filmov
tv
The TRUE COST of CNC machining!
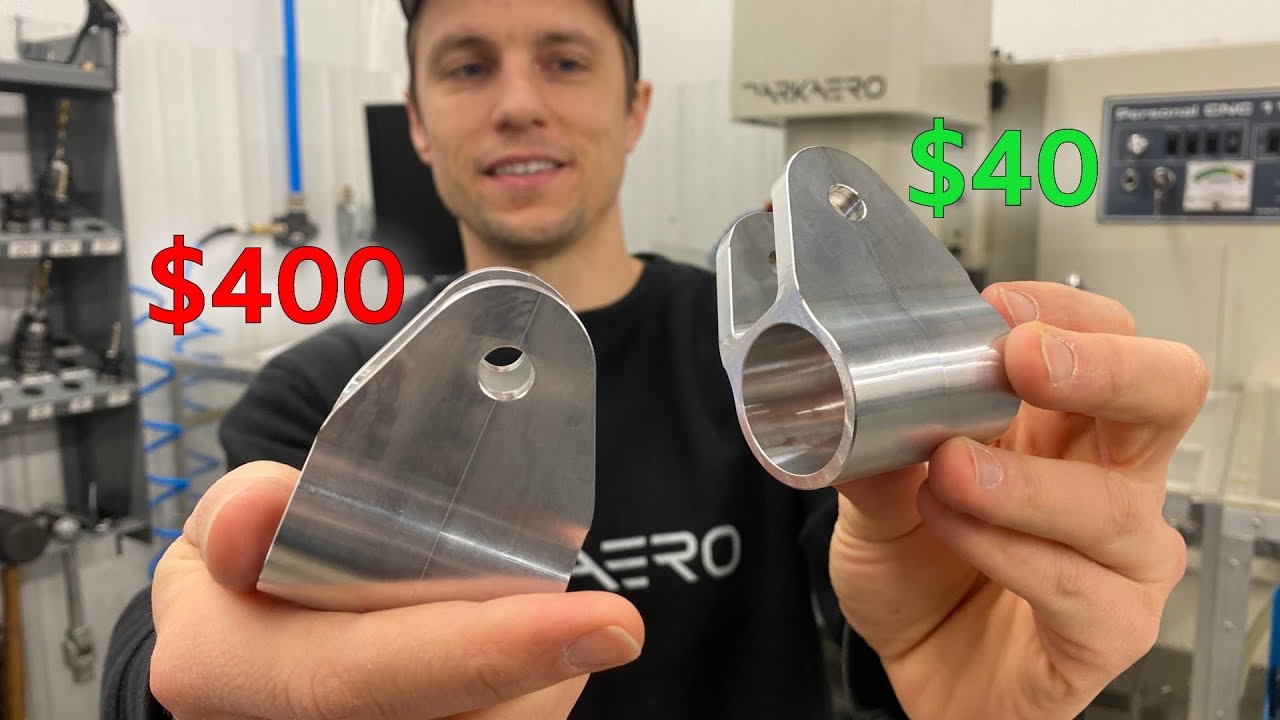
Показать описание
(Exclusive members only content including photos, videos, live Q&A and more!)
How much does it cost to make a CNC machined part? The answer depends on a number of variables like the material type, part quantity, dimensional tolerances, lead time, and surface finish. We demonstrate this using the two shock bottom brackets we CNC machined for the landing gear on the DarkAero 1 prototype. They were made in house on our Tormach from 7075-T6 aluminum. Quoting tools from Xometry offer a quick and easy way to see the cost of machining these parts if we were to outsource them. We uploaded a 3D CAD file of the shock bottom bracket to Xometry and then looked at the instant quote numbers to see where the cost might land in production.
Links to tools we use for CNC machining:
If you enjoyed this video and would like to see more of this type of content, follow along as we work to create the fastest, longest range aircraft you can build in your garage!
More information on DarkAero can be found on our website and other social media accounts:
00:00 - Intro
00:36 - Machining
04:37 - Cost
How much does it cost to make a CNC machined part? The answer depends on a number of variables like the material type, part quantity, dimensional tolerances, lead time, and surface finish. We demonstrate this using the two shock bottom brackets we CNC machined for the landing gear on the DarkAero 1 prototype. They were made in house on our Tormach from 7075-T6 aluminum. Quoting tools from Xometry offer a quick and easy way to see the cost of machining these parts if we were to outsource them. We uploaded a 3D CAD file of the shock bottom bracket to Xometry and then looked at the instant quote numbers to see where the cost might land in production.
Links to tools we use for CNC machining:
If you enjoyed this video and would like to see more of this type of content, follow along as we work to create the fastest, longest range aircraft you can build in your garage!
More information on DarkAero can be found on our website and other social media accounts:
00:00 - Intro
00:36 - Machining
04:37 - Cost
Комментарии