filmov
tv
Using Stealth Propulsion for Ocean Travel (MHD Thruster Build)
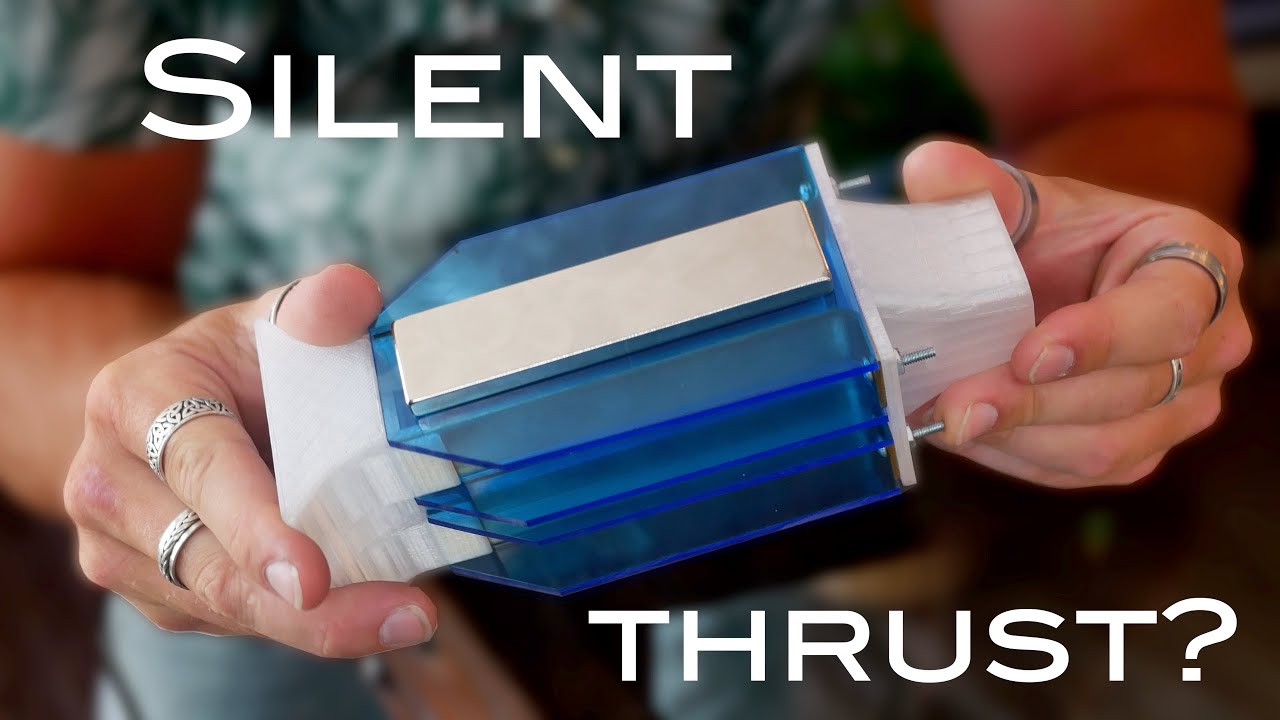
Показать описание
Magnetohydrodynamic thrust uses no moving parts in order to accelerate water. It has been known for half a century, but it may be possible that we're only now beginning to explore it for use in Marine travel. I built a modular MHD drive with great results, and documented the journey. The greatest strength of MHD thrust, may be its silence.
Support / Follow Plasma Channel on:
Instagram: Plasma_Channel_Official
=======================
***Music credits***
======================
Title screen music:
Song: Sappheiros - Awake
Music provided by Vlog No Copyright Music.
Creative Commons - Attribution 3.0 Unported
ALL other music provided by Epidemic Sounds
#future #innovation
Using Stealth Propulsion for Ocean Travel (MHD Thruster Build)
Using Stealth Propulsion for Ocean Travel (MHD Thruster Build)
Pumping Water Without Blades - Magnetic Pumps - Future of Propulsion?
The Power of a Nuclear Submarine
Why Nuclear Submarines Cannot Touch the Bottom
This Dad Built A Home-Made Jet Pack 😱
How does a Submarine work? / Typhoon-class submarine // The worlds largest submarine ever built.
Nuclear Explosion seen from New Zealand!
New marine propulsion technology Heptere Marine (How it works)
US Navy Nuclear Submarine Bursts Through Polar Ice
The Submarine with a Laser
The Manta Ray: How America's Futuristic Underwater Drone will Change Warfare.
Ion Propulsion - The Plane With No Moving Parts
Life Inside US $4 Billion Nuclear Submarine. Inside Kitchen and Sleeping Rooms
Genius Idea China Uses Laser propulsion for the Fastest Submarines in the world's
This is what 10,000 hours of practice looks like
The Insane Engineering of the F-35B
DARINS stealth boat with reactionless propulsion drive
Naval Group's Propulsion Systems: 3D printing
Removing Snow off a Tesla #shorts
Do the US Navy SEALs have FLYING SUBMARINES?
The Lamborghini 63 docking at the F1 track
Nuclear submarine propulsion systems unclassified part 1
Unveiling the INS Aragat's Revolutionary Nuclear Propulsion #insarighat
Комментарии