filmov
tv
New method of manufacturing using powder bed: Additive Manufacturing with Selective Laser Melting
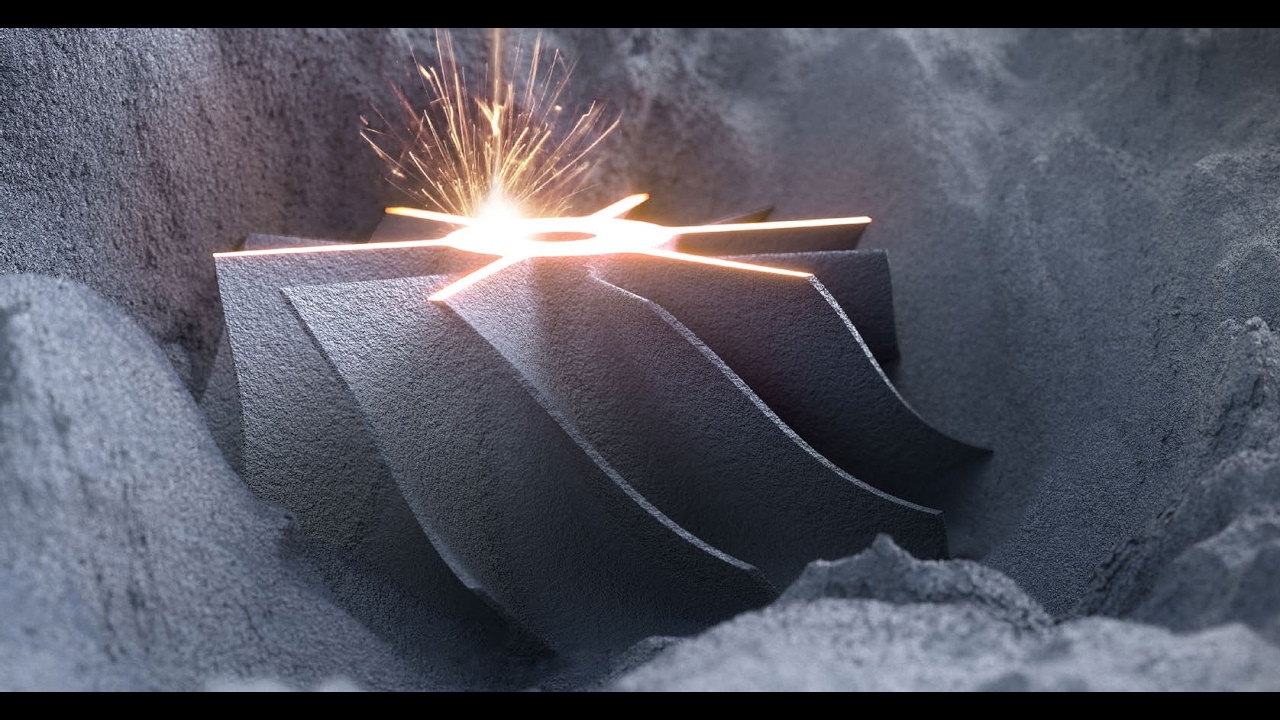
Показать описание
DMG MORI underlines its position as a market leader, being the first company to offer a full range of Additive Manufacturing machines by adding the new LASERTEC 30 SLM powder bed machine, to join the existing hybrid deposition welding machines.
New method of manufacturing using powder bed: Additive Manufacturing with Selective Laser Melting
Aerospace Nozzle ADDITIVE Manufacturing
Additive Manufacturing Process of an Aerospace Part
How Things Are Made | An Animated Introduction to Manufacturing Processes
Amazing factories | Manufacturing method and top 4 processes | Mass production process
Manufacturing buckle spring bending process- Good tools and machinery make work easy
Giant Composite Aerospace Part Manufacturing
Most Satisfying Industrial Manufacturing Processes with Modern Machinery.
Amazing Crankshaft Manufacturing in Pakistan Local Industry | Decades old method #talent #amazing
Large Scale Additive Manufacturing
PCB manufacturing and glueing | Electronics circuit | #electronic #shorts
How are Microchips Made? 🖥️🛠️ CPU Manufacturing Process Steps
The Manufacturing Process of Lab Grown Diamonds
NEW METHOD OF UNLOADING METAL COIL FROM THE LORRY
Integrated housing for easy construction process- Good tools and machinery make work easy
EPS panel house construction | INDIA | EPS Technology
A Different Farming Method Of Sugarcane Planting Deeper And Placing Sideways #satisfying #short
2023 New Handheld Laser Welding Machine
Manufacturing Nails | Iron Nails #nails #makingnails #making #wirenailmakingmachine #wireless #wire
Young Ginger Farming Techniques #satisfying #short
What A Great Idea Pepper Farming #satisfying #shot
Interesting Tools #satisfying #shortsvideo
Smart Farming #satisfying #shortsvideo
China's Top 5 Manufacturing and Mass Production Videos | by @miracleprocess
Комментарии