать описание
How to build a DIY TinyG & Arduino powered DIY CNC Machine from scratch with linear rails, ball screws and more!
~~~~~~~~~~~~~~~~~~~~~~~~~~~~
Links for this video
~~~~~~~~~~~~~~~~~~~~~~~~~~~~
Reach us / CNC Info:
~~~~~~~~~~~~~~~~~~~~~~~~~~~~
Links for this video
~~~~~~~~~~~~~~~~~~~~~~~~~~~~
Reach us / CNC Info:
DIY CNC Engraving Machine Details & Design
DIY Mini CNC Engraving Machine | Arduino based CNC Router machine
DIY CNC Engraving Machine! Widget69
CNC shield V3 - Shield for Arduino
Mini laser engraving machine #diy
Otomic High Performance 2060 ATC 4 Axis 3D CNC Wood Carving Machine for Sale
CNC Micro Engraving Machine - EleksMaker Pt 1
CNC Router EXTREME DETAIL Engraving w/ V-bit
Foxalien Vasto Cnc with Linear Rails & Ballscrews - Build, Test & Review.
How I built the Simplest CNC Machine with minimum parts possible | DIY Laser Engraver
DIY Mini CNC Engraving Machine,PCB Milling Machine
My DIY CNC Router build with ATC and Vacuum Table
Making CNC Machine || 3 Axis Milling Machine || CNC Engraving Machine
Woodworking cnc router machine
Small desktop CO2 laser engraving machine
multi_functions all-in-one cnc wood lathe composition machine for irregular shaped furniture legs
DIY CNC 002 - Specification & Hardware
3D Door Design is Made on CNC machine
leaves #production process #laser engraving #leaf engraving machine #entrepreneurship
2022 New Update CNC 3018Pro Max Engraving Machine diy CNC Router Grbl Assembly Video Tutorial
DIY Mini CNC Milling / Laser Engraving Machine Assembly
Wooden 3d Cnc work high-speed work #cnc
CNC Basics - What You Need To Get Started
DIY CNC Router Build and Testing (With Limited Tools!)
Комментарии