filmov
tv
Compressed Air Piston Engine V3 (3D Printed)
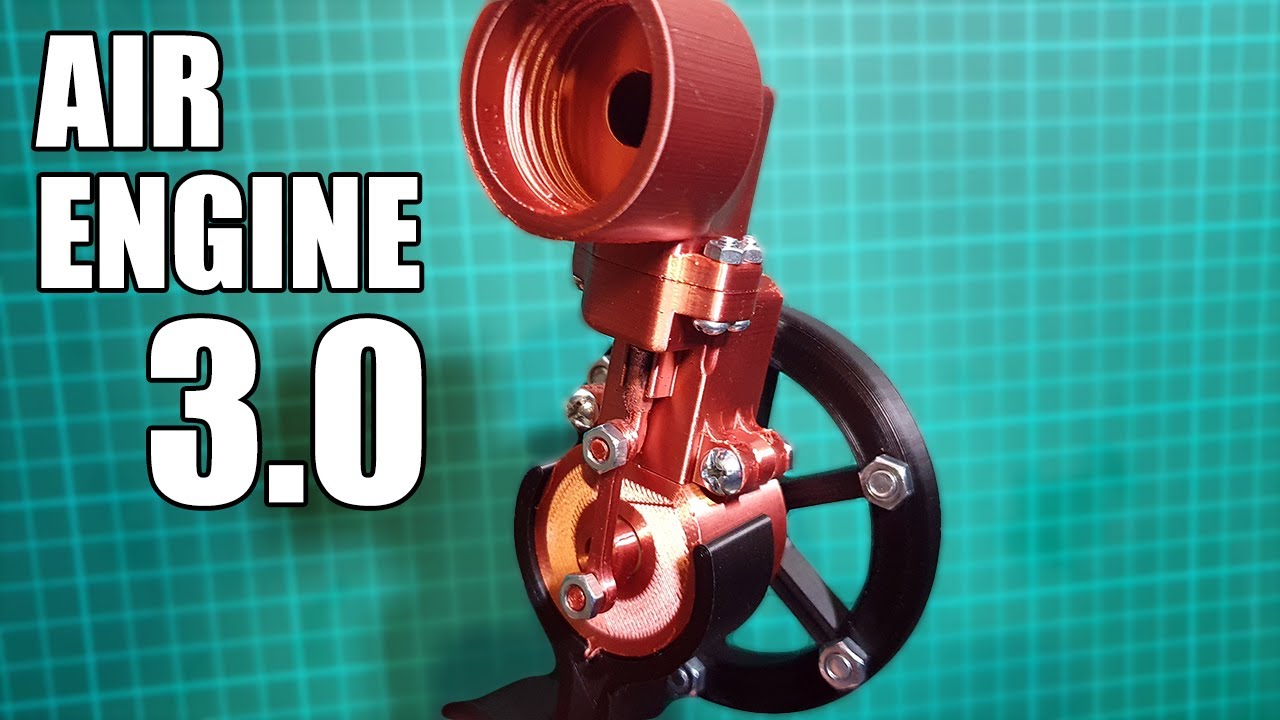
Показать описание
This is my 3rd attempt at making a compressed air engine. This time I've implemented a sort-of exhaust valve, improved the strength of the engine and increased the running duration!
There's still more I need to do to improve this engine, I still don't think that it is strong enough, so I may use PETG for some of the parts next time to see if this helps.
Also it would probably be good to see the engine actually power something....so let me know any ideas you have in the comments below!
There's still more I need to do to improve this engine, I still don't think that it is strong enough, so I may use PETG for some of the parts next time to see if this helps.
Also it would probably be good to see the engine actually power something....so let me know any ideas you have in the comments below!
Compressed Air Engine V3
Strange Compressed Air Engine (Assembly and Test) #steamengine #3dprinting
Compressed Air Piston Engine V3 (3D Printed)
Optimising an Air Engine
I Built a Nutating Disk Air Engine
Diaphragm Air Engine
Simple Compressed Air Engine #shorts
4,500RPM Air Engine
EP 3- Four Stroke Engine in Action! 🔥 What Really Happens Inside Your Bike
3D Printed Single Cylinder Compressed Air Engine
The most efficient air motor in the world by Engineair Pty Ltd Australia
Running Lego Engines with Air
Compressed Air Engine with an Old Hard Drive
3 Cylinder Radial Compressed Air Engine
3 Cylinder Opposed Piston Compressed Air Engine
ALL-NEW Compressed Air Engine To Disrupt The Car Market
Air powered engine. 3 cylinder.
Water Air Engine
Compressed Air Triangular Engine - Wankel Rotary (3D Printed)
Air Engine Compressed air engine
5 HP Air Compressor & 5 HP Motor 3 Phase | 700 Pound Air Tank | Industrial Air Compressor
Fiac 500 Ltr Air Compressor 7.5 HP Motor Made in Italy
3D Printed V2 Pressure Engine
3d Printed Compressed Air Inline 3 Engine
Комментарии