filmov
tv
Weldable Strain Gauge Sensor Installations (Winter 2018)
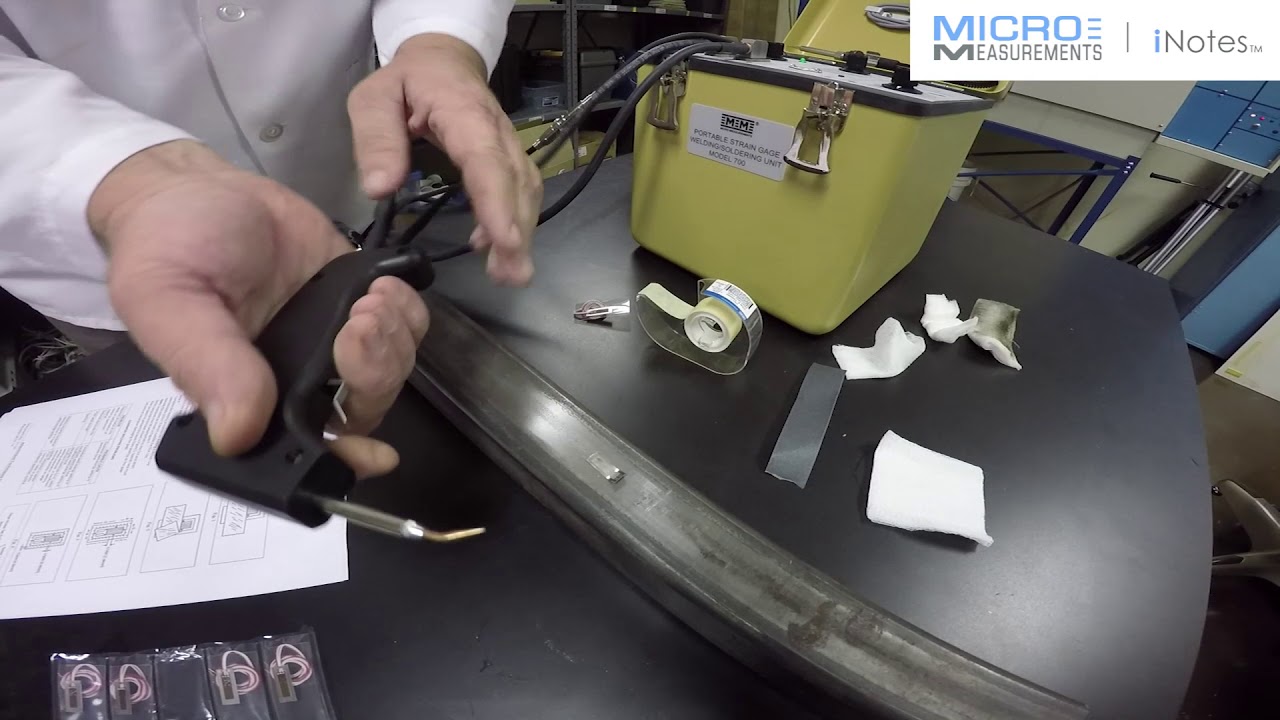
Показать описание
You have been tasked with making strain measurements on a railroad bridge during the middle of a Minnesota winter. Obviously, you can’t warm the bridge sufficiently to cure adhesives for a standard bonded foil sensor installation.
There is a solution: weldable strain sensors.
The vast majority of installations employ adhesive bonding, a tried and true method used since the invention of the bonded resistance strain gage in 1936. Micro-Measurements offers an extensive line of adhesives that perform well in a myriad of applications, including those exposed to extreme operating temperatures—from deep cryogenic up to 800 °F.
In some test applications, weldable sensors can offer very significant advantages over bondable sensors. For example, they are ideal for use on large test structures when it is not practicable to apply clamping pressure to the gage installation during the adhesive cure process. Weldable sensors can also be an excellent substitute for bondable sensors when the temperature of the test surface is below the minimum required for proper cure of the boding adhesive, and cannot be easily raise
There are instances, however, where adhesive bonding is just not an option. For example:
•Steel bridge sections in cold environments or difficult-to-access locations
•Ship hulls in very humid or wet environments
•High-temperature applications above 700 °F
•Test specimens that can’t be taken offline for gage installation
In such cases, welding a gage in place is often the best solution. Micro-Measurements offers a range of weldable devices, including sealed versions with pre-attached cables for wet environments; open-tab versions to accommodate installation of lead wires; and high-temperature versions free of organic materials for operation up to 1800 °C. So, is this installation technique difficult to learn? Not at all. In fact, surface preparation is nearly identical to bonded gages. Typically, a technician experienced in strain gage bonding can perfect the welding technique in less than an hour. Our weldable gages are provided on an Inconel or stainless steel shim to allow for spot welding. To facilitate installation, the Model 700 Portable Strain Gage Welding/Soldering unit enables capacitive discharge welding and features an onboard soldering pencil for lead wire attachment. The Model 700 includes a charging unit and can be placed in a backpack to free up technicians' hands.
There are a number of other advantages in using weldable gages:
•Bonding to the shim is performed under ideal conditions to ensure proper adhesion
•Fast installation with no adhesive cure time required
•Installations are compatible with most conventional protective coatings
•Testing can often begin immediately
Micro-Measurements standard weldable strain gages are available as single-element strain gages, and as two-element “T-rosettes”. The two CEA-Series patterns are available with a choice of either 120- or 350-ohm grids. Those in the LWK Series are available only with 350-ohm grids and preattached leadwires. LEA-Series weldable strain gages are both precabled and polymer-coated for water immersion and protection from weather. Micro-Measurements also offers a weldable temperature sensor to complement the gages.
For weldable strain gages, following is a list of materials needed and links to products:
Weldable Strain Gages:
Model 700 Portable Strain Gage Welder
There is a solution: weldable strain sensors.
The vast majority of installations employ adhesive bonding, a tried and true method used since the invention of the bonded resistance strain gage in 1936. Micro-Measurements offers an extensive line of adhesives that perform well in a myriad of applications, including those exposed to extreme operating temperatures—from deep cryogenic up to 800 °F.
In some test applications, weldable sensors can offer very significant advantages over bondable sensors. For example, they are ideal for use on large test structures when it is not practicable to apply clamping pressure to the gage installation during the adhesive cure process. Weldable sensors can also be an excellent substitute for bondable sensors when the temperature of the test surface is below the minimum required for proper cure of the boding adhesive, and cannot be easily raise
There are instances, however, where adhesive bonding is just not an option. For example:
•Steel bridge sections in cold environments or difficult-to-access locations
•Ship hulls in very humid or wet environments
•High-temperature applications above 700 °F
•Test specimens that can’t be taken offline for gage installation
In such cases, welding a gage in place is often the best solution. Micro-Measurements offers a range of weldable devices, including sealed versions with pre-attached cables for wet environments; open-tab versions to accommodate installation of lead wires; and high-temperature versions free of organic materials for operation up to 1800 °C. So, is this installation technique difficult to learn? Not at all. In fact, surface preparation is nearly identical to bonded gages. Typically, a technician experienced in strain gage bonding can perfect the welding technique in less than an hour. Our weldable gages are provided on an Inconel or stainless steel shim to allow for spot welding. To facilitate installation, the Model 700 Portable Strain Gage Welding/Soldering unit enables capacitive discharge welding and features an onboard soldering pencil for lead wire attachment. The Model 700 includes a charging unit and can be placed in a backpack to free up technicians' hands.
There are a number of other advantages in using weldable gages:
•Bonding to the shim is performed under ideal conditions to ensure proper adhesion
•Fast installation with no adhesive cure time required
•Installations are compatible with most conventional protective coatings
•Testing can often begin immediately
Micro-Measurements standard weldable strain gages are available as single-element strain gages, and as two-element “T-rosettes”. The two CEA-Series patterns are available with a choice of either 120- or 350-ohm grids. Those in the LWK Series are available only with 350-ohm grids and preattached leadwires. LEA-Series weldable strain gages are both precabled and polymer-coated for water immersion and protection from weather. Micro-Measurements also offers a weldable temperature sensor to complement the gages.
For weldable strain gages, following is a list of materials needed and links to products:
Weldable Strain Gages:
Model 700 Portable Strain Gage Welder
Комментарии