filmov
tv
Hammer-Forming Boiler Parts - Pennsylvania A3 Switcher, Part 2
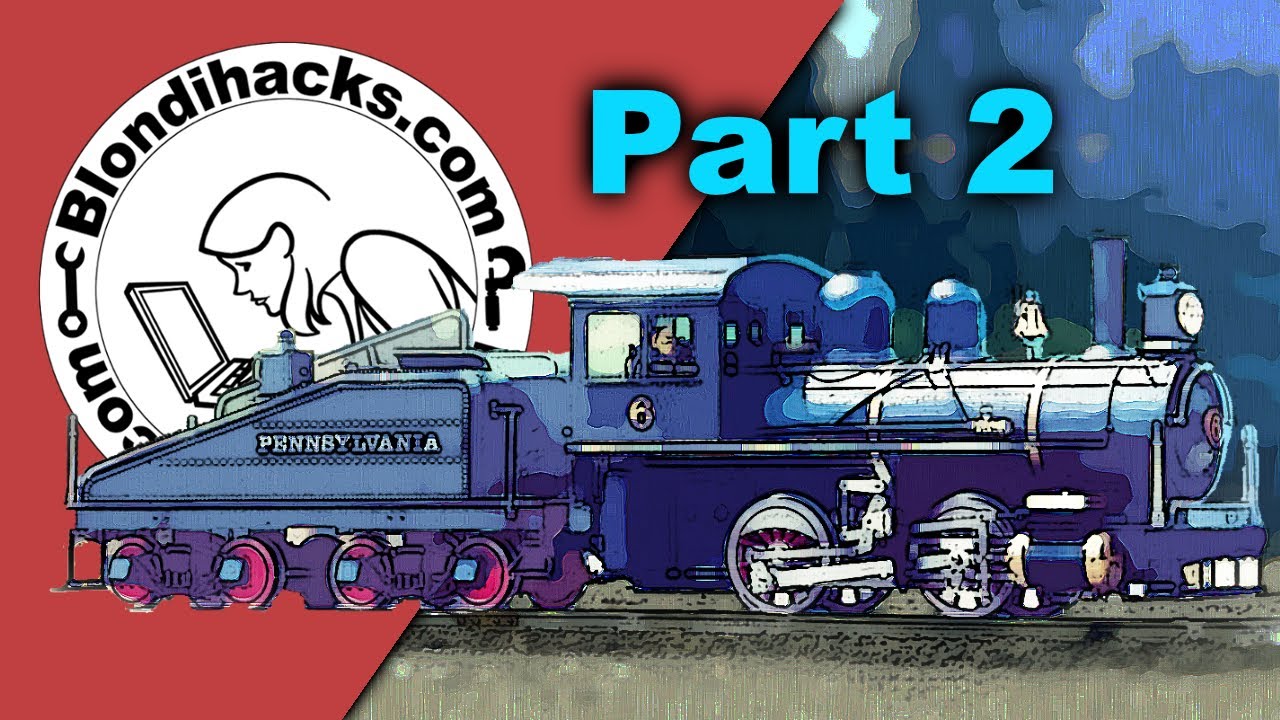
Показать описание
This episode on Blondihacks, I’m doin’ stuff! Exclusive videos, drawings, models & plans available on Patreon!
Here are links for many of the tools that you see me using:
(I earn small commissions on these links)
Want more content like this? Try these places:
As an Amazon Associate, I earn from qualifying purchases.
Here are links for many of the tools that you see me using:
(I earn small commissions on these links)
Want more content like this? Try these places:
As an Amazon Associate, I earn from qualifying purchases.
Hammer-Forming Boiler Parts - Pennsylvania A3 Switcher, Part 2
Finishing Boiler Bulkheads - Pennsylvania A3 Switcher, Part 3
Lathe Machine Actual video accidents #shorts #short
Boiler Outer Crown Sheet - Pennsylvania A3 Switcher, Part 8
Finishing The Boiler Shell - Pennsylvania A3 Switcher, Part 6
Let's Build a Locomotive! Pennsylvania A3 Switcher, Part 1
Growing up Pentecostal... #short
Rolling The Boiler Shell - Pennsylvania A3 Switcher, Part 4
Pressure Testing the Boiler Shell! Pennsylvania A3 Switcher, Part 7
Building a Firebox! Pennsylvania A3 Switcher, Part 9
Foundation Ring and Backhead! Pennsylvania A3 Switcher, Part 11
Metal shaping for beginners. Finishing the hammer form to create a patch panel from scratch bdp#10
Restoration of the rare straightening hammer. Made in the USSR.
Very resourceful GIRL 🤯 #camping #survival #bushcraft #outdoors
Tender Water Tank - Pennsylvania A3 Switcher, Part 21
Adding Boiler Features - Pennsylvania A3 Switcher, Part 5
A Big Error! Pennsylvania A3 Switcher, Part 23
Manufacturing process of cast iron pans by melting iron in a 1500°C furnace.
SIMPLEX PRAIRIE TANK - PART #82
Denmark official faints during Covid-19 conference
Train Vs. Metal Things Experiment OMG Ohh Noo 😳 || Train Experiments @TrainExperiments
Trucker Ran Off On The Lot Lizard 🚛💨🦎 #trucker #lotlizard #fyp
Pressure Testing The Firebox! Pennsylvania A3 Switcher, Part 10
Albert Einstein doing physics | very rare video footage #shorts
Комментарии