filmov
tv
18 (ish) Mechanical Design Tips and Tricks for Engineers Inventors and Serious Makers: # 093
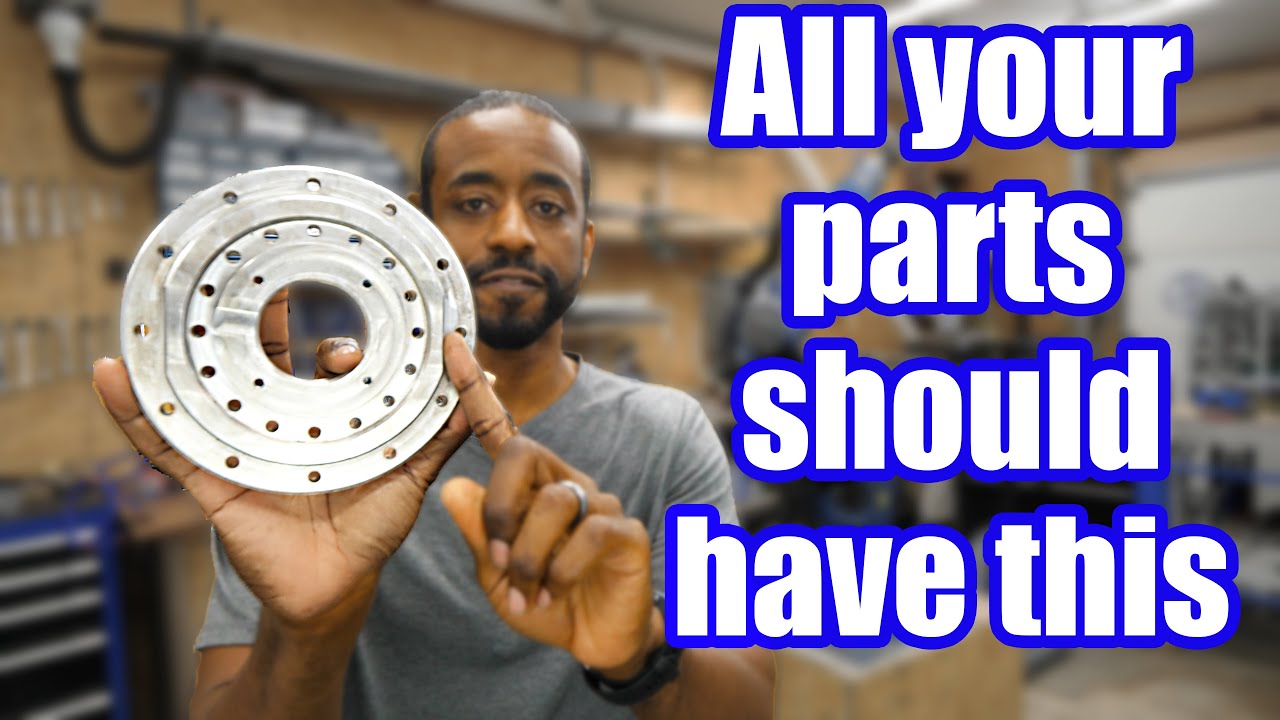
Показать описание
How to quickly change your idea into a real manufacturable product.
Thank you LOCTITE® for Sponsoring this video!
If you want to chip in a few bucks to support these projects and teaching videos, please visit my Patreon page or Buy Me a Coffee.
Social media
My other channel - Fatherhood engineered
Link to LOCTITE® plastics guide
Link to LOCTITE® 8000 series adhesive details
Link to LOCTITE® Xplore
Gears of Fire 516 YouTube channel
Gears of Fire website
************************************
Notes:
Technical corrections
Nothing yet
Thank you LOCTITE® for Sponsoring this video!
If you want to chip in a few bucks to support these projects and teaching videos, please visit my Patreon page or Buy Me a Coffee.
Social media
My other channel - Fatherhood engineered
Link to LOCTITE® plastics guide
Link to LOCTITE® 8000 series adhesive details
Link to LOCTITE® Xplore
Gears of Fire 516 YouTube channel
Gears of Fire website
************************************
Notes:
Technical corrections
Nothing yet
18 (ish) Mechanical Design Tips and Tricks for Engineers Inventors and Serious Makers: # 093
50 3D Modeling Tips and Best Practices for Mechanical Designs. - Jeremy Fielding 099
What do I do as a Mechanical Design Engineer?
Mechanical mechanism & applications, #mechanism, #design, #solidworks, #diy ,#technology , #fyp
Creative Mechanical Design in Old Fashioned Mechanisms - The Pick and Place Machine pt. 1 #shorts
Cool Mechanical Design on Everyday Part
How Engineers Build Products from Scratch
10 Tips to Improve Your CAD Designs for CNC Machining
How ChatGPT Simplifies Mechanical Engineering? From Design to Production
Meet Daria Junttanen, Photomask and Mechanical Designer
Day in the Life of a Mechanical Design Engineer
1200 mechanical Principles Basic
Design Engineering Career Growth: Tips and Strategies | How to grow as a design engineer
Top skills for Mechanical Design Engineers to get a Job with MNC | Top Design skills for Freshers
Milling Curves With a Rotary Table - Hemingway Sensitive Knurling Tool Build - Part 3
19 Mechanical Properties Every Mechanical Engineer Should Know.
Mechanical Engineering 101: Engineering Drawings
Top 3 Considerations When Designing a Machine
50-mechanical mechanisms commonly used in machinery and in life
Most Important Mechanical Engineering Skills To Learn
Top 6 Super Useful Websites For Mechanical Engineers 🛠
Mechanical design
Tips for Design Engineers
The Day you become a Mechanical Design Engineer - Ryan Fix
Комментарии