filmov
tv
Jointing a twisted board at warp speed - with Bob Van Dyke
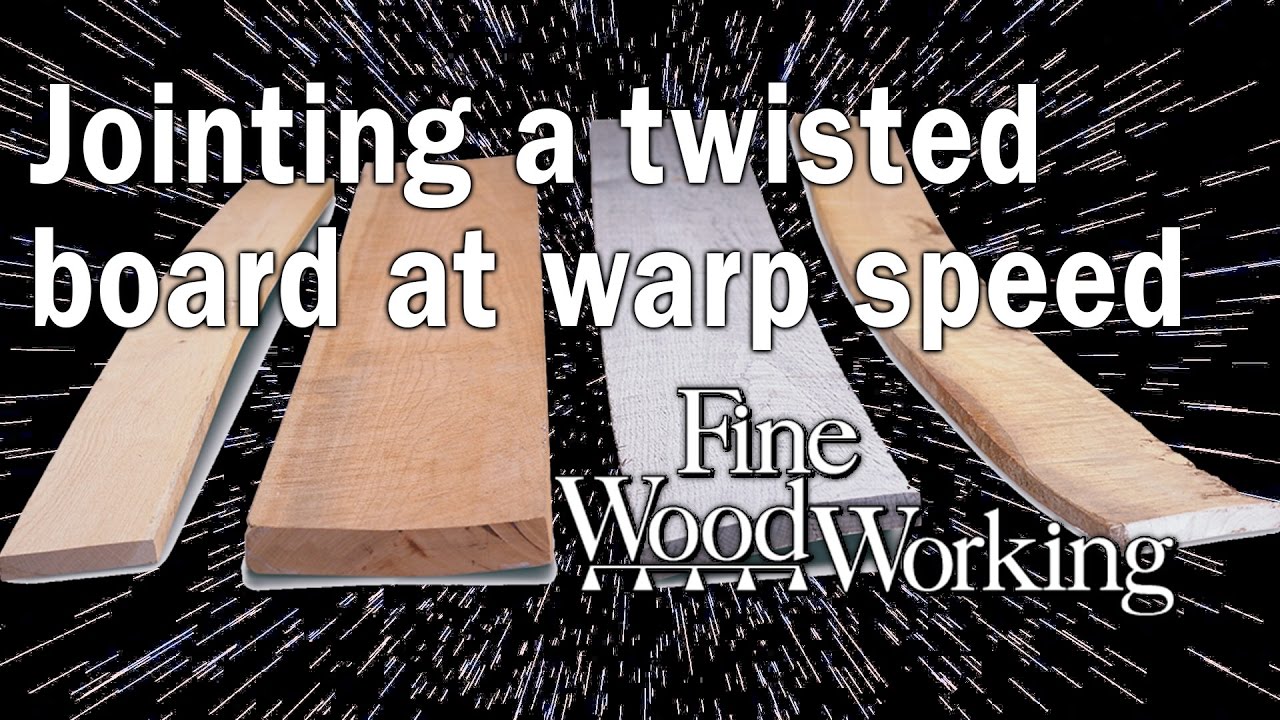
Показать описание
In this video Bob Van Dyke shows you how he flattens a board that many would consider too warped to use.
Jointing a twisted board at warp speed - with Bob Van Dyke
How to surface plane a twisted board safely on a Jointer Planer to produce a face side
How to flatten a twisted board in under 5 minutes
How to plane flat a twisted (in wind) board using a surface planer (jointer).
5 Ways to Joint a Board Without a Jointer
Jointer Basics Flatten a twisted board
Easy Way to Straighten Out Warped Twisted Crooked Cupped Lumber.
How to fix a badly twisted slab/board without losing much thickness
2 new people joining twisted gang!
Flattening a Twisted Board! #woodworking #shorts
Mill and Process Lumber Like a Pro - Woodworking Essentials
Table Saw Basics - Twisted And Crooked Wood
169 - How to Flatten Boards Wider Than Your Jointer
Skip Planing Tutorial | Skip Plane & Flatten Reclaimed Wood | How To
Getting Wood/Lumber Dead Flat with a Hand Plane
How To Flatten a Twisted Board By Hand
How to Flatten Cupped and Twisted Wood | ToolsToday
Twisted Board Quick Fix
BEGINNERS Guide to Using an Electric Planer.
How to Flatten a Live Edge Wood Slab
How to Make a Simple Planer Sled for Flattening Wide Boards
Fix twisted or cupped boards without a jointer.
How To Flatten Twisted Boards #shorts
TWISTED BOARD FLATTENING JIG
Комментарии