filmov
tv
How Many Threads Does Nut Need To Be Strong?
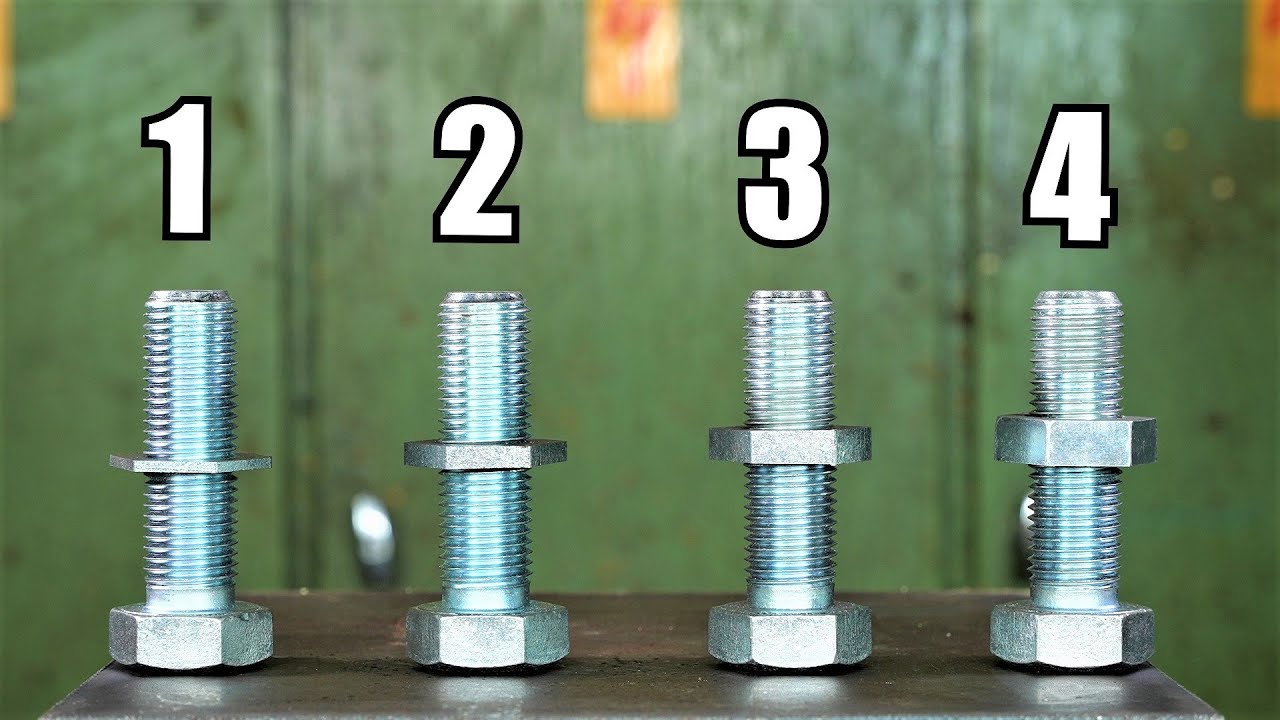
Показать описание
How Many Threads Does Nut Need To Be Strong? Or how about bolt? How strong is one thread? how about two? We are going find out using our 150 ton hydraulic press and 240 ton force sensor / load cells!
Do not try this at home!! or at any where else!!
Music Thor's Hammer-Ethan Meixell
Do not try this at home!! or at any where else!!
Music Thor's Hammer-Ethan Meixell
How Many Threads Does Nut Need To Be Strong?
Nylon lock nut will be tighter
nut and size with mm
How to Measure Bolts, Nuts and Screws Using a Thread Gauge Size Tool
How many people know this trick with a Wing Nuts?
Nut and Bolt Thread Checker
Nylon Insert Lock Nuts - Vibration Resistant Nuts | Fasteners 101
Thread locking | nut locking
Convert nearly anything to French Cleat with Rhino Frame's French Cleat Nut
The Best Way to 3D Print Threads; Nuts, and Bolts
Spin nuts on long threaded rod quickly and easily. #easyhacks #diy #howto#easyway#threaded
Bolt and nut measurement
🔩 how to use THREAD gages to recognize nuts and bolts
How to Installing a Rivet nuts | Riv nuts | Nutsert | thread inserts for thin metal
Nut internal thread inspection process- Good tools and machinery can increase work efficiency
243. Replacing thumb nuts with hex nuts #mtbitesize #nuts #jigmaking
How To Easily Remember Which Way To Tighten Or Loosen Nuts Or Screws - Let Me Show You How
Learn how you can repair damaged threads on nuts and bolts
double start, left/ right hand thread, bolt and nut #lathe #bolt #nut #machining
Getting a nut on a bolt with stripped threads
Removing rusted and seized nut and bolt! #restoration #metalworking #workshop #tools #rust
How to Tell a Nut or Bolt Size the Easy Way
Round nut thread tapping process- Good tools and machinery can increase work efficiency
Lug Nuts | Wheel Tips
Комментарии