filmov
tv
Foundry worker puts wet scrap metal in furnace
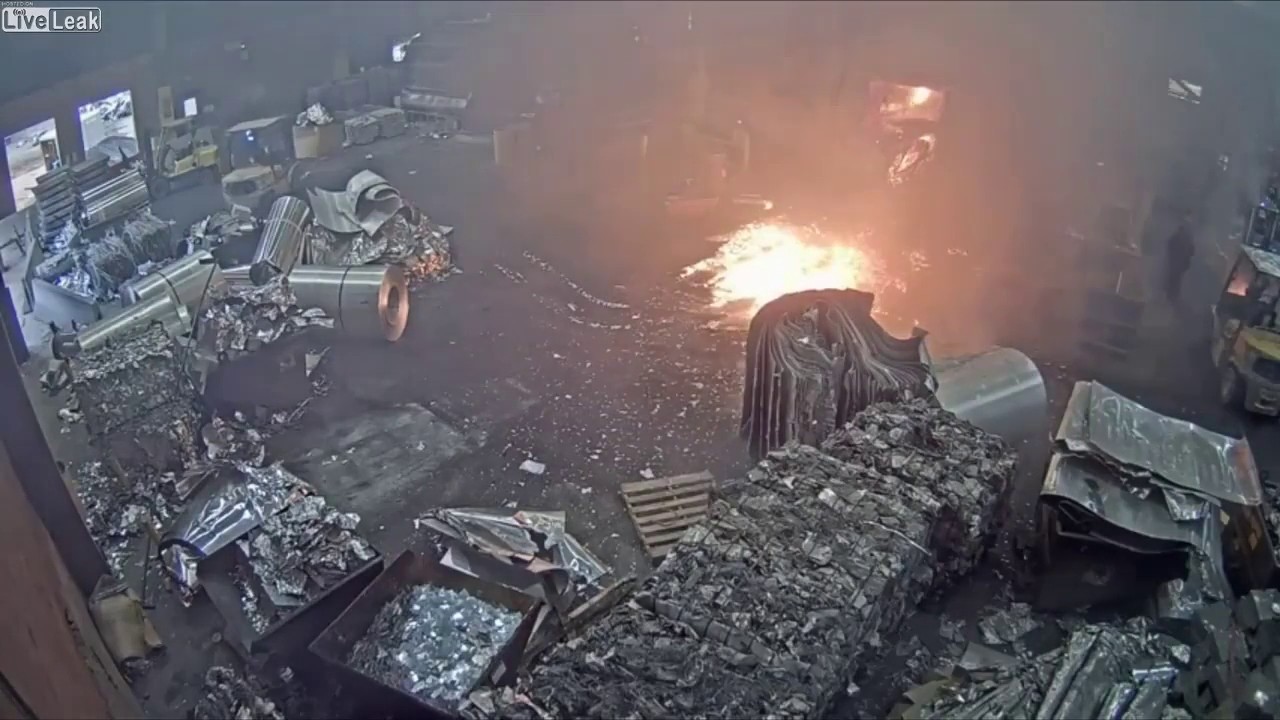
Показать описание
Foundry worker puts wet scrap metal in furnace
A portal to hell at an aluminum plant that swallowed up the entire shop in a matter of seconds.
Foundry worker puts wet scrap metal in furnace, November 27, 2019
How To Foundry Worker Puts wet Scrap Metal / Scrap Baling Press Double Action #scrap@scrap
Foundry worker almost burned alive after loading wet scrap metal into furnace
TOP 10 Accidents In Metal Industry ✅
😲 WATCH THIS BLAST FURNACE ACCIDENT AT A STEEL PLANT
OMG! Did not expect this! Wet Scrap Metal into a Furnace
Company fined £2m after death of recycling plant worker
😲 Accident, lathe machine accident 🔥🔥🔥
Lathe Machine Actual video accidents #shorts #short
Forklift Driver Walks Away Unharmed After Causing Massive Explosion With Wet Aluminum In Furnace 💥😲...
A Foundry accident A Cautionary Tale to new Foundry people
STEEL MILL ACCIDENT #wow #crazy #steel #trending #views #search
Russian Lathe Accident
Mistakenly Grabbing Molten Glass (For safety/hazard education, don’t try!) #shorts
steel2 foundry
Man Puts Hand In Molten Metal
Induction Furnace Run..
When Loggers Cut Down Old Tree – They Couldn't Believe What They Found Inside
Danger. Watch the iron derailment in an iron factory
Scrap melting induction furnace
Back Draft
amazing welding method of Pakistani welder #welding #shorts
Комментарии