filmov
tv
3 ways to add a dual Z axis - Including G34 auto Z levelling
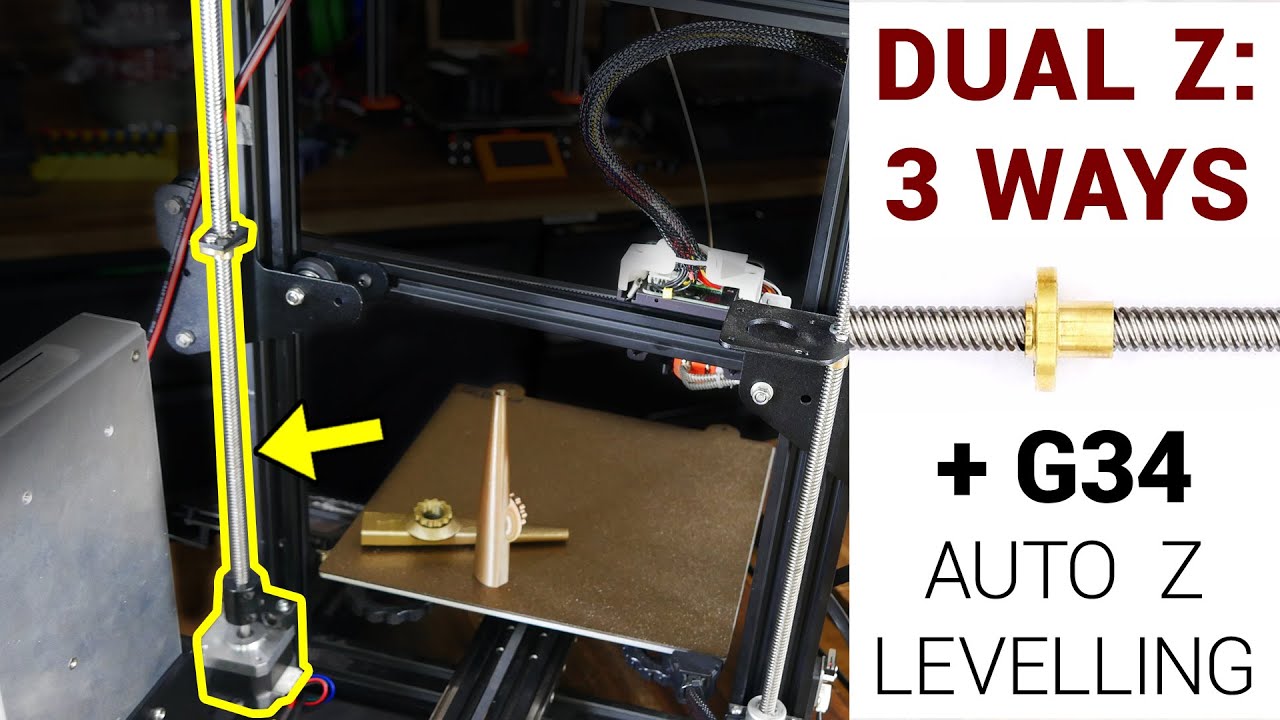
Показать описание
A patreon request: make a guide on how to add a second Z axis to an Ender 3. In this video we achieve that, showcasing three methods to get the gantry level. This includes a mechanical belt driven kit from TH3D, adding a 2nd stepper motor in parallel, and a 2nd firmware controlled stepper with G34 auto z levelling.
If you were looking to do this upgrade, hopefully one of these methods will be suitable for you!
Everything in this video was purchased with my own money. The links all point to TH3D for convenience only. 3D printed versions of the concept are linked below.
0:00 Introduction
0:42 Identifying the problem
1:56 Overview of the the three methods
3:06 Ender 3 PSU relocation
4:36 Option 1: Mechanical - belt driven leadscrew
7:48 Alignment
9:39 Option 2: 2nd stepper motor in parallel
12:39 Flexible coupler to remove Z banding
13:09 Option 3: 2nd stepper motor with G34 auto alignment
Purchase the BTT SKR E3 Turbo:
14:37 G34 minimum firmware changes
14:56 G34 default behaviour
16:11 G34 slicer start gcode change
16:28 G34 advanced firmware changes
17:59 Conclusion - You on Kazoo!
Get Quality Resins from 3D Printers Online. 5% off storewide for Teaching Tech subscribers [Code: tech5]
Take a look around and if you like what you see, please subscribe.
If you were looking to do this upgrade, hopefully one of these methods will be suitable for you!
Everything in this video was purchased with my own money. The links all point to TH3D for convenience only. 3D printed versions of the concept are linked below.
0:00 Introduction
0:42 Identifying the problem
1:56 Overview of the the three methods
3:06 Ender 3 PSU relocation
4:36 Option 1: Mechanical - belt driven leadscrew
7:48 Alignment
9:39 Option 2: 2nd stepper motor in parallel
12:39 Flexible coupler to remove Z banding
13:09 Option 3: 2nd stepper motor with G34 auto alignment
Purchase the BTT SKR E3 Turbo:
14:37 G34 minimum firmware changes
14:56 G34 default behaviour
16:11 G34 slicer start gcode change
16:28 G34 advanced firmware changes
17:59 Conclusion - You on Kazoo!
Get Quality Resins from 3D Printers Online. 5% off storewide for Teaching Tech subscribers [Code: tech5]
Take a look around and if you like what you see, please subscribe.
Комментарии