filmov
tv
Full Shop Air Compressor Setup
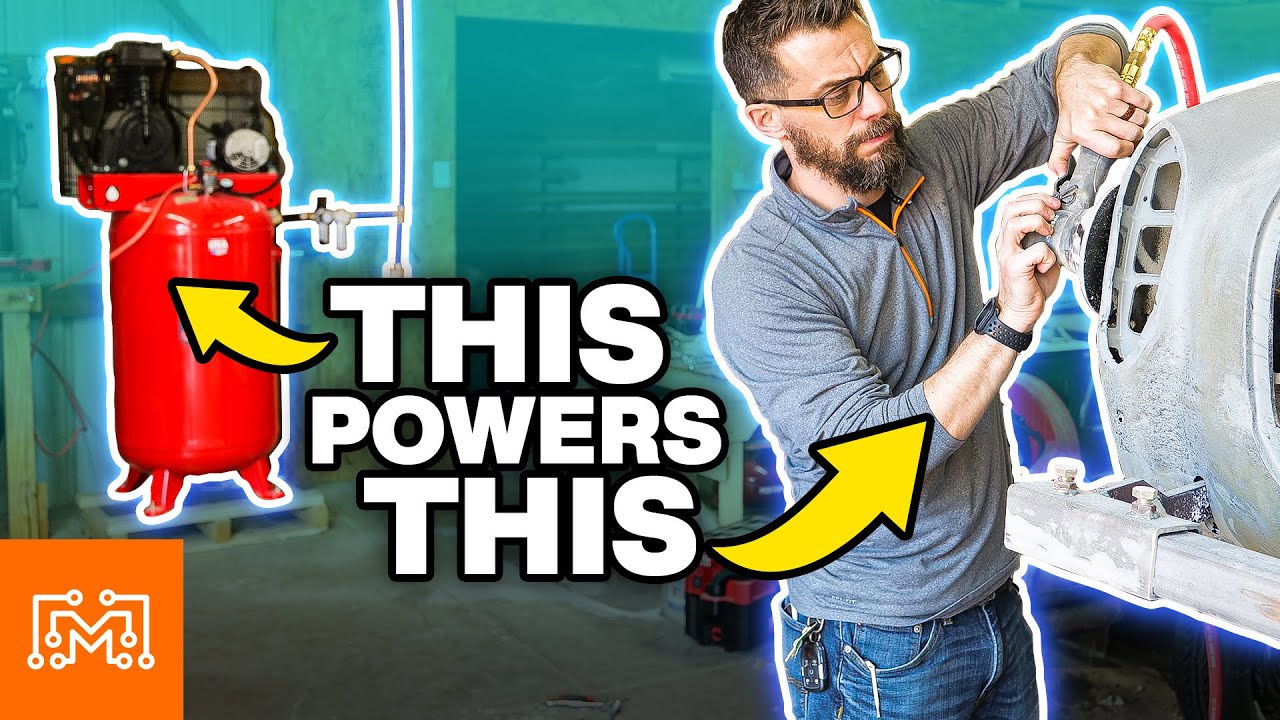
Показать описание
Get digital plans, cool merch, and indepth articles at
Learn 3d modeling in Fusion 360 with our online course:
TOOLS & SUPPLIES WE USED(affiliate links):
Want to support ILTMS? The Maker Alliance gets exclusive content and more...
FOLLOW:
#aircompressor #ILikeToMakeStuff #DIY
About I Like To Make Stuff:
We have lots of projects including woodworking, metalworking, electronics, 3D printing, prop making and more!
These videos are our attempt inspire and empower others to make the stuff that they want to have. Hopefully you'll see something here that will inspire you to make something that you're passionate about!
Full Shop Air Compressor Setup
I Like To Make Stuff
Full Shop Air Compressor Setup
Air Compressor Piping Line Hack #aircompressor pressor #airtools #Shoptour
How to Install Air Compressor Lines & Drops to Use Air Tools in Your Home Garage or Shop
Full RapidAir Maxline & 60 Gal Compressor Setup For The Shop!
Industrial Air Compressed Air Piping System
DIY Home Garage Compressor System for Autobody and Paint!
You Need This Shop Piping System // MaxLine 1/2' Compressed Air Tubing Installation
Garage/Shop Air Compressor setup + Tips
Air Compressor Line Kit 3/4'' x 200FT HDPE/Aluminum Shop Air Piping System Review
60-Gallon Air Compressor Setup and Shop Air Installation Industrial Air (Setup Part One)
✅ Building a Better Air Compressor for My Garage for DIRT CHEAP !
How to install a compressed air system in your garage or workshop
What Size Air Compressor Do You Really Need? (Updated 2023)
Ultimate Shop Air Setup
Dual Air Compressor Set up for Small Shop
Complete Overview of my Garage/Shop Air System
HOW TO Set Up your SHOP or HOBBY AIR COMPRESSOR for AIRBRUSH a Beginners Guide!
Air Compressor Setup: Stage 1 (Sanborn Pneumatic Shop Air) | AnthonyJ350
A Real Man's Air Compressor Setup and Running
Quincy Air Compressor setup with cooling
Our Budget Air Compressor Set-Up #shorts
GARAGE CUSTOM DETAIL AIR COMPRESSOR INSTALLATION. COXREELS EZCOIL
Barbershop Air Compressor Set Up | FadeFathers Barbershop
My Custom Shop Air Compressor Setup & Noise Level Comparison
Комментарии