filmov
tv
Measuring the output of strain gauges
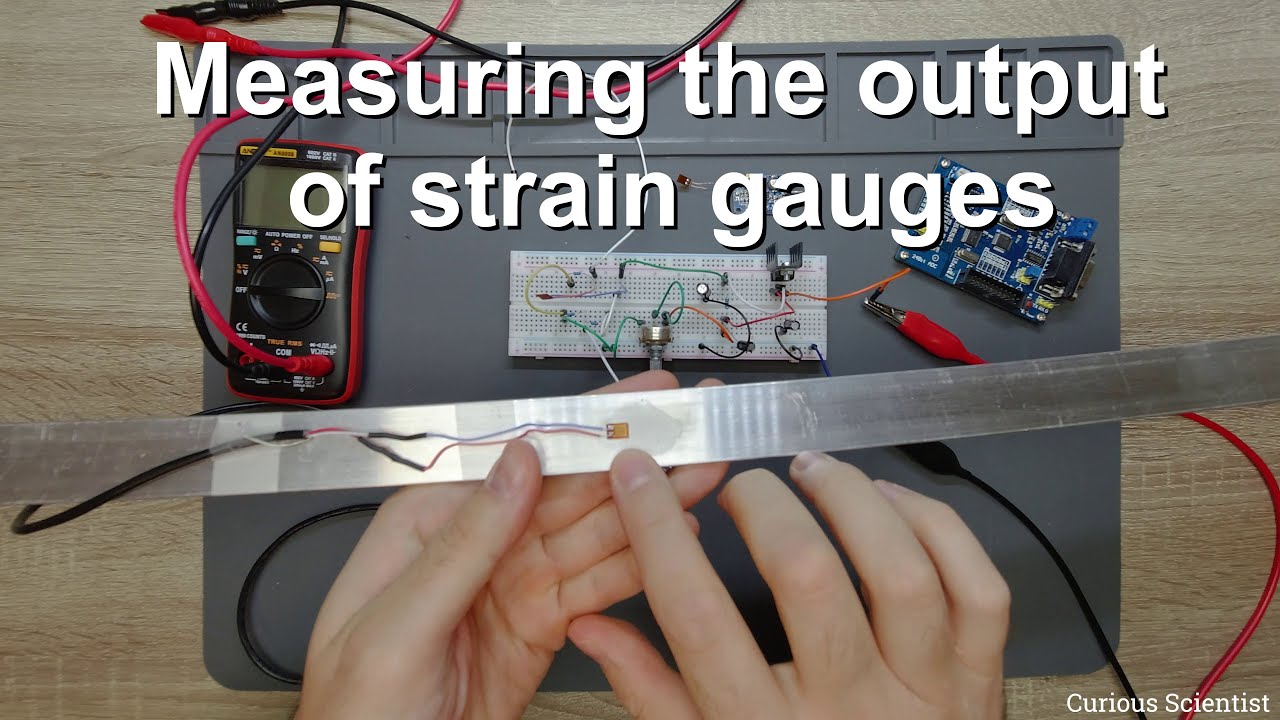
Показать описание
In this video I show you what are the challenges of measuring the tiny changes in the resistance of a strain gauge. The resistance of an unloaded strain gauge is around 350 Ohm (at least the one I use in this video) and a loaded one's is 1-2 Ohms smaller or larger. This is a small change, it is difficult to measure it and it is even more difficult when it is a change in the resistance of something. To make this value into a more comprehensive one, I use a Wheatstone bridge to convert the change in the resistance into a change in voltage. The obtained voltage change is still tiny (few tens of microvolts), therefore I use the built-in PGA (Programmable Gain Amplifier) of an ADS1256 AD converter to resolve this tiny change.
Please don't forget to subscribe!
If you want to support my work, please consider buying the parts using my affiliate links:
Please don't forget to subscribe!
If you want to support my work, please consider buying the parts using my affiliate links:
Measuring the output of strain gauges
Measuring the Output of Strain Gauge Sensors.
Strain Measurement
Strain Gauge 101 - Learn the basics of how they're used
Measuring Output from a Strain Gauge
The Ingenious Design of Strain Gauges
Electronic Basics #33: Strain Gauge/Load Cell and how to use them to measure weight
How STRAIN GAUGE Works | Precision SCALE With Arduino
Strain gauges first measuring test
[Short Answers #1] Output voltage of a strain gauge amplifier module
Strain gage for measuring Thermal Expansion Coefficient
Introduction to Strain Gauges
What will happen if you forcefully bend a PCB strain gauge? #pcb #engineering #electronics #test
Strain Measurement using Strain Gauges
Strain Gage Mass Measurement
Strain Gages Introduction【KYOWA】
Improving Strain Measurement Quality with Signal Conditioning
Numerical 1- Calculation of Bridge Output - Strain Measurement - Transducer -2
Torque Measurement | Wheatstone Bridge Circuit for resistance strain gauge | Lecture 05.10
Learn how to scale a Strain Meter to read Microstrain
EME 3214: Strain gauge basics
Vinytics strain gauge - Sensor output measurement before signal conditioning by Amit verma
Strain gauge & Load cells
P#6 Measuring the output of strain gauges
Комментарии