filmov
tv
Steel Manufacturing Process: Coal & Coke
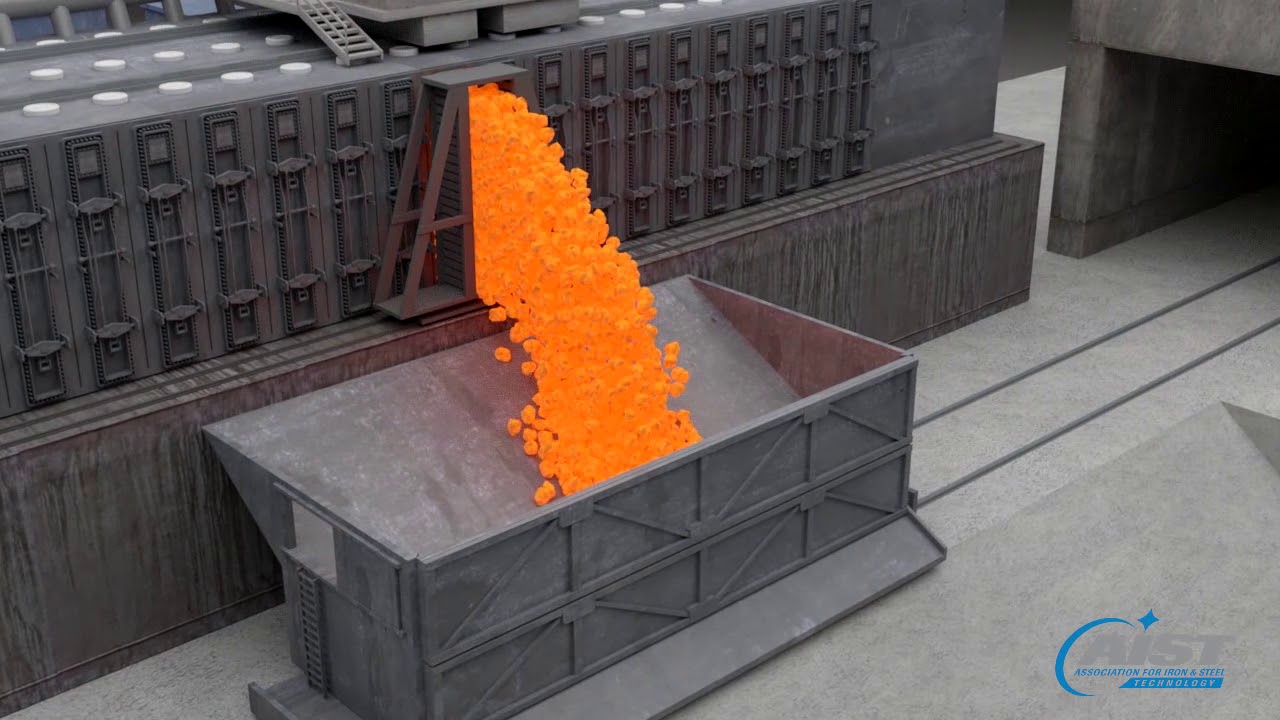
Показать описание
Coal is a mineral consisting mainly of sedimentary fossilized carbon with smaller amounts of other elements, such as sulfur, hydrogen, oxygen, nitrogen and more. Coal is found under the earth crust as lignite, or brown coal — the lowest ranking coal, bituminous coals and anthracite. It is extracted either from underground by shaft mining or at ground level by open-pit mining.
Coal is the largest source of energy for the generation of electricity worldwide and is also used in the production of metallurgical coke as blast furnace fuel. Some smaller blast furnaces can utilize charcoal as a carbon source, but the larger blast furnaces require the strength and durability of coke.
Coke is produced by igniting bituminous coal under reduced oxygen conditions in oven batteries specially designed for this process. The coking process generates the following main volatiles as byproducts: coke oven gas, tar, ammonium sulfate, benzol, toluol and naphtha.
A coke battery is made up of multiple ovens. Coal is crushed and blended prior to being charged in a coke oven. A larry car charges the individual oven with the blended coal. In the coke oven, the coal is heated to 1,800°F for up to 18 hours. During that time, the volatiles of the coal are driven into the offgas and a pure carbon form called “coke” remains. The coke, when exposed to oxygen, will immediately ignite and begin to burn. When the coke is pushed from the oven into a railcar, it is quickly quenched to cool the coke and stop the burning process. The cooled coke is then dumped onto a coal wharf where it is taken to a facility to be screened and sized prior to being charged into the blast furnace.
From the Association for Iron & Steel Technology’s (AIST) Interactive Steel Manufacturing Process
The Making, Shaping & Treating of Steel Wheel
Produced in collaboration with Purdue University Northwest’s Center for Innovation through Visualization and Simulation and the Colorado School of Mines’ Advanced Steel Processing and Products Research Center
AIST.org
Copyright AIST, All Rights Reserved
Coal is the largest source of energy for the generation of electricity worldwide and is also used in the production of metallurgical coke as blast furnace fuel. Some smaller blast furnaces can utilize charcoal as a carbon source, but the larger blast furnaces require the strength and durability of coke.
Coke is produced by igniting bituminous coal under reduced oxygen conditions in oven batteries specially designed for this process. The coking process generates the following main volatiles as byproducts: coke oven gas, tar, ammonium sulfate, benzol, toluol and naphtha.
A coke battery is made up of multiple ovens. Coal is crushed and blended prior to being charged in a coke oven. A larry car charges the individual oven with the blended coal. In the coke oven, the coal is heated to 1,800°F for up to 18 hours. During that time, the volatiles of the coal are driven into the offgas and a pure carbon form called “coke” remains. The coke, when exposed to oxygen, will immediately ignite and begin to burn. When the coke is pushed from the oven into a railcar, it is quickly quenched to cool the coke and stop the burning process. The cooled coke is then dumped onto a coal wharf where it is taken to a facility to be screened and sized prior to being charged into the blast furnace.
From the Association for Iron & Steel Technology’s (AIST) Interactive Steel Manufacturing Process
The Making, Shaping & Treating of Steel Wheel
Produced in collaboration with Purdue University Northwest’s Center for Innovation through Visualization and Simulation and the Colorado School of Mines’ Advanced Steel Processing and Products Research Center
AIST.org
Copyright AIST, All Rights Reserved
Комментарии