filmov
tv
What is Strain Wave Gear a.k.a. Harmonic Drive? A Perfect Gear Set For Robotics Applications!?
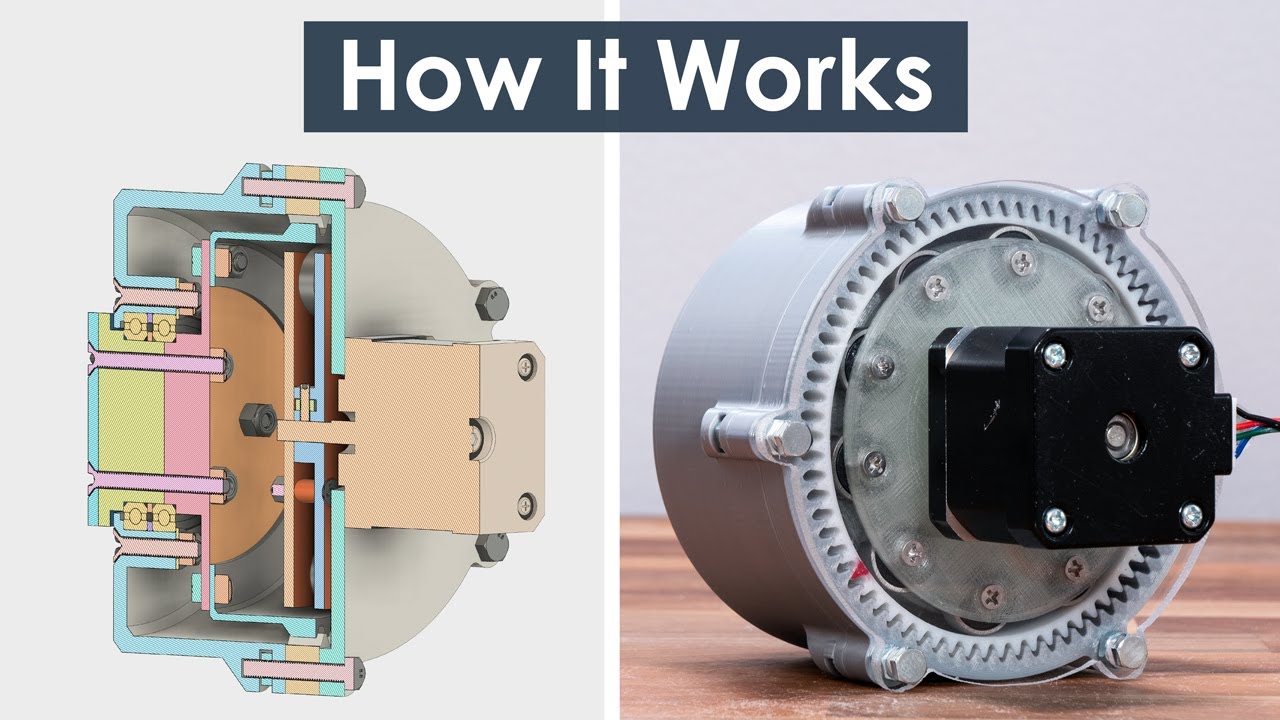
Показать описание
In this tutorial we will learn what is Strain Wave Gear, also known as Harmonic Drive.
Like my page on Facebook:
What is Strain Wave Gear a.k.a. Harmonic Drive? A Perfect Gear Set For Robotics Applications!?
Harmonic Drive® Strain Wave Gear: Functional Principle | The Original
You NEED to know this BEFORE buying! Strain Wave Gear/Harmonic Mount Specs EXPLAINED!
Harmonic Drives explained
Harmonic Drive® strain wave gear - zero backlash
ROBOTICS | Measuring repeatability of a strain wave gear from Harmonic Drive
Harmonic Drive® Strain Wave Gear Principle | Harmonic Drive SE
Strain Wave Gear
Harmonic vs Cycloidal Drive - Torque, Backlash and Wear Test
About Strain Wave Gearing
Nema17, 3D Printed Strain Wave Gear (Harmonic Drive)
Strain Wave Gear (Harmonic Drive) Wave Generator Balls
Tribological Aspects of A Strain Wave Gearing System (Harmonic Gear)
Strain Wave Gear | Elitewave® | KOFON® KB-HO typical connections
igus® new generation strain wave gears in robolink® ReBeL 2020
igus® drygear® RL-S New generation strain wave gear
SureServo Strain Wave Gearbox - How it works from AutomationDirect
3D Printed Strain Wave Gear Gets Stronger
Strain Wave Gear Prototype - 3D Printing
How to choose harmonic drive? Selection of strain wave gears#mechanical #automation #machines
How to install LHT series strain wave gear? See here:
SMD Harmonic Gearbox Strain Wave Gear Principle
Strain Wave Gear by ZeroBacklashRobotics
3D Printed Strain Wave Gear: First Design Revision
Комментарии