filmov
tv
Design Perfect Scoops for Mass Production 3D Printing
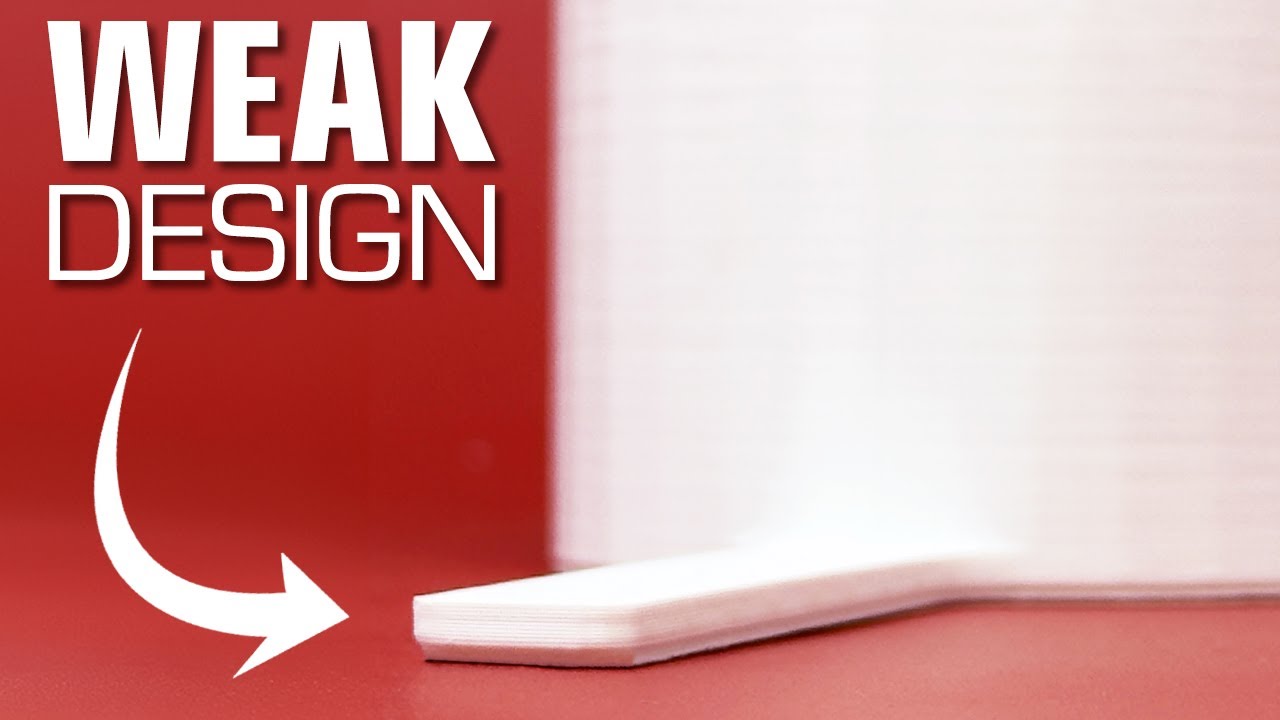
Показать описание
Learn how to design a scoop optimized for 3D printing, whether for mass production or print-on-demand. We explore the challenges of 3D printing traditional designs meant for injection molding and share expert tips on modifying a scoop to be perfectly suited for 3D printing. Discover how to minimize supports, improve surface quality, and leverage the unique capabilities of 3D printing to create functional and competitive products. Perfect for 3D printing hobbyists, entrepreneurs, and anyone interested in bringing their unique designs to life. Watch now to unlock new design possibilities and get ahead in the world of 3D printing!
#3dprinting #designfor3dprinting #3dprintingideas #3dprintingdesign #3dprintingtips
🔗 OTHER IMPORTANT LINKS 🔗
About Slant 3D
🏭 High-Volume 3D Printing: Scalability Meets Flexibility
Slant 3D's Large-Scale 3D Print Farms utilize 1000's of FDM 3D printers working 24/7 to offer limitless scalability and unparalleled flexibility. Whether it's 100 or
100,000 parts, our system can handle it reliably, while still allowing for real-time design updates, ensuring products evolve with the times. This adaptability is key in today's fast-paced world.
🌿 Sustainable Manufacturing: Eco-Friendly Efficiency
Embrace a system that drastically reduces carbon emissions by eliminating carbon-intensive steps in the supply chain, such as global shipping and warehousing. Our approach minimizes this footprint, offering a more sustainable manufacturing option.
⚙️ Digital Warehouses: Parts On-Demand
Think of print farms as a "Digital Warehouse", meaning we can store your parts digitally on a server rather than physically on a shelf. parts are available on-demand, reducing the need for extensive physical inventory.
*As an Amazon Associate, I earn commission from qualifying purchases.*
Produced by Geometry Media
#3dprinting #designfor3dprinting #3dprintingideas #3dprintingdesign #3dprintingtips
🔗 OTHER IMPORTANT LINKS 🔗
About Slant 3D
🏭 High-Volume 3D Printing: Scalability Meets Flexibility
Slant 3D's Large-Scale 3D Print Farms utilize 1000's of FDM 3D printers working 24/7 to offer limitless scalability and unparalleled flexibility. Whether it's 100 or
100,000 parts, our system can handle it reliably, while still allowing for real-time design updates, ensuring products evolve with the times. This adaptability is key in today's fast-paced world.
🌿 Sustainable Manufacturing: Eco-Friendly Efficiency
Embrace a system that drastically reduces carbon emissions by eliminating carbon-intensive steps in the supply chain, such as global shipping and warehousing. Our approach minimizes this footprint, offering a more sustainable manufacturing option.
⚙️ Digital Warehouses: Parts On-Demand
Think of print farms as a "Digital Warehouse", meaning we can store your parts digitally on a server rather than physically on a shelf. parts are available on-demand, reducing the need for extensive physical inventory.
*As an Amazon Associate, I earn commission from qualifying purchases.*
Produced by Geometry Media
Комментарии