filmov
tv
RDWorks Learning Lab 114 Can We Dither Greyscale images
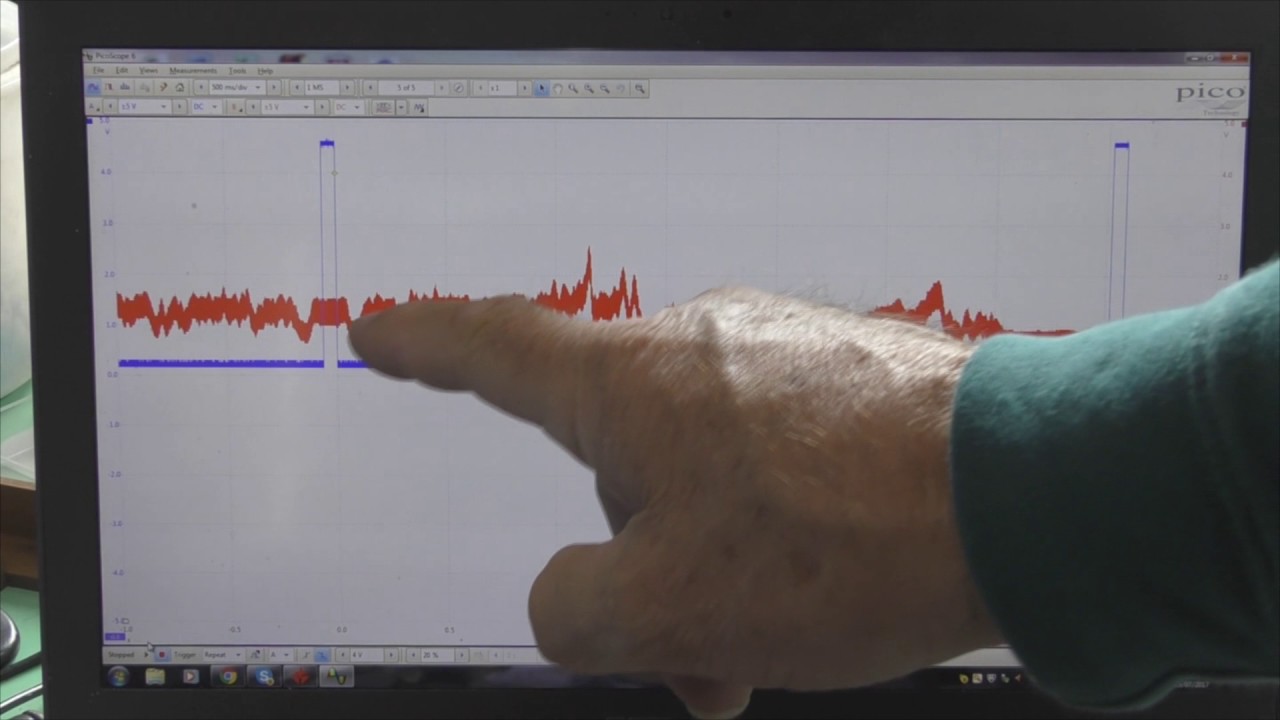
Показать описание
If you own a Chinese laser cutter this little series of videos about me learning how to use the free software provided, may solve the problem of trying to learn from a virtually unreadable manual.
I am nothing to do with RD Works, I am not an instructor and I am no expert. This series will document the essential bits of many hours of trial and error
I am nothing to do with RD Works, I am not an instructor and I am no expert. This series will document the essential bits of many hours of trial and error
RDWorks Learning Lab 114 Can We Dither Greyscale images
RDWorks Learning Lab 113 What the FACULA is going on
RDWorks Learning Lab 33 Solar LED edge lit sign
RDWorks Learning Lab 226 Can my Beam Collimator Work
RDWorks Learning Lab 112 Checking those Dots with an Oscilloscope
RDWorks Learning Lab 80 My Chinese Pizza Oven!!
RDWorks Learning Lab 120 Strange properties of acrylic
RDWorks Learning Lab 117 Hunting those Phantom Pixels
RDWorks Learning Lab 104 Dithered Graphics Not What They Seem
RDWorks Learning Lab 108 Going Dotty Pt3
RDWorks Learning Lab 207 The Importance of Beam Intensity
RDWorks Learning Lab 126 3D Engraving Is this the FINAL Chapter Part 1
RDWorks Learning Lab 215. AT LAST!!! I understand how lenses cut.
RDWorks Learning Lab 232 Beam Expansion Means Degraded Cutting
RDWorks Learning Lab 228 Search for a Beam Collimator Part 1
RDWorks Learning Lab 106 Going Dotty Part 1
RDWorks learning Lab 194 I seem to have lost my FOCUS
RDWorks Learning Lab 224 Blue Dream Begins it's Test work
RDWorks Learning Lab 247 PWM Grayscale Engraving
RDWorks Learning Lab 89 Axis Squareness Issue
RDWorks Learning Lab 69 Rotary Cermarking of glass
RDWorks Learning Lab 210 Lets Focus on Focus AGAIN
RDWorks Learning Lab 56 Engraving Pt1 History and Greyscale
RDWorks Learning Lab 109 Joining the dots Part 4
Комментарии