filmov
tv
What is a CNC Router Vacuum System Table and How Does It Work
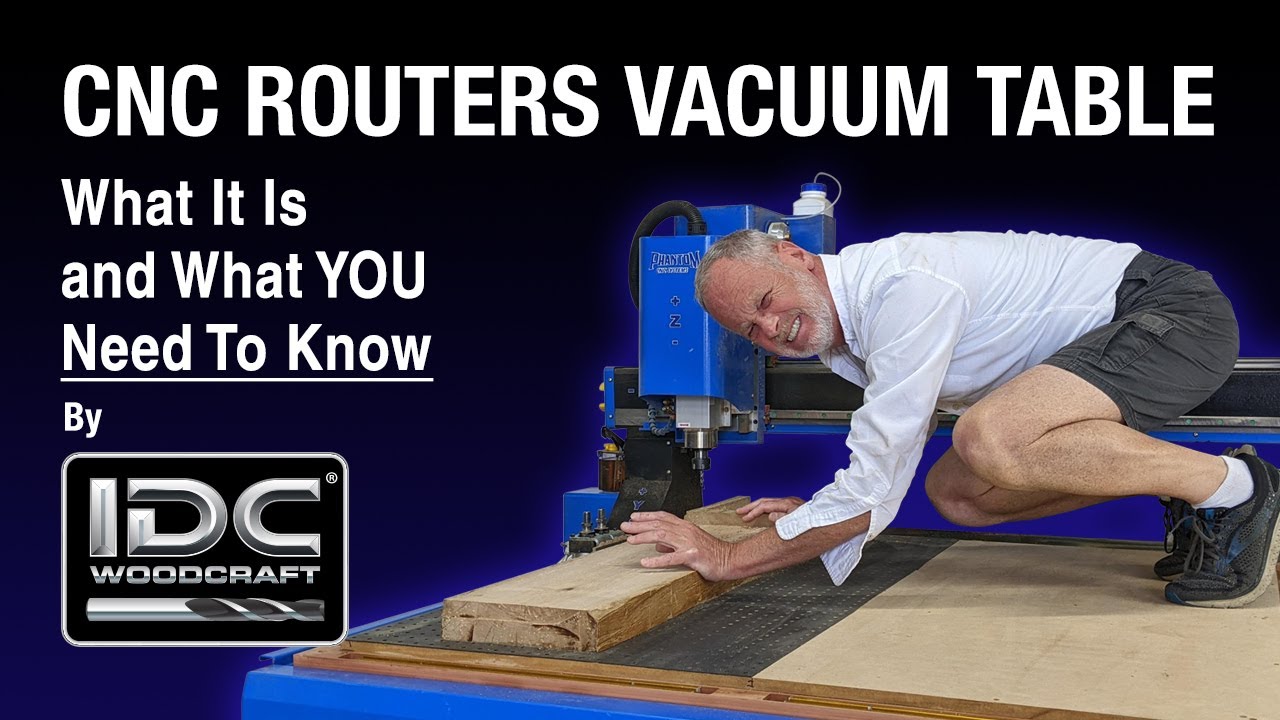
Показать описание
Welcome to this CNC router video tutorial about vacuum tables, and about how does a vacuum table work, or even what is a vacuum table for and how to enhance their hold-down power!
In this episode, you may find that your CNC router vacuum pump is just fine, that it may be your setup. We dive into vacuum mats that revolutionize the effectiveness of your vacuum table. Our focus will be on the exceptional vacuum mat from All Star CNC. To put it to the test, we'll be using the Phantom CNC router by Phantom CNC Systems, along with two router bits from IDC Woodcraft: "The BEAST," a groundbreaking roughing CNC router bit, and the 1.5-inch ultra-smooth surfacing bit. Prepare for the phenomenal results achieved in this comprehensive experiment.
Throughout our testing, the vacuum mat proved to be a game-changer, significantly boosting the suction capability of vacuum tables, such as on the Phantom CNC router. Even when subjected to aggressive cutting on a hardwood like Maple, the vacuum mat held its ground admirably. We were thrilled to witness the vacuum mat withstand the forces exerted upon it, providing an unrivaled level of stability and hold-down power.
One common question regarding MDF on vacuum tables is, can you pull a vacuum through MDF.. MDF is porous and a vacuum can be pulled through it. In this video, we will discuss how to ensure the most effective way to utilize MDF for a CNC router vacuum table.
All-Star CNC Products page w/ vacuum mat ↓
Or call 253-320-1211 for more information regarding Phantom CNC routers. Tell then Garrett says hello!
ROUTER BITS DISCUSSED
------------------------------------------------------
ROUTER BITS FOR CNC ROUTERS
***Use this discount code (SURFACING BIT)
Recommended Design Software
_____________________________
CNC FREE STUFF AND MORE
_____________________________
------------------------------------------------------
------------------------------------------------------
Please support IDC Woodcraft Youtube channel:
------------------------------------------------------
------------------------------------------------------
Garrett Fromme
In this episode, you may find that your CNC router vacuum pump is just fine, that it may be your setup. We dive into vacuum mats that revolutionize the effectiveness of your vacuum table. Our focus will be on the exceptional vacuum mat from All Star CNC. To put it to the test, we'll be using the Phantom CNC router by Phantom CNC Systems, along with two router bits from IDC Woodcraft: "The BEAST," a groundbreaking roughing CNC router bit, and the 1.5-inch ultra-smooth surfacing bit. Prepare for the phenomenal results achieved in this comprehensive experiment.
Throughout our testing, the vacuum mat proved to be a game-changer, significantly boosting the suction capability of vacuum tables, such as on the Phantom CNC router. Even when subjected to aggressive cutting on a hardwood like Maple, the vacuum mat held its ground admirably. We were thrilled to witness the vacuum mat withstand the forces exerted upon it, providing an unrivaled level of stability and hold-down power.
One common question regarding MDF on vacuum tables is, can you pull a vacuum through MDF.. MDF is porous and a vacuum can be pulled through it. In this video, we will discuss how to ensure the most effective way to utilize MDF for a CNC router vacuum table.
All-Star CNC Products page w/ vacuum mat ↓
Or call 253-320-1211 for more information regarding Phantom CNC routers. Tell then Garrett says hello!
ROUTER BITS DISCUSSED
------------------------------------------------------
ROUTER BITS FOR CNC ROUTERS
***Use this discount code (SURFACING BIT)
Recommended Design Software
_____________________________
CNC FREE STUFF AND MORE
_____________________________
------------------------------------------------------
------------------------------------------------------
Please support IDC Woodcraft Youtube channel:
------------------------------------------------------
------------------------------------------------------
Garrett Fromme
Комментарии