filmov
tv
Foundation Waterproofing
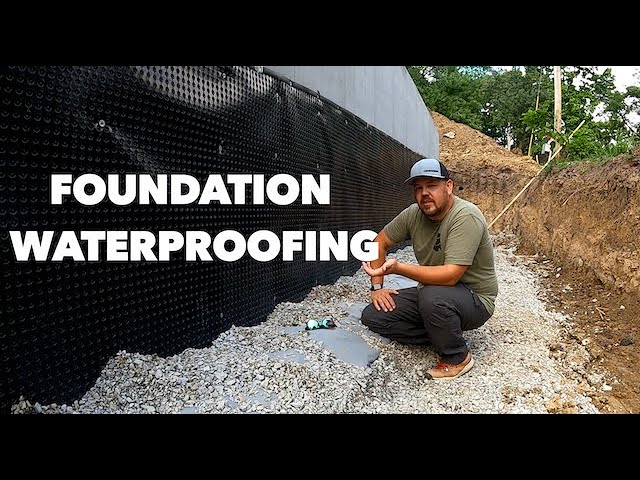
Показать описание
It will be buried beneath soil, concrete, landscaping, driveways, pool, patios, and so much more. All of that combines to mean we have to get it correct the first time. Drain and dry, down and out. Water away from the foundation and not held in tension is key.
.
.
#aarowbuilding #comobuilds #kcmobuilds #foundations #foundationwaterproofing #watermanagementsystem #dimplemat #coatings #builditbetter #construction #longliveourbuildings
.
.
#aarowbuilding #comobuilds #kcmobuilds #foundations #foundationwaterproofing #watermanagementsystem #dimplemat #coatings #builditbetter #construction #longliveourbuildings
Foundation Waterproofing Tutorial
Foundation Waterproofing Membrane
How to do Exterior Basement Waterproofing - Aquatech Basement Waterproofing (2023)
ICF FOUNDATION MEMBRANE : the RIGHT Waterproofing Solution for Your ICF Foundation
waterproofing for roof | waterproofing for terrace #waterproofing #shotrs
Basement Waterproofing - How To Permanently Waterproof A Basement
How to Waterproof Basement Walls With Flex Seal Products
How To Waterproof Basement Walls Using Rub-R-Wall
Eu Resolvi o Problema do Rodapé Com Umidade e Você Pode Fazer o Mesmo
Basement Waterproofing: How To Keep Your Basement Dry
Basement Waterproofing 101: Which System is Right for Your Project?
Waterproofing Your Basement Prevents Mold, Leaks, and Moisture! #basementwaterproofing #wetbasement
exterior foundation waterproofing
Professional Basement Waterproofing Systems | WATERPROOF.COM Contractor Membership Program
Waterproofing Basement Walls with DRYLOK® Paint -- by Home Repair Tutor
Blue Max® Liquid Rubber Basement Waterproofing
Foundation Waterproofing - Bomber Method
French Drain and Foundation Waterproofing System
B-Dry Waterproofing
ICF Waterproofing with PolyWall Building Solutions
Professional Basement Waterproofing Supplies
Rexoseal Concrete & Crack Repair Waterproofing Sealant - DIY Foundation Waterproofing System
RUB-R-WALL AQUA Waterproofing for Foundation
All Basement Waterproofing Steps within 1 minute #shorts
Комментарии