filmov
tv
Mig Welding Downhill Problems
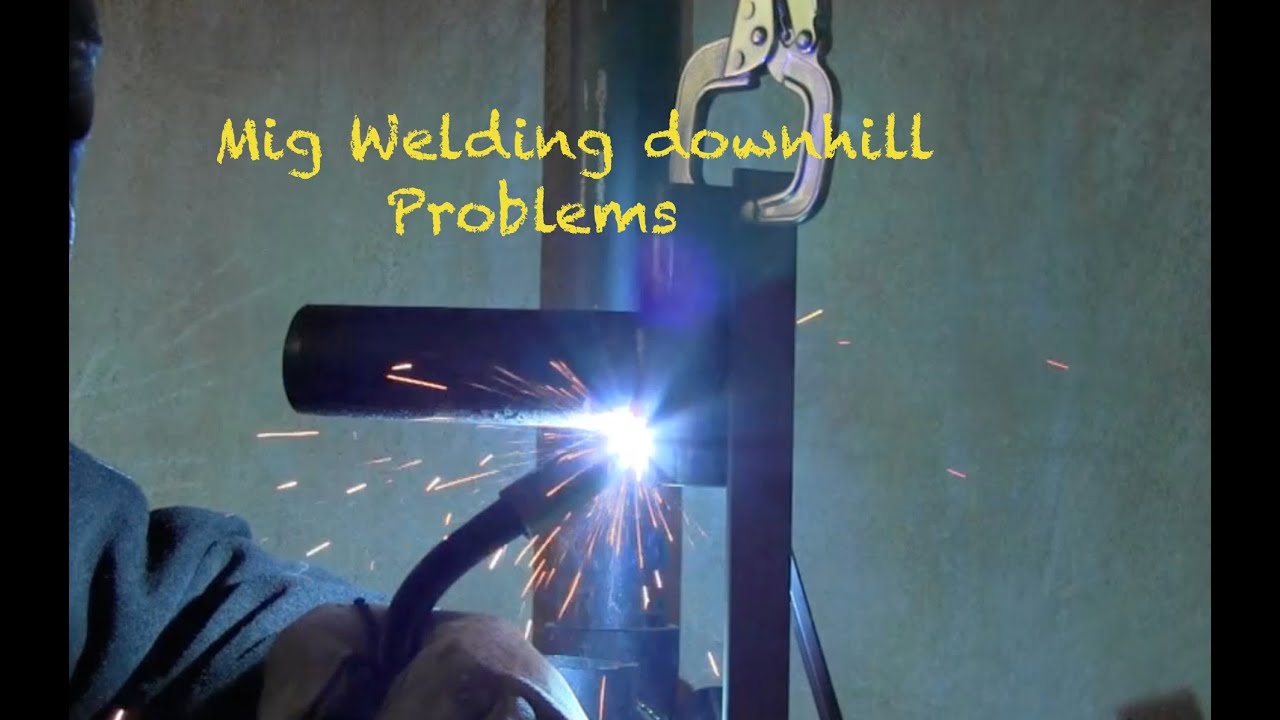
Показать описание
Mig Welding downhill is much easier and usually quicker than uphill.
But its not always the best way to go. for 1/4" and thicker, uphill welding is my choice. But Mill scale on Hot rolled steel can be a problem either way.
But its not always the best way to go. for 1/4" and thicker, uphill welding is my choice. But Mill scale on Hot rolled steel can be a problem either way.
Mig Welding Downhill Problems
Fix This MIG Welding Problem
Downhill MIG Welding #shorts
How NOT TO Weld: Most Common MIG Welding Mistakes
Mig welding downhill #sorts
Is MIG Welding Downhill As Strong As Uphill?
How to mig weld downhill technique | GMAW for beginners tips and tricks
Setting Wire Speed On A Mig Welder To Match Voltage, Must See For Beginners Learning Welding
MIG Welding 3g Plate Uphill Root vs Downhill
Downhill mig welding #sorts
(HELP) I Can't See My Mig WELDS (Top 5 Tips)
MIG downhill welding
MIG Welders Beware! - 'Pretty' Does NOT Equal Strong. - Weld Analysis
42. MIG welding. Vertical Welding Demo downhill
MIG Welding | Vertical Uphill and Downhill
MIG Welding GMAW- Vertical downhill
downhill mig weld
Learning 3F Downhill MIG!
MIG Welding Overhead - Mig basics part 8
How To MIG Downhill
How to Make Consistent MIG Welds
Mig welding GMAW - Vertical downhill of box tube/section corners.
3F 2 Pass Vertical MIG Weld
Walking the Cup with MIG welding: Downhill Root, Uphill Fill and Cap
Комментарии