filmov
tv
How to TIG Weld Cast Iron with good success 440 engine block broken ear for 71 barracuda episode 10
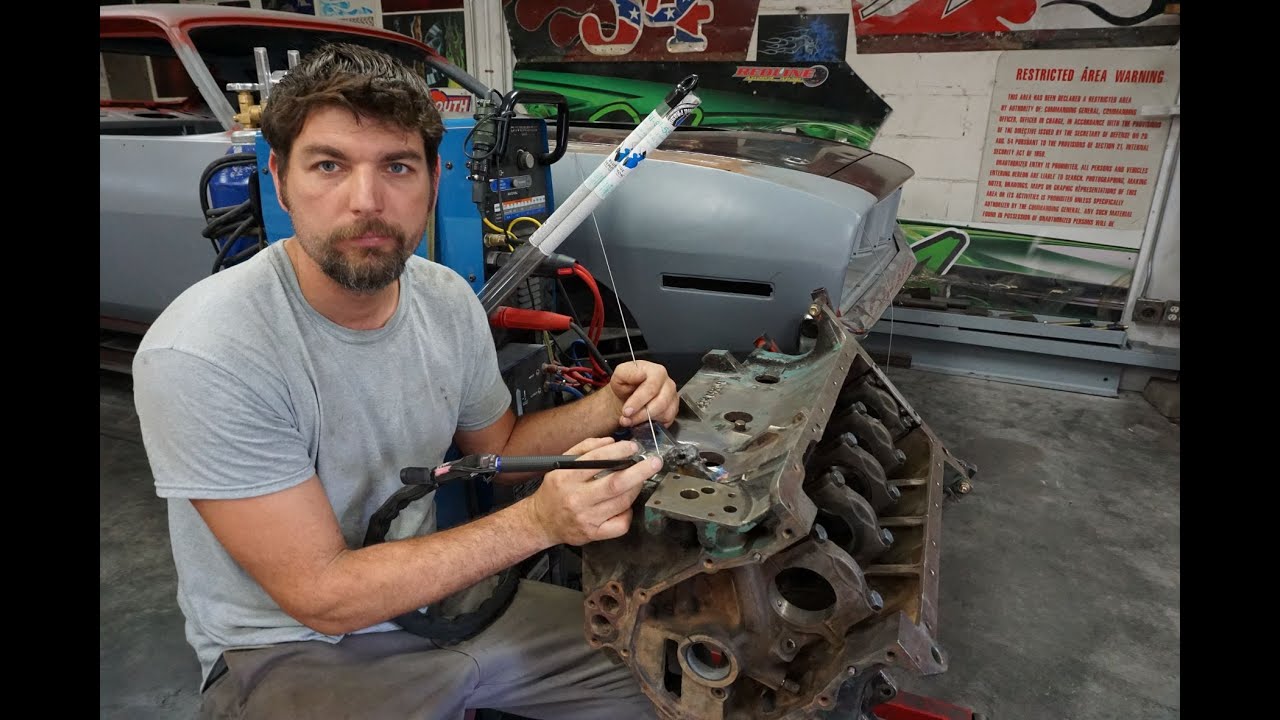
Показать описание
In this episode I go over how I have had success welding a 440 Cast Iron engine block for the 1971 Plymouth Barracuda we have in the shop. Correction to video I am DCEN not DCEP as stated on my settings normal DC TIG hookup with leads. I was multitasking and said the wrong thing. I give you a step by step walk through with lots of tips and tricks that might be able to help you with you cast welding project. If you have a Dodge tall deck big block you might have the same issue.
Thanks for watching if you like what you see and want to help support what we with putting out videos on this channel please visit our store and pick up a shirt, hat or a sticker.
#weldinglesson #440 #mopar
Thanks for watching if you like what you see and want to help support what we with putting out videos on this channel please visit our store and pick up a shirt, hat or a sticker.
#weldinglesson #440 #mopar
How to Weld Cast Iron NO Pre-Heating | TIG Time
Cast iron - Welding Manifold with TIG
TIG Welding Tips for Cast Aluminum | TIG Time
CAST ALUMINUM - A BASIC LESSON IN TIG WELDING IT
Aluminum Welding - Tips for Tig Welding Cast Aluminum parts
TIG Welding/Brazing Cast Iron Vise
TIG Cast Aluminum Repair Advice - TIG Welding
How to TIG Weld Cast Iron with good success 440 engine block broken ear for 71 barracuda episode 10
Tig Welding/Brazing Cast Iron to 409 Stainless
the DEFINITIVE GUIDE TO TIG WELDING BALANCE -How to TIG weld aluminum
Can You Weld Cast Iron??
cracked cast iron exhaust manifold repair Tig welding
How to TIG weld CAST IRON with 308LSi filler rod (cast engine manifold)
tig welding aluminum - 5 tips in 5 minutes
TIG Welding Cast Iron Repair with Muggy Weld
7 Tips for TIG welding Aluminum
Expert Tips and Techniques — TIG Welding Aluminum Parts
Cast Iron Welding Repair with Copper and Stainless TIG Brazing
How to TIG Weld Aluminum part 1
THE HIDDEN SECRET TO SUCCESSFULLY REPAIRING CAST ALUMINUM BY TIG WELDING
Beginner's Guide To TIG Welding Aluminum - Pro Tips & Tricks!
Welding Cast Aluminum and Q&A
TIG Welding Cast Aluminum - Jet Boat Bellhousing
Tig Welding Cast Aluminum Outboard Jet Pump
Комментарии