filmov
tv
Bowden 3d Printer Extruder Vs. Direct Drive
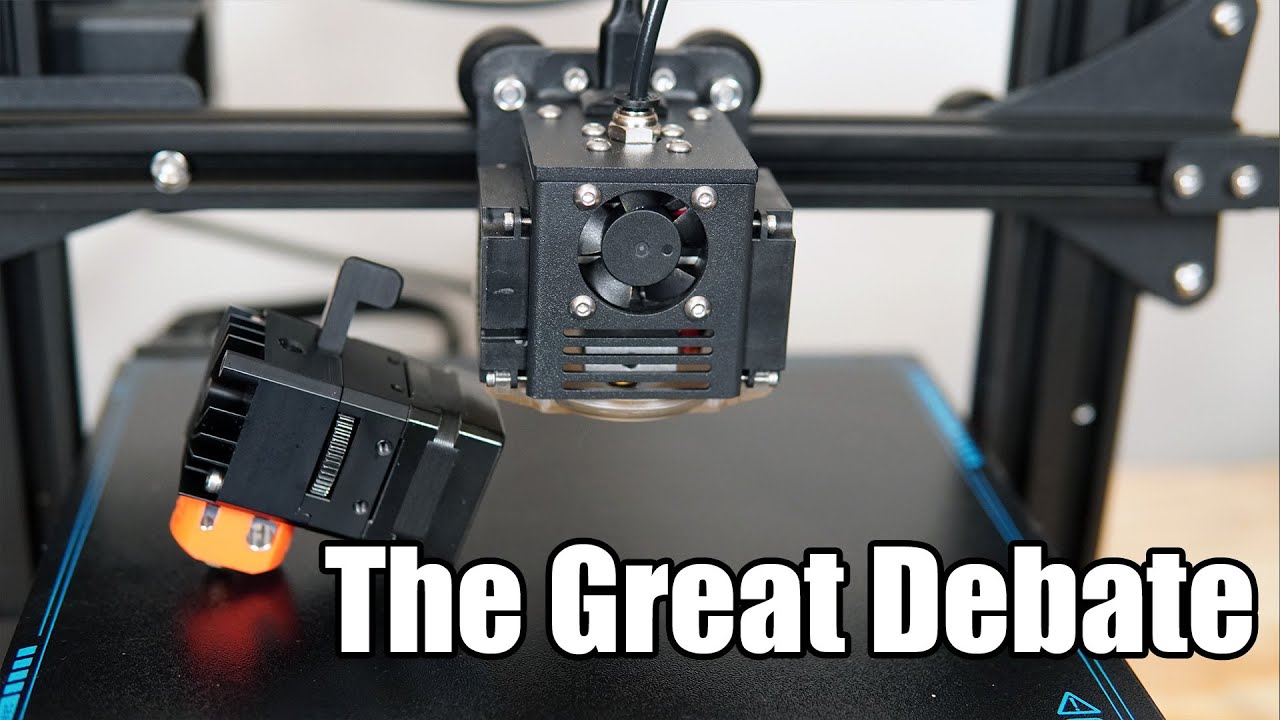
Показать описание
Love the channel? Consider supporting me on Patreon:
In this video, we take a look at the key differences between a bowden 3d printer extruder and a direct drive extruder. We will cover the pros and cons of each and discuss which extruder type may be best for your specific applications.
(´∀`)♡ As an Amazon Associate I earn from qualifying purchases:
Lets Get Social!
Music provided by Argofox:
NEREUS - Lotus
In this video, we take a look at the key differences between a bowden 3d printer extruder and a direct drive extruder. We will cover the pros and cons of each and discuss which extruder type may be best for your specific applications.
(´∀`)♡ As an Amazon Associate I earn from qualifying purchases:
Lets Get Social!
Music provided by Argofox:
NEREUS - Lotus
Bowden 3d Printer Extruder Vs. Direct Drive
Direct-Drive VS. Bowden
Is BOWDEN DEAD? Direct Drive vs. Bowden DEEP DIVE on Voron Zero
Simple comparison between Bowden & Direct drive extruder #3dprinter
Next generation direct drive extruder gear system for 3d printing
Faster 3d Printers, Bowden vs Direct Extruder, Creality Ender 3 v2 vs Ender 5
Essential First Upgrade That Will Actually Improve Your Bowden Tube 3d Printer! A Capricorn Tube!
Why direct drive is not automatically better than bowden tube
Anycubic Kobra: Fastest Budget 3D Printer?
Improve Ender 3 print quality: OMG DM1 dual gear lightweight direct drive extruder upgrade
micro swiss Ng. VS. the creality Sprite extruder on the ender 3 pro
3D Printer - Bowden Extruder Setup
What is a Direct Drive Extruder? And Why Would You Need One? #3dprinting #shorts #ender3
Should you use a Reverse Bowden?
How to unclog any Bowden or Direct Drive Extruder? - NoClogger The Must-Have 3D Printing Tool
High-Ratio 3D Printer EXTRUDERS – MUST HAVE? or STUPID?
Fixing a Clogged Ender 3 V3 SE 3D Printer Extruder in 40s #3dprinter
Battle: Comparing SV01 and SV02! Direct-Drive vs Bowden-Dual-Extruder
Bowden Tube... Direct Drive Extruder... WHY?!
I tried to find the Strongest Filament Extruder.
Best Bowden Extruder In 2023
PERBEDAAN EXTRUDER BOWDEN VS DIRECT
Why Direct Drive Beats Bowden Tube
Quality of print with direct drive vs bowden extruder on my MakerGear M2 printer
Комментарии