filmov
tv
Main Cylinder Machining! Big Steam Engine Build, Part 6
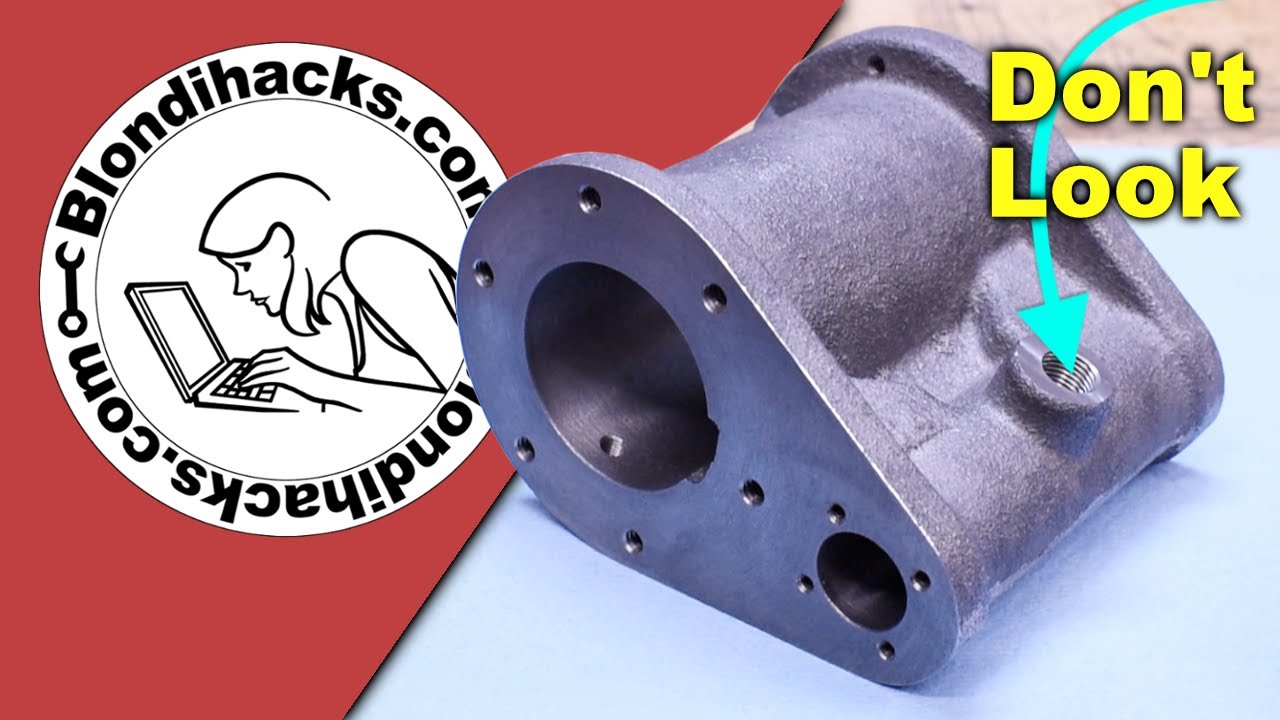
Показать описание
This episode on Blondihacks, I’m machining the main steam cylinder casting! Exclusive videos, drawings, models & plans available on Patreon!
Here are links for many of the tools that you see me using:
(I earn small commissions on these links)
Want more content like this? Try these places:
As an Amazon Associate, I earn from qualifying purchases.
Here are links for many of the tools that you see me using:
(I earn small commissions on these links)
Want more content like this? Try these places:
As an Amazon Associate, I earn from qualifying purchases.
Main Cylinder Machining! Big Steam Engine Build, Part 6
Main Bearings! Big Steam Engine Build, Part 4
Overtaking with a steam engine.
Engine block transformation after chemical dipping
how to half do a job- setting up and boring steam cylinders
Let's Build A Model Steam Engine - Machining a cylinder casting!
Making a Simple Steam Engine
Making a BIG Hydraulic Cylinder Rod & Eye | Part 2
Steam Engine Build: Machining the Engine Cylinder: Part 1
With Steam Path Turbine Services Inc #in situ #usa #machining
Steam Update: Tackling Big 'Boring' Jobs
Impressive CNC Lathe Machine Turning
Lapping a Cylinder! Big Steam Engine Build, Part 7
Big Steam Engine
Bending Wood #shorts
How a Radial Engine Works- High RPM (Part 3)
Machining a Model Steam Engine Cylinder - Part 1
Steam Engine - How Does It Work
Getting It To Run And Finishing Touches! Big Steam Engine Build, Part 16
Boring steam cylinders
CNC boring and milling machine equipped with extened side milling head. 、For steam turbine cylinder....
machining a locomotive steam cylinder
Live Steam Locomotive Cylinder Machining , Home Machine Shop
Part 20: Boring the Cylinders
Комментарии