filmov
tv
Saw blade manufacturers won't want you to see this tool #sawblades #tools
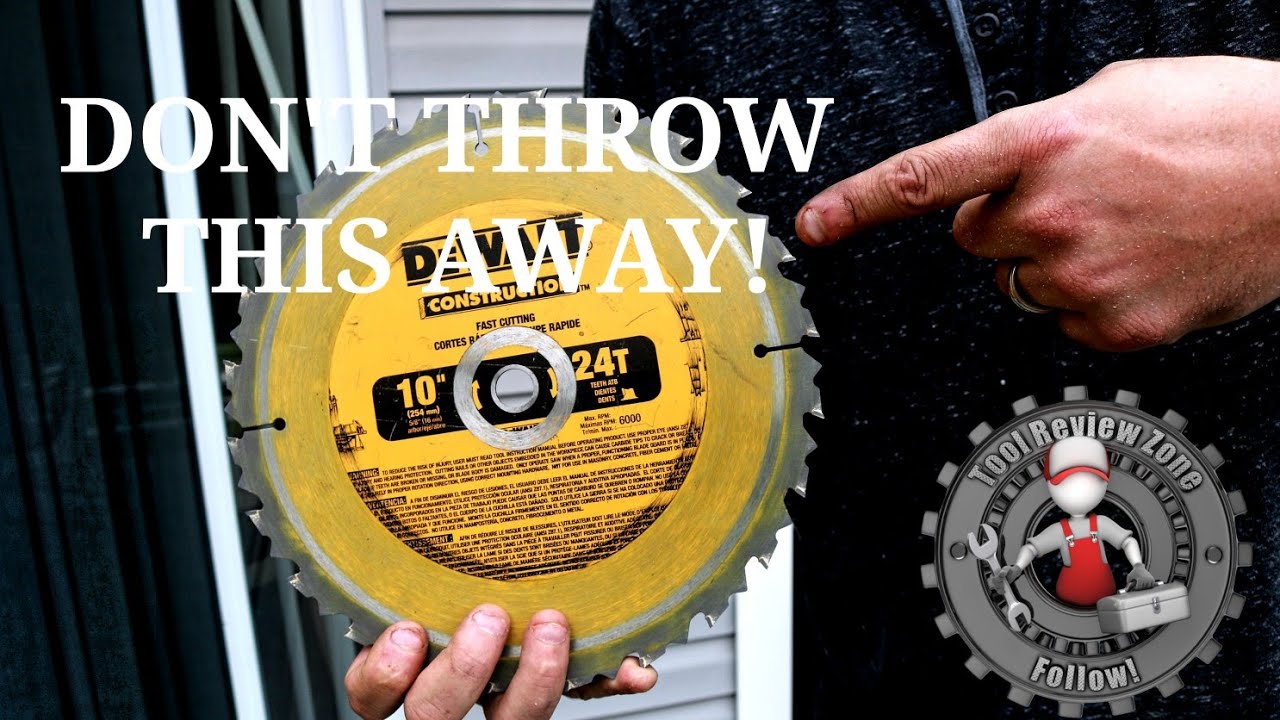
Показать описание
Chicago Electric Power Tools Professional Series- Item#96687
This portable circular saw blade sharpener makes it possible to sharpen several blades at a time. Constructed with a die cast aluminum base and indexing arm, this saw blade sharpener is durable but lightweight. Features include a motor block that tilts 25 degrees left and right to adjust for different blade tooth configurations.
Specialized blade receiver accepts blades with arbors up to 1 in.
Motor block tilts 25° left and right to handle different blade tooth configurations
Blade indexing arm for fast and easy performance
Sturdy die cast aluminum base and indexing arm
Portable compact design
Specifications
Name120 Volt Circular Saw Blade SharpenerSKU96687BrandChicago ElectricAmperage (amps)9CertificationUL listedDiameter3-1/2 in. - 15-3/4 in.Speed (max)3800Wattage (watts)140Product Height11Product Length9-1/2Product Width13-3/4Shipping Weight12.45 lbs.Accessories Included4 in. diamond wheel for carbide tips, 4 in. emery wheel for steel tips, harbor freight Chicago electric tools
This portable circular saw blade sharpener makes it possible to sharpen several blades at a time. Constructed with a die cast aluminum base and indexing arm, this saw blade sharpener is durable but lightweight. Features include a motor block that tilts 25 degrees left and right to adjust for different blade tooth configurations.
Specialized blade receiver accepts blades with arbors up to 1 in.
Motor block tilts 25° left and right to handle different blade tooth configurations
Blade indexing arm for fast and easy performance
Sturdy die cast aluminum base and indexing arm
Portable compact design
Specifications
Name120 Volt Circular Saw Blade SharpenerSKU96687BrandChicago ElectricAmperage (amps)9CertificationUL listedDiameter3-1/2 in. - 15-3/4 in.Speed (max)3800Wattage (watts)140Product Height11Product Length9-1/2Product Width13-3/4Shipping Weight12.45 lbs.Accessories Included4 in. diamond wheel for carbide tips, 4 in. emery wheel for steel tips, harbor freight Chicago electric tools
Комментарии