filmov
tv
Extrusion Width - The magic parameter for strong 3D prints?
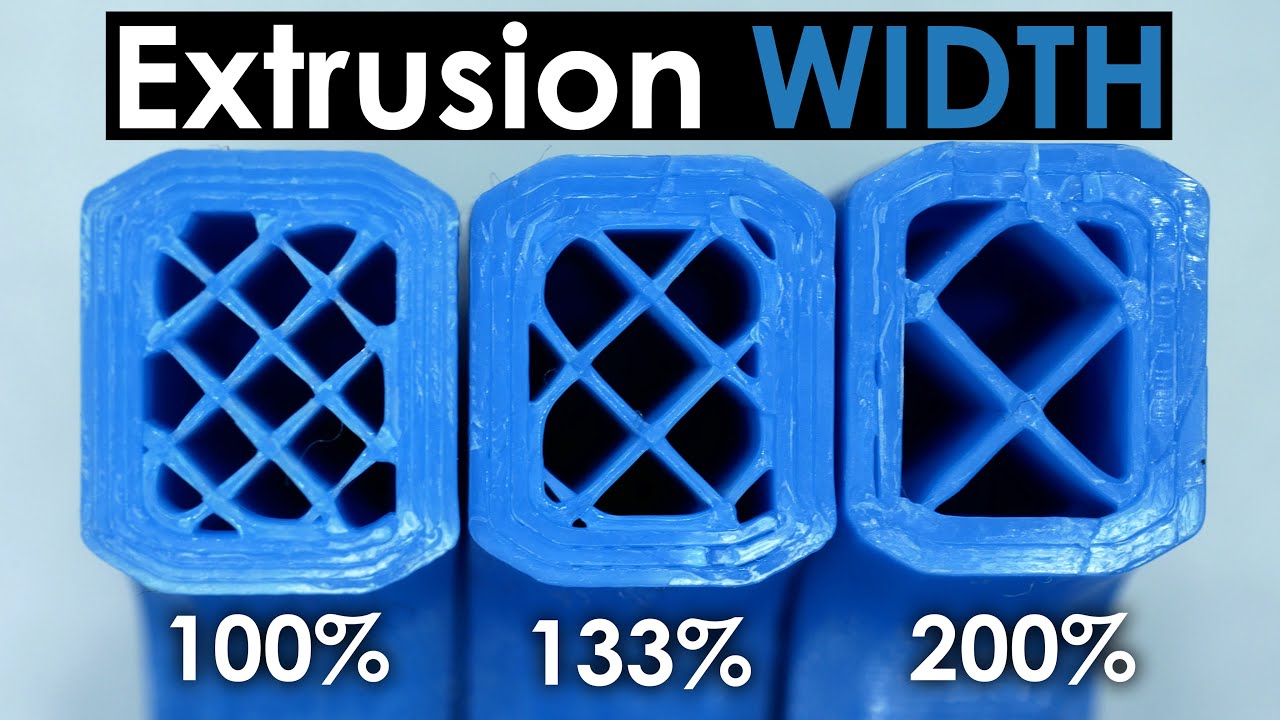
Показать описание
Extrusion width defines how wide the lines of extruded material are. Higher values require more pressure to squeeze the molten filament out of the nozzle that also presses the layers together. I investigated how different extrusion widths impact the quality and the strength of our 3D prints and discovered that this might be a way to produce strong prints in a short amount of time.
💚 Support me 💚
Join as a YouTube member!
🎙Check out my PODCAST with Tom Sanladerer
🛠Tested Materials
📚Papers and further information
⚙ My gear (Affiliate Links):
🎥 CAMERAS & LENSES
🎙AUDIO
🔴 LIVE STREAMING
🏆 Do you want to help me cover my running costs? Send me a dollar or two over PayPal, it helps me a lot!
🌼 Even watching the ads before my videos helps me a lot!
DISCLAIMER: This video was sponsored by Squarespace.
Extrusion Width - The magic parameter for strong 3D prints?
3D Printing at magical width #Shorts
Cura Questions - Nozzle Diameter VS Line Width
3D Printing Nylon - Useful Tips
Which LAYER HEIGHT gives you the STRONGEST 3D prints?
Hack #20 Larger Line Width
(HOW) I fixed the Ugly Layers on my 3D Printer
5-34 Advanced Extrusion width
Calibrating 3d Printer Flow Rate with Cura - The Quick Fix for Under Extrusion
printed WITHOUT support #shorts
BIG nozzles - HOW they (can) make your 3D prints STRONGER
Need…more…width! (here’s how)
Extruder Multiplier Calibration Test
0.4mm nozzles just became obsolete
What causes lines in the middle of a 3d print? Solve under extrusion problems mid print, halfway up!
Extrusion problems
Simplify3D Version 4 - Variable Extrusion Sizing & Dynamic Gap Fill
Hack #12 Top line width
3D Extrusion Printing of PHAs
Effect of extrusion FLOW RATE to the strength of 3D printed object
Which Layer Height Do You Print In? 3D Printing Resolutions Explained
magicPLA for a magic cube
Over extrusion (Timelapse)
Cos'è la Extrusion Width / Larghezza di estrusione ?
Комментарии