filmov
tv
TFS: TIG Simple - Does it Matter How You Sharpen Tungsten?
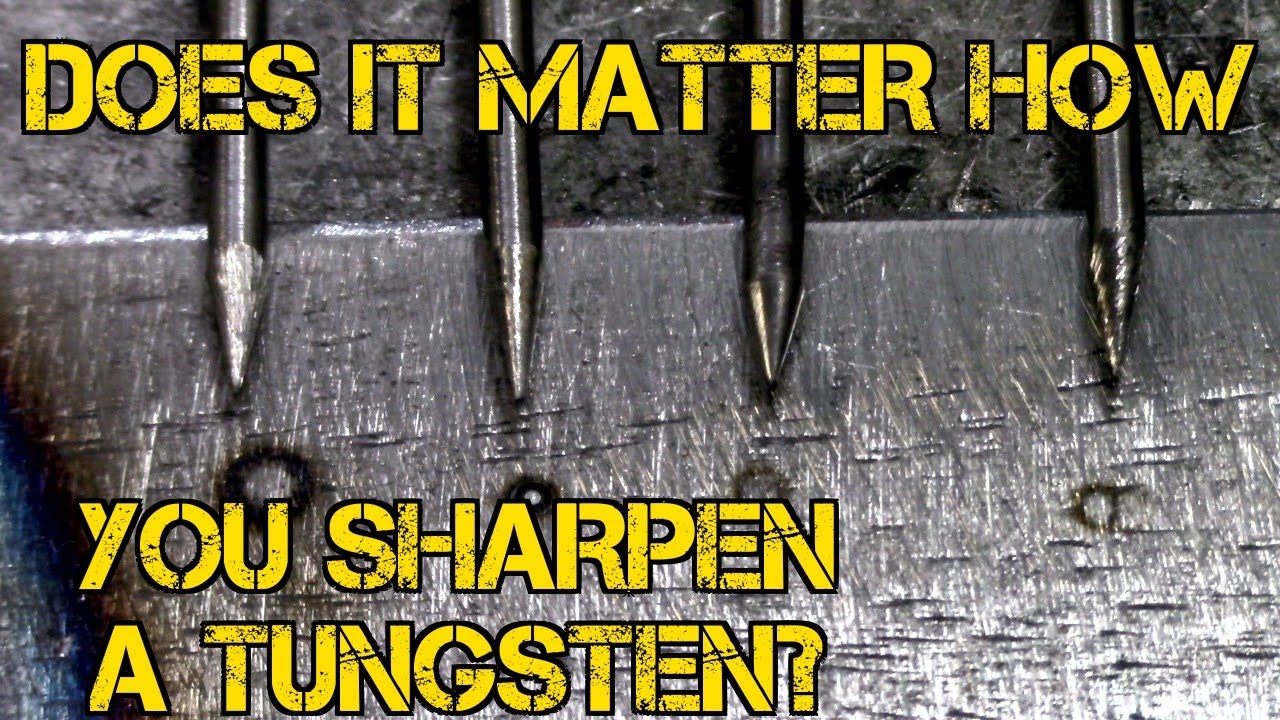
Показать описание
The ultimate question... "Does it matter how you sharpen tungsten?" Maybe... In today's TIG Simple episode, Justin the Fabricator investigates different ways to sharpen a tungsten and compares them to one another. Surprisingly, it needs more investigation.
Tell us what you think in the comments below!
Tools & Gear We Use and Recommend
Want to earn how to TIG? Take a class!
More TIG Simple vids coming soon!
Subscribe to my channel for MORE!
Tell us what you think in the comments below!
Tools & Gear We Use and Recommend
Want to earn how to TIG? Take a class!
More TIG Simple vids coming soon!
Subscribe to my channel for MORE!
TFS: TIG Simple - Does it Matter How You Sharpen Tungsten?
TFS: TIG Simple - Get A Grip - 8 Ways to Hold a TIG Torch
TFS: TIG Simple - 4 Ways to Feed Filler Rod
TFS: TIG Setup Simplified with LOTS of Detail
TFS: Top 10 Mistakes Beginner TIG Welders Make
TFS: First TIG. Now What?
TFS: The Secret to Perfect Stainless TIG Welds
TFS: 2T 4T TIG Welding Operation Modes #TIGSimple
TFS: All About TIG Torches
Your Very First TIG Welds with EXTREME Detail
TFS: Welds That Will Ruin Your Day
TFS: Understanding AC Balance #TIGSimple
TFS: Does Tungsten Stick Out Really Matter?
TFS: TIG Welding Class With Justin Kramer (highlights)
TFS: TIG Welding Class with Bob Moffatt (Highlights)
Which TIG Cup Works Best on Aluminum?
Beginner TIG welders NEED to know this...
TFS: 5 Aluminum Welding Drills
TFS: Why is the Filler Melting and Balling?
TIG Welding Basics Overview
TFS: Back Purging - How and Why
TFS: Battle of the Tungsten Colors
Busting Fake Internet Welds
the FIRST thing you should learn tig welding
Комментарии