filmov
tv
Brick Layers - Why did no one do this before?
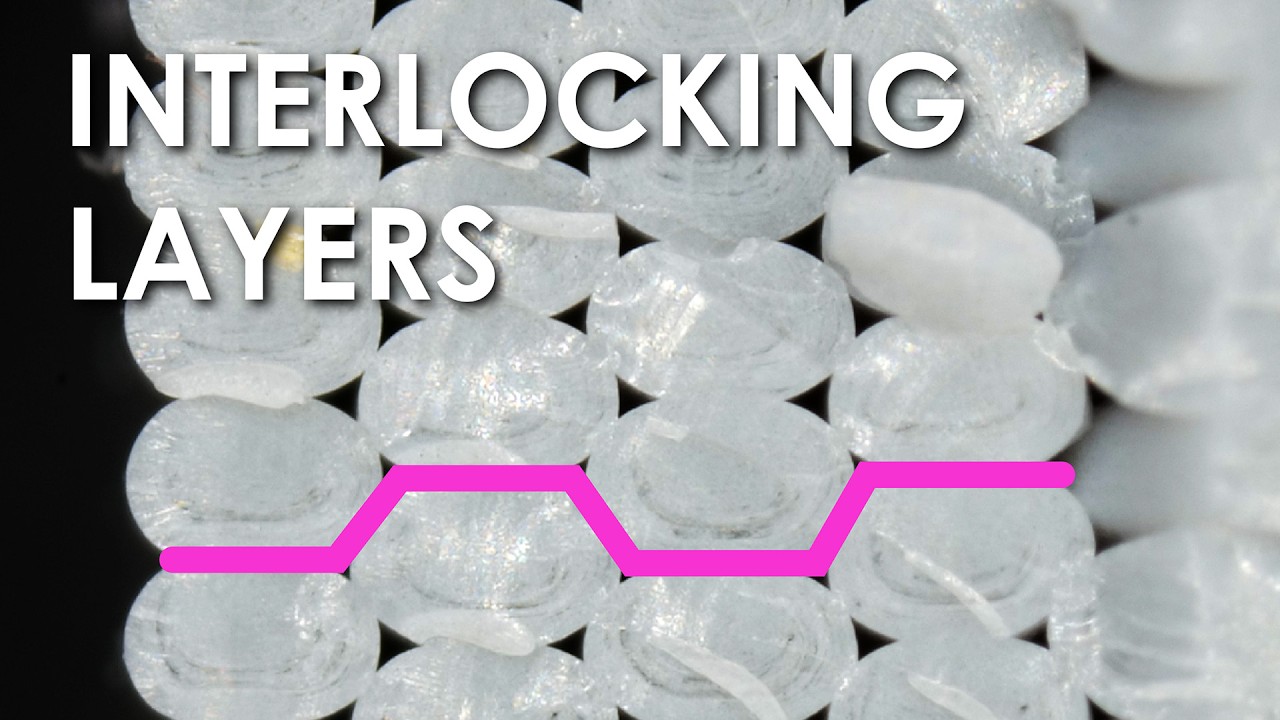
Показать описание
3D prints still suffer from bad layer adhesion due to their 2.5D slicing and printing approach. I investigated if a novel slicing method that interleaves the layer could improve the strength of 3D prints.
💚 Support me 🙏
Join as a YouTube member!
📚 Printed Models:
*Chapters*
00:00 Introduction
01:47 Brick Layers
04:20 Implementation in Simplify3D
04:55 Print Quality
05:55 Strength Tests
08:51 Summary
09:33 Sponsor
10:55 Outro
#3Dprinting #Slicing #Future
DISCLAIMER: Part of this video was sponsored by Brilliant.
FTC Disclaimer: A percentage of sales is made through Affiliate links
Brick Layers - Why did no one do this before?
THE REALITY OF BEING A BRICKY IN WINTER!! #bricklayer #bricklaying #short #construction #building
A very professional Masonry work specifically when you have to place the last brick@GIMS
Brick Layers: Stronger 3D Prints TODAY - instead of 2040 😬
Fastest Bricklayers in the Uk 😉
ASMR Bricklaying
The best technique to lay bricks fast #bricklaying
#asmr #bricklayingasmr #bricklaying #bricklayer #satisfying #brickwork l #pattersonconstruction
The Unseen Bricklayer: A Story About Purpose and Legacy #manifestation #motivation #quotes
Raised by the old school #bricklayer #bricklayers #subscribe #brickwork #mahoney #videos #bricks
The HARSH reality of being a bricklayer 👍🏻🧱#bricklaying #thetruth #timeoff
This is ESSENTIAL when bricklaying!! #brickwork #bricklayer #bricks #construction
Laying HEAVY hollow Blocks! #bricklaying #blocklaying #construction
Laying bricks on a miserable day 😞 #bricklaying #construction #brickwork
Neil demonstrating his bricklaying skills
Old bricklayer checking my work again #bricklaying
Working with an Apprentice Bricklayer
Bricklaying ASMR
Bricklaying Uk - Blockwork prices 😁
Meet two Bricklayers who explain the trade and the apprenticeship pathway.
Bricklaying - How To cavity Tray your corners ✅
New woke bricklayers wouldn’t even know 🇬🇧🧱 #bricklaying #bricklayer #patriot #diy #heritage...
Bricklaying SATISFYING #brickwork #asmr #construction
Bricklaying - Averaging 500 brick per Hour 💨
Комментарии