filmov
tv
one machine for PCB assembly
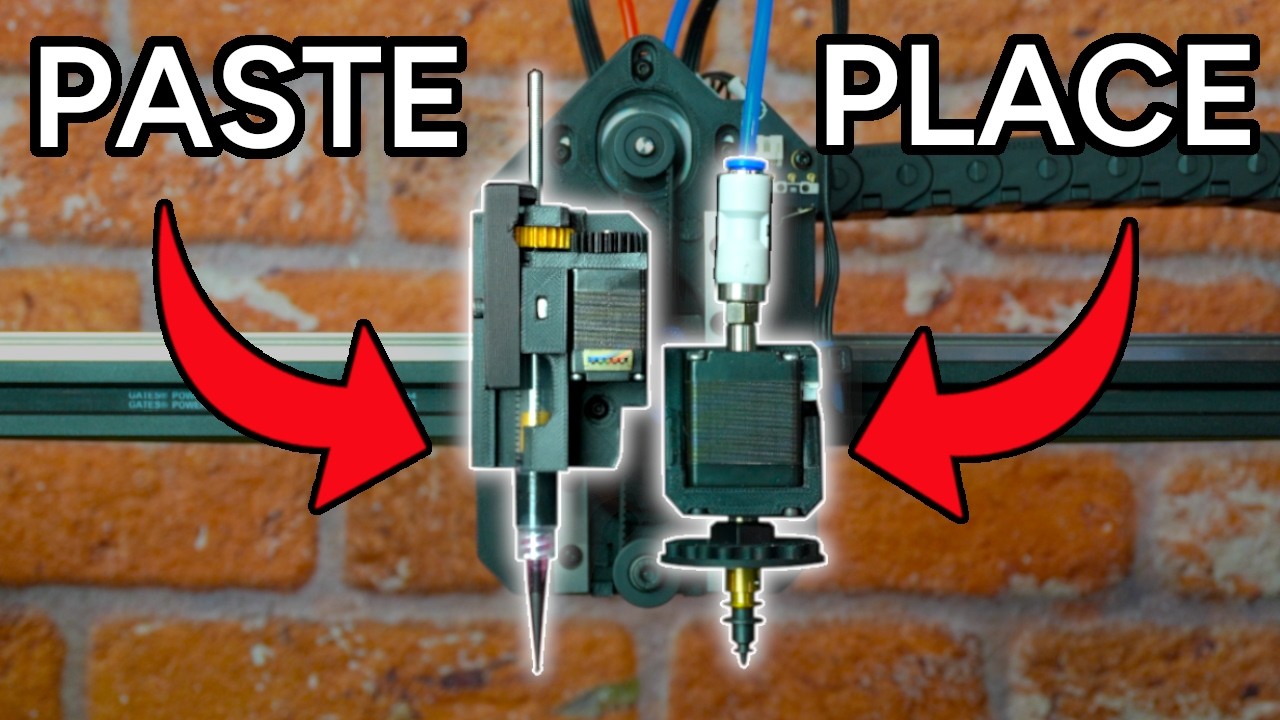
Показать описание
The LumenPnP can now do it all: deposit paste, then immediately place parts! Blank board goes in, working board comes out!
-------------------------------------------------------------------
-- FOLLOW --
-- GEAR --
These are affiliate links so if you buy anything through them I get a small percentage which helps out the channel. Thank you!
-------------------------------------------------------------------
-- FOLLOW --
-- GEAR --
These are affiliate links so if you buy anything through them I get a small percentage which helps out the channel. Thank you!
one machine for PCB assembly
You can now PRINT PCBs! Creating a homemade PCB with the Voltera V-One PCB Printer!
One-Stop PCB & SMT Assembly |Reliable Manufacturing #oem #pcbmanufacturer #smtfactory #pcba #sm...
Automated PCB Assembly Using Pick & Place Machine
Bittele Electronics - One-stop PCB Assembly House
The Best One for AOI Inspection for PCB Assembly #pcbmay #pcbengineering #electronicsmanufacturing
#pcbassembly#technology#ic#arduno#circutboard#innovation
How to Upgrade Your Manual Odd-Form PCB Assembly to Machine Automation
PCB Manufacture and PCB Assembly inside PCB Factory China - PCBWay
Best way to solder a wire on PCB #diy #soldering
Full Yamaha SMT line up 2025 | Yamaha YR series | PCB assembly of the future
Advanced PCB Assembly Choosing the Right Pick and Place Machine
PCB assembly In Circuit Test ICT
PCB Manufacturing and Assembly Process in Factory | How Printed Circuit Boards are Made | Production
One stop solution For PCBs, PCBAs
one-stop solution: pcb manufacturing and pcb assembly
High-speed placement machine-PCB Assembly Factory Tour
How SMT PCB Unloader working for Smart EMS factory PCB assembly
One-stop pcb printing, component procurement, pcba assembly #chips #pcba #smartdoorlock
Surface Mount pcb Assembly | PCBA one-stop production, fast delivery, 100% quality products
How PCB is from design to production-1 minute let you know
one-stop pcb/pcba manufacturer👨🔧 #scspcba #scspcb #pcb #pcba
What is a PCB?
PCB Assembly One Stop Solution HENGKAITUO Company Profile
Комментарии