filmov
tv
Printing a High Performance Fuel Nozzle
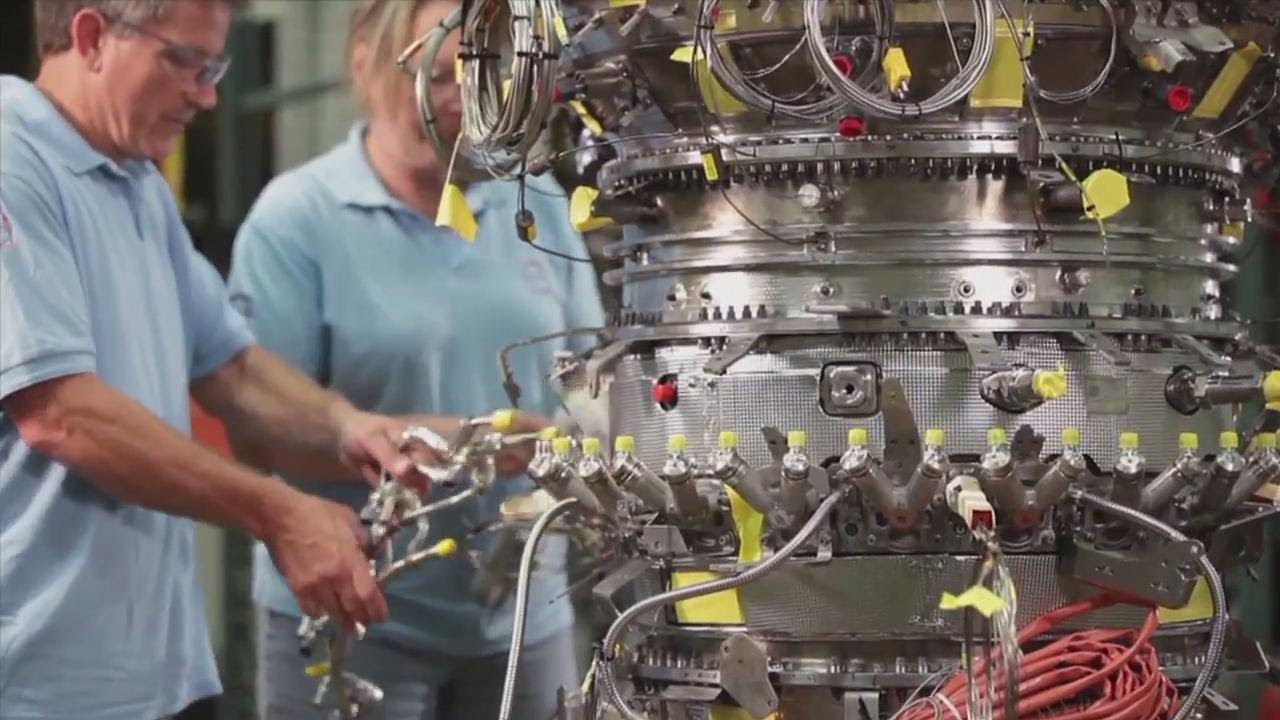
Показать описание
More than 40 metal 3D printers at a GE Aviation plant in Auburn, Alabama, have produced more than 30,000 fuel nozzles for the high performance LEAP engine. In this ASME video, the engineer who was given the task to design the fuel nozzle describes how he took on the challenge.
According to an announcement in March, 2019, by Alabama Governor Kay Ivey, GE Aviation is planning to invest an additional $50 million to expand the Auburn plant. In late 2018, the company reported it had produced 30,000 of the advanced fuel nozzles. And the company says it plans on increasing its staff at the plant in 2019 from 230 to 300 employees. The expansion will allow the Auburn facility to begin mass production of another 3D-printed engine part.
GE drew much attention in 2013 when it announced plans to move from prototyping to production with the 3D printed fuel nozzle. Production at the Auburn plan began in 2015.
When GE Aviation managers first decided it might use 3D printing for the fuel nozzle, they turned to design engineer Joshua Mook. In this video report, Mook explains that challenge. His design optimized the mixing of fuel and air using tiny, complex channels that could not be made with conventional machine tools. Engineering manager Mark Shaw, who had responsibility for developing a manufacturing pipeline for the nozzle, describes how his team realized they could print in one piece what would have been 20 parts in a conventional nozzle. Additive Manufacturing pioneer Greg Morris is also featured in this report. Morris describes how advances in metal 3D printing led to the use of the technology for production.
The LEAP engine is a joint venture between GE Aviation and France's Snecma.
This ASME video was originally produced in 2013, shortly after GE Aviation announced its ambitious plans for the fuel nozzle. The video was produced by ASME’s Roger Torda.
According to an announcement in March, 2019, by Alabama Governor Kay Ivey, GE Aviation is planning to invest an additional $50 million to expand the Auburn plant. In late 2018, the company reported it had produced 30,000 of the advanced fuel nozzles. And the company says it plans on increasing its staff at the plant in 2019 from 230 to 300 employees. The expansion will allow the Auburn facility to begin mass production of another 3D-printed engine part.
GE drew much attention in 2013 when it announced plans to move from prototyping to production with the 3D printed fuel nozzle. Production at the Auburn plan began in 2015.
When GE Aviation managers first decided it might use 3D printing for the fuel nozzle, they turned to design engineer Joshua Mook. In this video report, Mook explains that challenge. His design optimized the mixing of fuel and air using tiny, complex channels that could not be made with conventional machine tools. Engineering manager Mark Shaw, who had responsibility for developing a manufacturing pipeline for the nozzle, describes how his team realized they could print in one piece what would have been 20 parts in a conventional nozzle. Additive Manufacturing pioneer Greg Morris is also featured in this report. Morris describes how advances in metal 3D printing led to the use of the technology for production.
The LEAP engine is a joint venture between GE Aviation and France's Snecma.
This ASME video was originally produced in 2013, shortly after GE Aviation announced its ambitious plans for the fuel nozzle. The video was produced by ASME’s Roger Torda.