filmov
tv
HACKED!: Microwave Transformer becomes a High Current Transformer
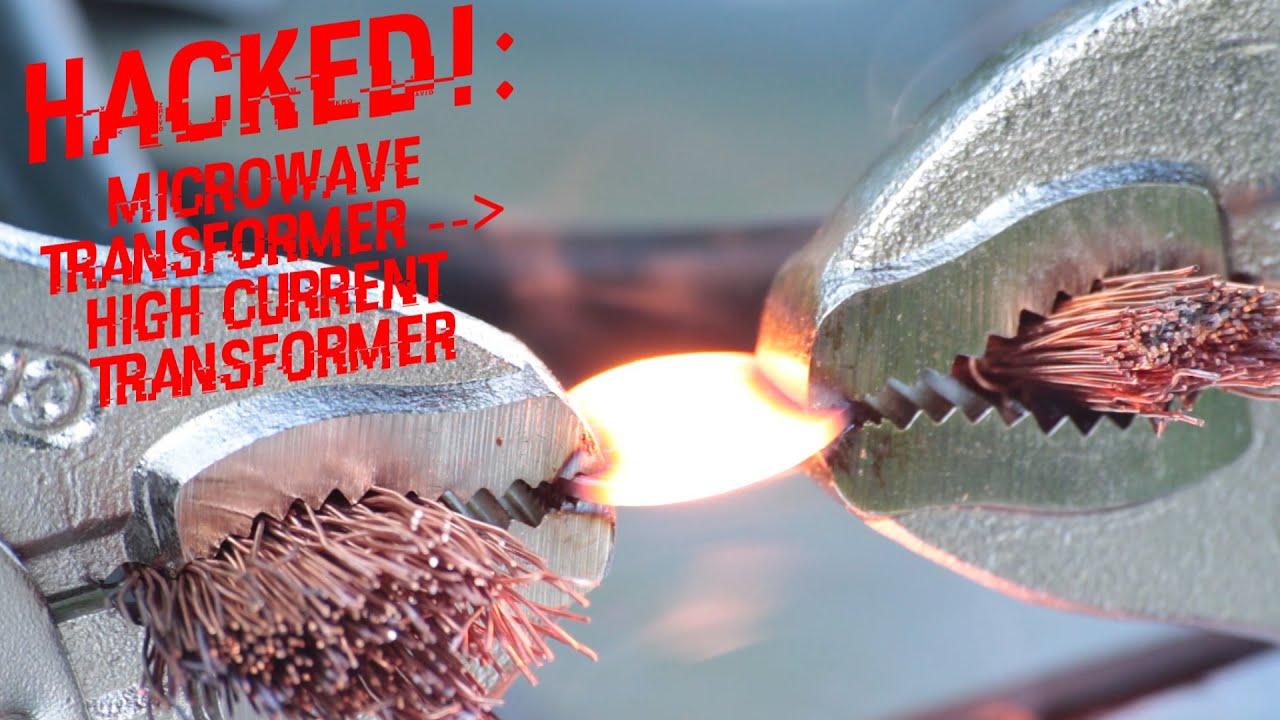
Показать описание
WARNING: This project uses mains voltage. Do not replicate it!
In this episode of HACKED! I want to create a weld for my electric longboard. But I do not have a welding machine. That is why I will repurpose an old transformer from a microwave into a high current transformer that should be capable of doing the job.
Music:
2011 Lookalike by Bartlebeats
In this episode of HACKED! I want to create a weld for my electric longboard. But I do not have a welding machine. That is why I will repurpose an old transformer from a microwave into a high current transformer that should be capable of doing the job.
Music:
2011 Lookalike by Bartlebeats
HACKED!: Microwave Transformer becomes a High Current Transformer
HACKED : Microwave Transformer Become A High Current Transformer...Home Made Spot Weldding Machine..
Hacked microwave transformer vs 4 mm nail
The most deadly project on the Internet
2263 - 10 Things To Do With A Microwave Oven Transformer
Microwave Oven Transformer/MOT Under Oil - 2.5KV Input - High Voltage Arc
HACKED! :Normal Transformer Become a High Current Transformer
Microwave Oven Transformer 😄
This Is Why We Don’t Toss Out Broken Microwaves | Remake Projects
Rewound Microwave Oven Transformer (MOT) for high current. (Re-upload from old channel)
Microwave oven Transformer welder
Microwave Oven Transformers Using Them For Projects
High Voltage Microwave Transformer Arcing to Water (2000V)
Plasma From a MicroWave Transformer
microwave transformer becomes a high current।।diy spot welder microwave transformer||high temperatur...
Microwave Oven Transformer (MOT) Sparks and Sparklers! | Extreme High Voltage
Debunking DEADLIEST craft hack, 34 dead | H2CT Ann Reardon
Weekend fun with a transformer from a microwave
Microwave Transformer Burnout in 1080p
Is a microwave oven transformer welder any good? (plus a softstart circuit)
Homemade electromagnet from a microwave transformer
Jacob's ladder using microwave transformer High voltage Danger
Fun with Microwave transformers part 1
Old Microwave Oven Transformer
Комментарии