filmov
tv
TFS: How to Bridge Gaps and Holes on Thin Aluminum
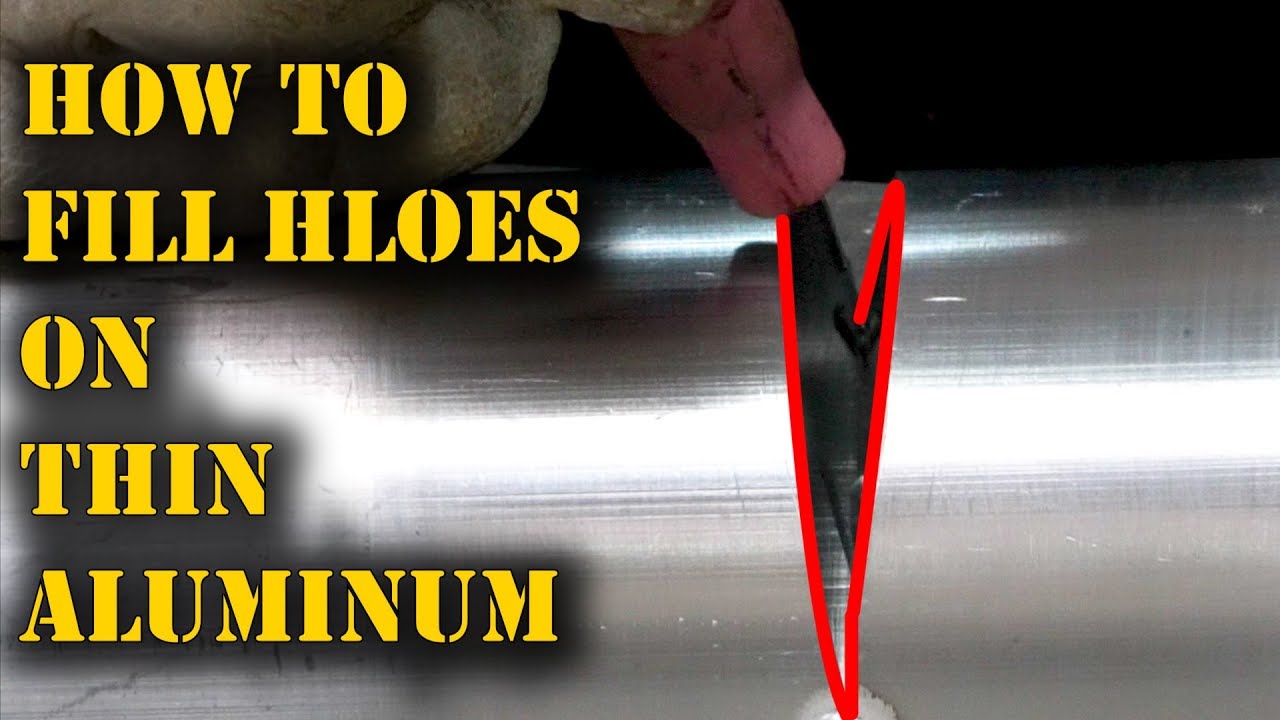
Показать описание
By very popular request, we created a video dedicated to bridging gaps on thin aluminum based on the episode all about filling gaps on thin metal (steel). While this gap may be a bit extreme as shown, the techniques demonstrated to control it still hold true.
Special thanks to Blue Demon Welding for sending out a ton of filler rod used in this episode. Check out the link below to pick up some cool Blue Demon products we regularly use!
Tools & Gear We Use and Recommend
Learn to TIG Weld in Our Class!
Bridge Gaps in Steel Episode:
Subscribe to The Fabrication Series for MORE!
Special thanks to Blue Demon Welding for sending out a ton of filler rod used in this episode. Check out the link below to pick up some cool Blue Demon products we regularly use!
Tools & Gear We Use and Recommend
Learn to TIG Weld in Our Class!
Bridge Gaps in Steel Episode:
Subscribe to The Fabrication Series for MORE!
TFS: How to Bridge Gaps and Holes on Thin Aluminum
TFS: How to Bridge Gaps and Holes on Thin Metal
Welding tip, how to bridge a gap
How To TIG Weld ANY Gap
Fitting plane thorough bridge gaps
How Fear of Holes was invented
Flying through the smallest bridge gap in TFS!!!
Tig Welding an Impossible Huge Gap | Bad Fit-Ups
HOW TO FILL GAPS, MIG WELDING
TIG Welding A Gap In Thin Steel
My finger hurts so much, oh my god 😭 #youtubeshorts #makeup #sfx #sfx_makeup #foryou #art #shorts
TFS: TIG Simple - 4 Ways to Feed Filler Rod
TFS: Understanding AC Balance #TIGSimple
TFS: Does Tungsten Stick Out Really Matter?
TFS: Welding Very Thin Aluminum (GTR Trunk Shave)
How-To Fill Holes and Big Gaps With Your MIG Welder
how to weld gap iron
TFS: 5 Aluminum Welding Drills
TikTok Similar to 9/11 Attacks
TFS: Stainless Crack Repair
TFS: First TIG. Now What?
TFS: Stacks and Dabs
TFS: How to Weld Thick Metal to Thin Metal
TFS: TIG Setup Simplified with LOTS of Detail
Комментарии