filmov
tv
Problem Definition (Lean Problem Solving: Steps to Defining a Problem)
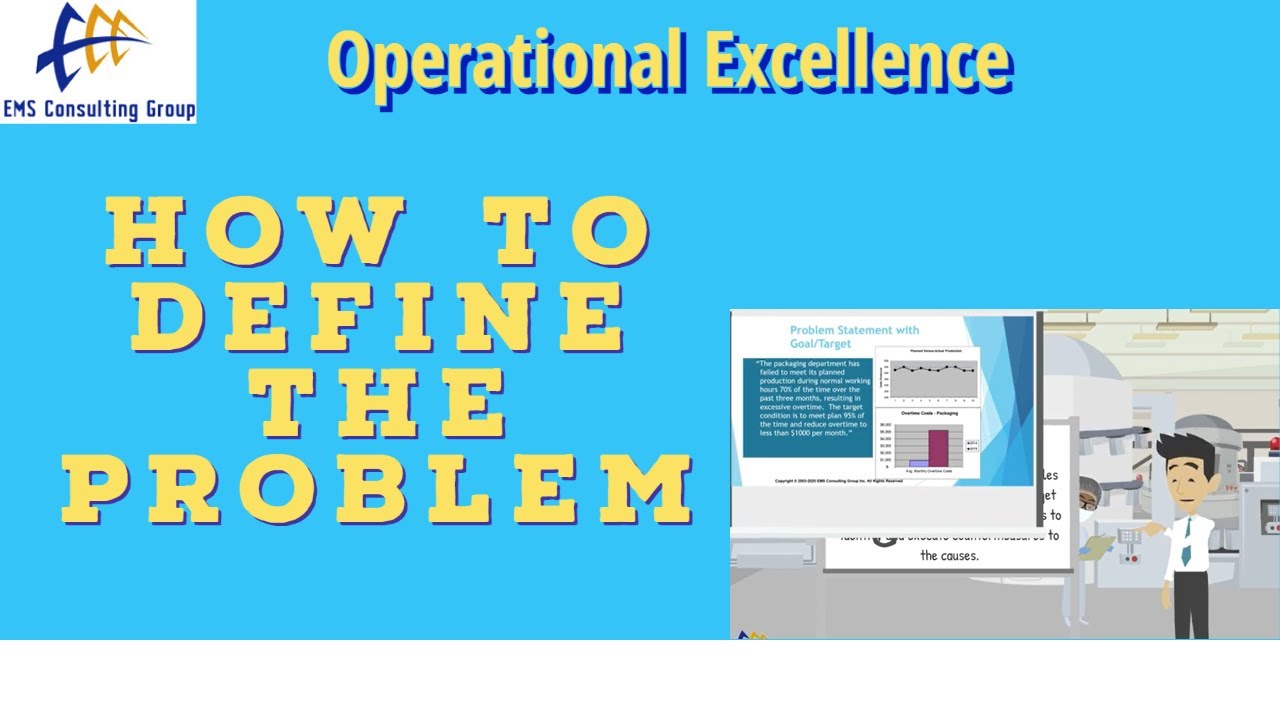
Показать описание
How to Define the Problem. Lean is all about problem solving. Six Sigma is also a problem solving process. Defining the problem is a very critical step in problem solving. How do we properly define the problem? Presented by EMS Consulting Group, Inc.:
#opexminute #kaizen #problemsolving #leanmanufacturingmanagement #leanmanagement #valuestream #a3
Welcome to today’s edition of the OpEx Minute, presented by EMS Consulting Group. Today we will be talking about Defining Problems. Whether you are using the Six Sigma DMAIC approach or Lean problem solving approach or even 8D, it is critical to understand how to define problems properly.
What most people think of as a problem is too narrow a definition. We define a problem as the gap between the current condition and a target condition or standard. This broad definition will allow for an array of problems at multiple levels. Any good problem solving process will aim to identify the primary causes or obstacles preventing us from reaching the target condition or standard and then allow us to identify and execute countermeasures to the causes. There will also be follow-up and monitoring.
In order to define problems, we need 4 key pieces of information.. First, the actual performance of the process. Next, the desired performance or goal. Then, we need to quantify the gap or magnitude of the problem- what is the difference between actual and desired performance? Finally, we need to know what the characteristics of the problem are. Is the problem worsening, for example? Let’s look at a problem statement.
“The packaging department has failed to meet its planned production during normal working hours 70% of the time over the past three months, resulting in excessive overtime. The target condition is to meet plan 95% of the time and reduce overtime to less than $1000 per month.” This problem statement is fairly well-stated. We have a chart that illustrates our failure to meet target on a consistent basis. We also have a chart that shows the overtime costs, which describes the impact of the problem..
There is much more you can do to help define a problem including some tools for refining problem definitions, and we are planning on covering those in future OPEX minutes. We provide coaching and training in problem solving for a wide variety of organizations across many industries.
#opexminute #kaizen #problemsolving #leanmanufacturingmanagement #leanmanagement #valuestream #a3
Welcome to today’s edition of the OpEx Minute, presented by EMS Consulting Group. Today we will be talking about Defining Problems. Whether you are using the Six Sigma DMAIC approach or Lean problem solving approach or even 8D, it is critical to understand how to define problems properly.
What most people think of as a problem is too narrow a definition. We define a problem as the gap between the current condition and a target condition or standard. This broad definition will allow for an array of problems at multiple levels. Any good problem solving process will aim to identify the primary causes or obstacles preventing us from reaching the target condition or standard and then allow us to identify and execute countermeasures to the causes. There will also be follow-up and monitoring.
In order to define problems, we need 4 key pieces of information.. First, the actual performance of the process. Next, the desired performance or goal. Then, we need to quantify the gap or magnitude of the problem- what is the difference between actual and desired performance? Finally, we need to know what the characteristics of the problem are. Is the problem worsening, for example? Let’s look at a problem statement.
“The packaging department has failed to meet its planned production during normal working hours 70% of the time over the past three months, resulting in excessive overtime. The target condition is to meet plan 95% of the time and reduce overtime to less than $1000 per month.” This problem statement is fairly well-stated. We have a chart that illustrates our failure to meet target on a consistent basis. We also have a chart that shows the overtime costs, which describes the impact of the problem..
There is much more you can do to help define a problem including some tools for refining problem definitions, and we are planning on covering those in future OPEX minutes. We provide coaching and training in problem solving for a wide variety of organizations across many industries.