filmov
tv
PLC Digital Output Types | Solid State vs Relay
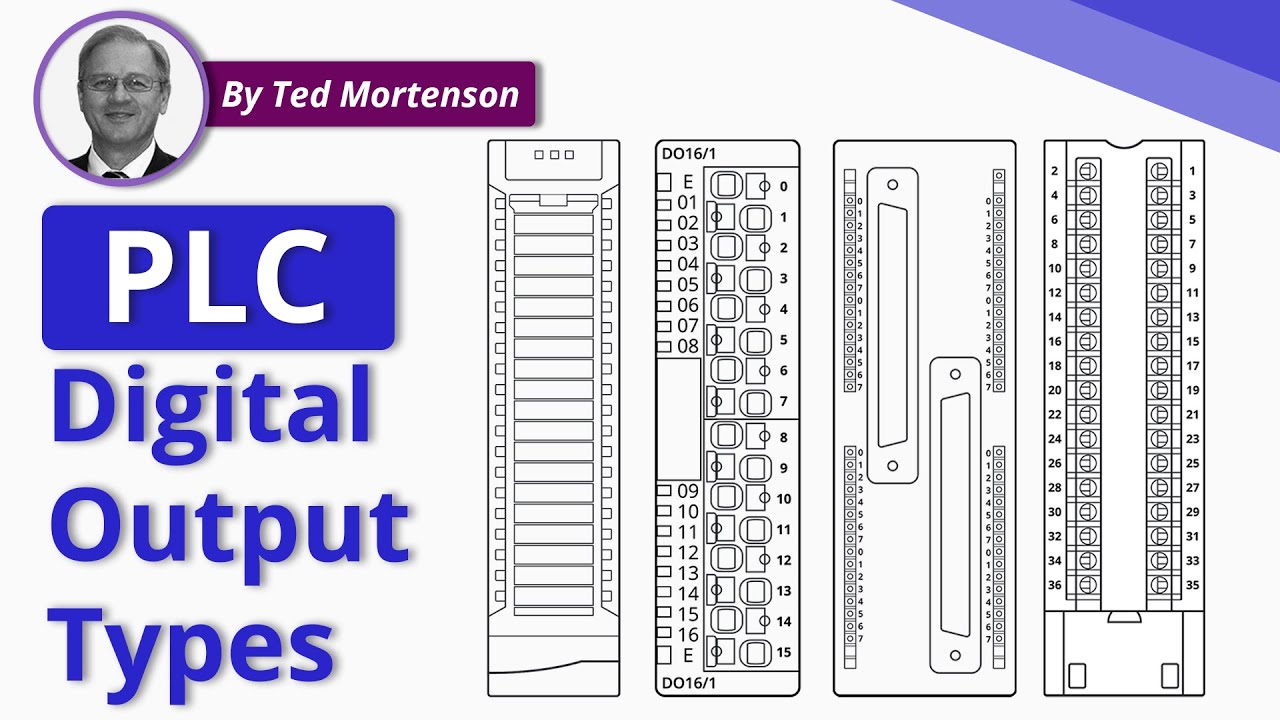
Показать описание
=============================
▶ Check out the full blog post over at
=============================
⌚Timestamps:
00:00 - Intro
00:52 - Digital vs Analog
01:44 - PLC digital output module types
01:50 - Relay output module
03:09 - Solid-State output modules
03:24 - Transistor output modules
05:00 - Triac output module
05:36 - Output module comparisons
=============================
In this video, we’re going to explore the differences between Solid State and Relay outputs on PLC Digital Output Modules and the pros and cons of each.
The purpose of a PLC Output module is to operate or control a physical device based on field device conditions connected to an input module and decisions made by the PLC program.
Digital or Discrete devices have only 2 possible conditions. These 2 possible conditions could be On or Off, Open or Closed, or Energized or De-energized.
Analog devices are a bit more complicated because they have an infinite number of possible conditions.
A fan is a digital device if it can be turned either on or off.
If the fan can be adjusted for any speed from Off to On, the fan is an analog device because it has an infinite number of possible speeds.
There are 2 types of PLC Digital Output Modules: 1) Relay and 2) Solid State.
1) When PLCs were first introduced, the only outputs were relay type with a separate relay dedicated to each output.
As with any typical relay, the PLC output module had physical coils and relay contacts contained inside.
The contacts were operated by applying a voltage to the relay coil. The contacts were connected to an external supply to turn on or off a discrete device. Not much has changed except today’s modules have miniaturized relays and contacts.
The Allen Bradley 1756-OW16I has 16 individual relay outputs.
We can use one output to operate an AC load and another output to operate a DC load as relay contacts are voltage-independent. That’s one advantage of relay type as solid-state type output modules are not voltage-independent.
Relay Output modules are available with Single Pole Double Throw, or SPDT outputs as well, as seen on the Allen Bradley 1756-OX8I module.
2) Solid-State output modules are often referred to as Switching modules. Output devices are turned on or off by using solid-state devices such as a Bipolar Junction Transistor (BJT) or a Triac.
A Triac output module is capable of controlling AC loads where transistor output modules can control DC loads only. When the PLC signal is applied, the Triac will turn on and provide an alternating current path for the load.
1) Relay
– Relays generally have a higher current rating than transistors, but, as with any mechanical device, it will wear out with time.
– A relay module can operate AC or DC loads, or both.
– Relays provide electrical isolation between the load and the PLC.
– Relays are slow-acting with typical response times of 10 milliseconds or greater.
Closed relay contacts are almost zero ohms thus ensuring no voltage loss.
2) Transistor
– Transistor output modules are for DC applications only.
– Transistors typically cannot switch a large load current as can a relay.
– A transistor is fast because there are no mechanical parts. Their response time is much faster than relays.
– In some transistor modules, there is a leakage current even when turned off.
3) Triac
– A Triac output is used to control AC loads only.
– As with the transistor, a Triac is much faster than a relay.
– Triac outputs are suited to low power AC loads such as lighting, motor starters, and contactors with current ratings of around 1 amp.
=============================
Missed our most recent videos? Watch them here:
=============================
To stay up to date with our last videos, make sure to subscribe to this YouTube channel:
=============================
=============================
#RealPars #PLC #Transistor
Комментарии