filmov
tv
EEVblog #1267 - How To Control a 747 Flight Simulator
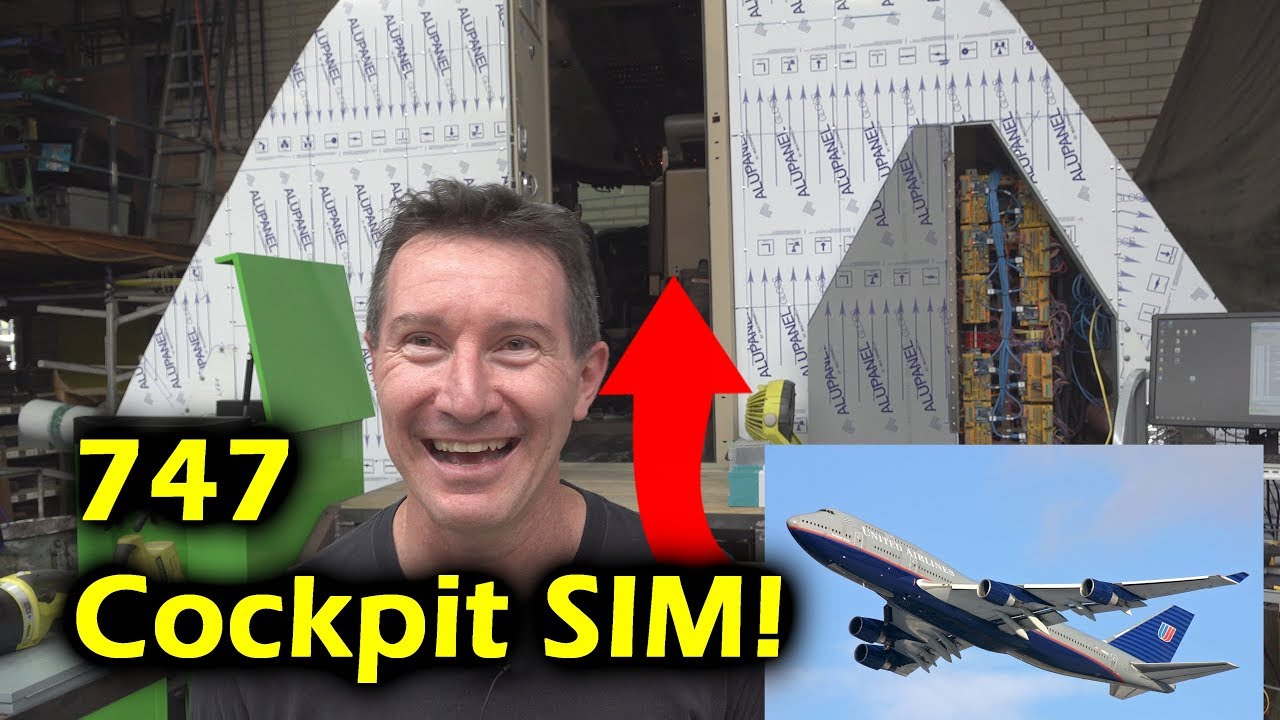
Показать описание
How do you control the thousands of switches, sensors, actuators, bulbs and ARINC 429 bus devices in the world's most expensive 747 flight simulator?
Rod Redwin from Simulator Solutions explains the design on the I/O solution for such a mammoth task.
Support the EEVblog through Patreon!
Buy anything through that link and Dave gets a commission at no cost to you.
Donate With Bitcoin & Other Crypto Currencies!
Rod Redwin from Simulator Solutions explains the design on the I/O solution for such a mammoth task.
Support the EEVblog through Patreon!
Buy anything through that link and Dave gets a commission at no cost to you.
Donate With Bitcoin & Other Crypto Currencies!
EEVblog #1267 - How To Control a 747 Flight Simulator
EEVblog #1271 - 100kW WindWall Generator BUSTED!
EEVblog #1268 - DIY Boeing 747 Cockpit Simulator Full Tour
EEVblog #1269 - Solar Roadways SR4 DATA Hilarity!
EEVblog #1265 - $53 360W Lab Bench PSU!
EEVblog #1230 - How The Apollo 11 Moon Walk Video Happened
EEVblog #1274 - Long Term Alkaline Battery Leakage Testing
#1266 Philips PM 5712 Pulse Generator (part 1 of 3)
Philips PM5712 pulse generator 1980 test repair teardown
TRRS #1267 - Old Electronic Books/Magazines on CDs
#1267 Philips PM 5712 Pulse Generator (part 2 of 3)
Merry Solar Roadways Christmas!
🔴 Fixing A Classic PowerMac G4 Power Supply - Vintage PowerMac G4 Repair - No.1267
Test Equipment Drone Hp pulse generator 8011a/8015a + Wavetek Model 30 + Sanyo Mc-1 + Mod Duo
Installing a 6 kW 48 V rectifier rack in the basement
Home cockpit cessna 172 - x plane 11
EEVblog #1282 - Design Your Own Membrane Keypad! (µSupply Part 20)
#1268 Philips PM 5712 Pulse Generator (part 3 of 3)
World's Most Expensive DIY Flight Simulator!
1265 Energy As A Strategy
Karl Koscher - An Introduction to the ARINC standards - DEF CON 27 Aviation Village
#1319 HP 8601A Sweep Generator (part 1 of 2)
Power Tips: Managing your DC/DC converter's switch node sensitivity
Laser Printer Teardown - Samsung ML3312ND
Комментарии