filmov
tv
Half Bridge – Thermal Compensating Gage.
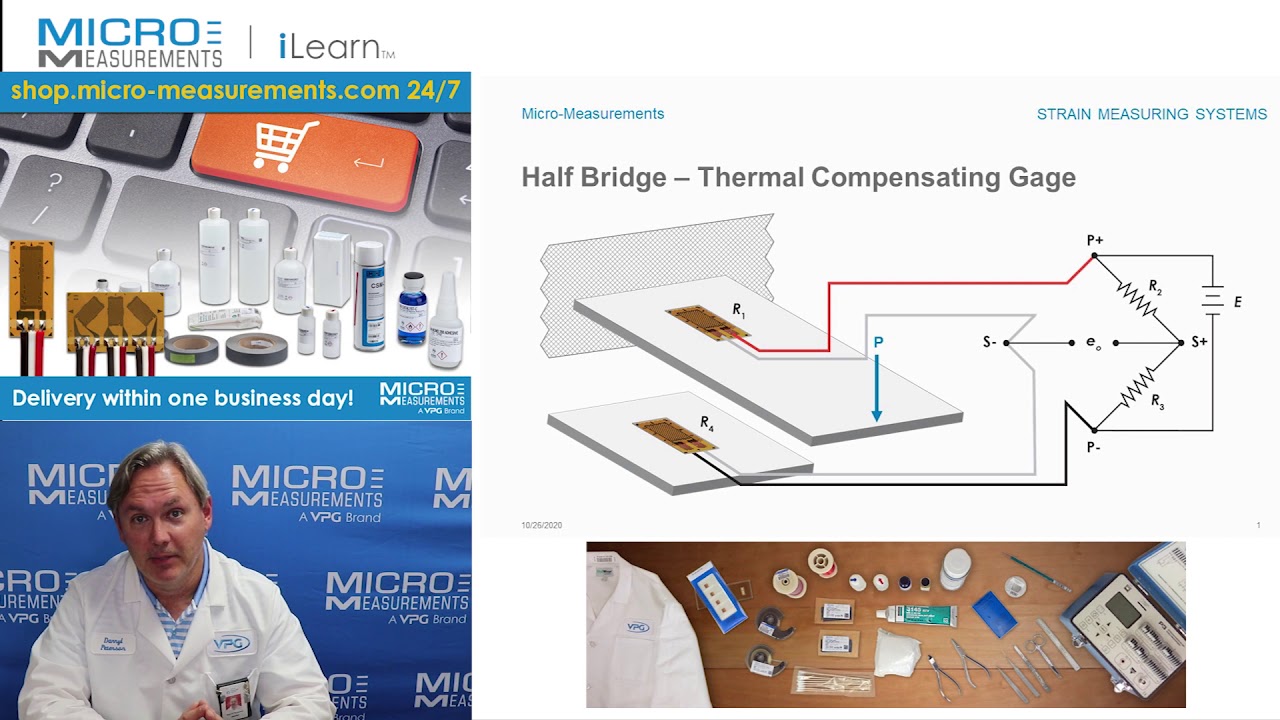
Показать описание
In this iLearn video, Darryl explains about temperature compensation by half-bridge strain gage design.
Once an installed strain gage is connected to a strain indicator and the instrument balanced, a subsequent change in the temperature of the gage installation will normally produce a resistance change in the gage. This temperature-induced resistance change is independent of, and unrelated to, the mechanical (stress-induced) strain in the test object to which the strain gage is bonded. It is purely due to temperature change, and is thus called the thermal output of the gage. Thermal output is potentially the most serious error source in the practice of static strain measurement with strain gages. In fact, when measuring strains at temperatures remote from room temperature (or from the initial balance temperature of the gage circuit), the error due to thermal output, if not controlled, can be much greater than the magnitude of the strain to be measured. At any temperature, careful consideration; and it is usually necessary to either provide compensation for thermal output or correct the strain measurements for its presence.
Once an installed strain gage is connected to a strain indicator and the instrument balanced, a subsequent change in the temperature of the gage installation will normally produce a resistance change in the gage. This temperature-induced resistance change is independent of, and unrelated to, the mechanical (stress-induced) strain in the test object to which the strain gage is bonded. It is purely due to temperature change, and is thus called the thermal output of the gage. Thermal output is potentially the most serious error source in the practice of static strain measurement with strain gages. In fact, when measuring strains at temperatures remote from room temperature (or from the initial balance temperature of the gage circuit), the error due to thermal output, if not controlled, can be much greater than the magnitude of the strain to be measured. At any temperature, careful consideration; and it is usually necessary to either provide compensation for thermal output or correct the strain measurements for its presence.
Half Bridge – Thermal Compensating Gage.
Lec 9 1 II Temperature Compensation Techniques for Strain Gauge
Compensating For Thermal Expansion in Standard Wheatstone Bridge Configuration
Strain Measurement
StrainSensingCompensation
Half (Wheatstone) Bridge – Poisson's Ratio.
How to Select a Strain Gage – Self Temperature Compensation (STC) - The Lazy S.
Double Your Output: Half (Wheatstone) Bridge – Bending.
Temperature Sensitivity Of Quarter Bridge Strain Gauges
Electronics: How does temperature compensation work for strain gauge in wheatstone bridge?
Do you know how to identify a (crash test) dummy strain gage? 👀
Lecture 9: Quarter and Half Wheatstone Bridge Configuration Under Bending Strain
II _ 2.6 Temperature effect and compensation | Strain Gauge and Strain Measurement | GTU Sem 7
Torque Measurement | Temperature compensation of resistance strain gauges | Lecture 05.11
temperature compensation methode in strain guage
HBM Webinar - Introduction to Strain Gauges
Electronics: Load cell temperature compensation
Part 15 I Dummy Gauges for Temperature Compensation
Strain gage for measuring Thermal Expansion Coefficient
Full (Wheatstone) Bridge – Bending.
Strain Gauge 4 - Temperature Correction.MP4
Are strain gage load cells (Weigh Modules) sensitive to temperature?
HBM Webinar - Compensating for Lead Resistances in Strain Gauge Applications
WBCircuits
Комментарии