filmov
tv
Cutting aluminum and acrylic with the table saw
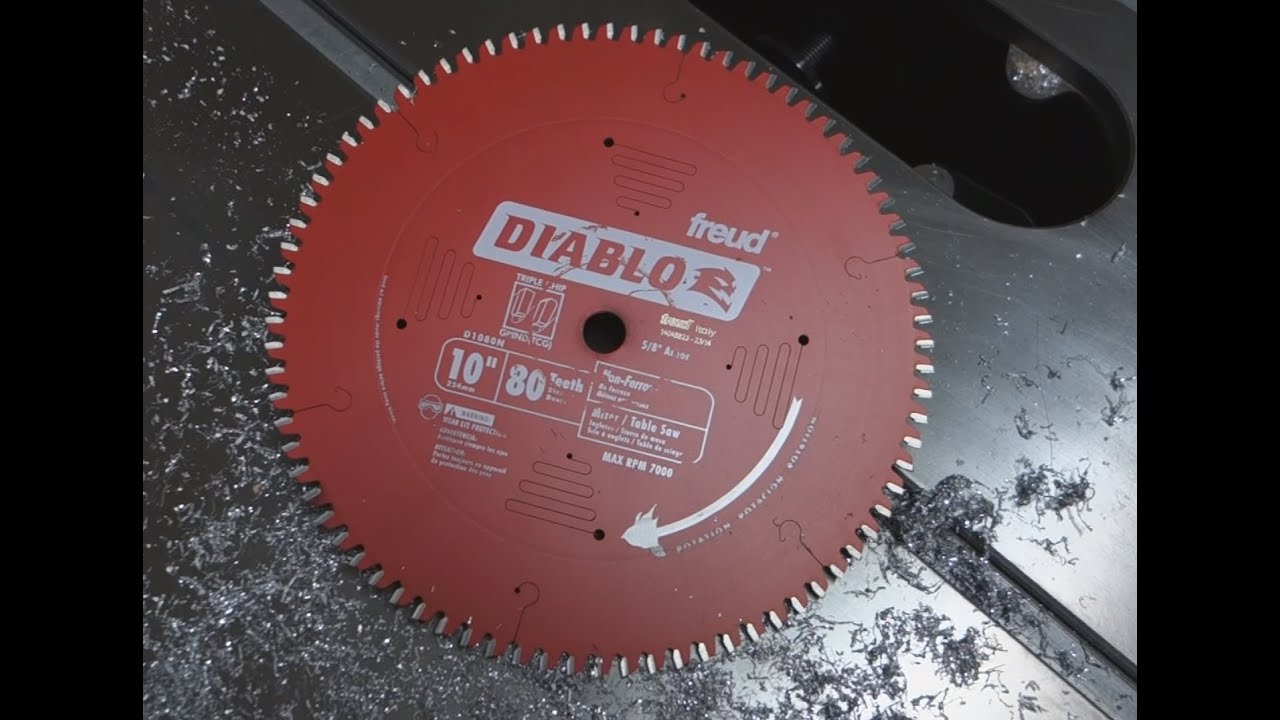
Показать описание
This is the 80 tooth non ferrous TCG Diablo blade from Freud. All cuts were made with out lubricant and the majority of the cuts were made on solid 1-1/4" x5" 6061 Aluminum.. I also used the same blade to cut parts for the wooden sled and plastic guard with great results.
I have used regular wood ATB blades to cut aluminum and while it will work... this blade does make a significant difference in cut quality and ease of cutting. It did not provide a 'fly cutter' like finish on the cuts but it did cut true and smooth, polishing most of the cut on many passes. Blade deflection will be minimal on thicker solid parts.
Although the video only shows a few cuts, I made many more passes on the aluminum materials testing different configurations with full pass and blind cuts. At the end of the testing the blade still looks new with no signs of usage on the carbide.
I am impressed and it beats using the band saw to perform straight line cuts. Makes me want to try out their ferrous blade...
I have used regular wood ATB blades to cut aluminum and while it will work... this blade does make a significant difference in cut quality and ease of cutting. It did not provide a 'fly cutter' like finish on the cuts but it did cut true and smooth, polishing most of the cut on many passes. Blade deflection will be minimal on thicker solid parts.
Although the video only shows a few cuts, I made many more passes on the aluminum materials testing different configurations with full pass and blind cuts. At the end of the testing the blade still looks new with no signs of usage on the carbide.
I am impressed and it beats using the band saw to perform straight line cuts. Makes me want to try out their ferrous blade...
Комментарии