filmov
tv
Should You Buy A Bridgeport Mill To Start Your Shop?
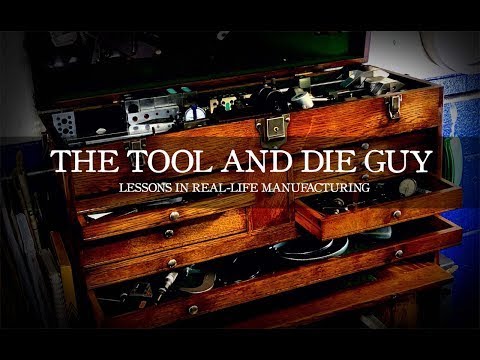
Показать описание
This video is a response to an email that I received this week:" I want to start my own shop, is buying a Bridgeport milling machine still a good option?" Here are my two cents.
Should You Buy A Bridgeport Mill To Start Your Shop?
Why you should buy a Bridgeport Milling Machine instead of a Drill Press
Bridgeport Milling Machine Buyer' s Guide
How to buy a mill machine
How to use a Bridgeport and its features!
How to Buy a BRIDGEPORT SERIES II MILL
#31 What's Better Than a Bridgeport?
The Differences Between Bridgeported & Street Ported Rotary Engines
Family Life Week | Pastor Samuel Blair | Calvary SDA Media | October 20, 2024
New to me Bridgeport finally found one worth buying
Bridgeport CT is a Great City with So Much to Offer. Find Out Why People are Moving to Bridgeport
Buying a Bridgeport, TIG Welder & More at Auction!
Why the Bridgeport is So Good for Bicycle Framebuilders
How to use a Bridgeport Milling Machine
It's Bridgeport Time!
Best Things To Do in Bridgeport Connecticut
Tips For First Time Rotary Owners
Bridgeport Mill, new to the shop!
Boring a Cylinder on the Bridgeport Series 1
Buying and Moving a Bridgeport Alliant RT2 Mill
Vertical (Bridgeport) Milling Machine Head | Every Knob and Lever Explained
How it started vs how its going... Bridgeport cleanup continues...
Bridgeport J head Features and Functions
What do you know about THAT? #bridgeport #industrialrevolution #schoolsystem #employees
Комментарии