filmov
tv
What Should I Use?: Episode 6 - Roofing Assembly
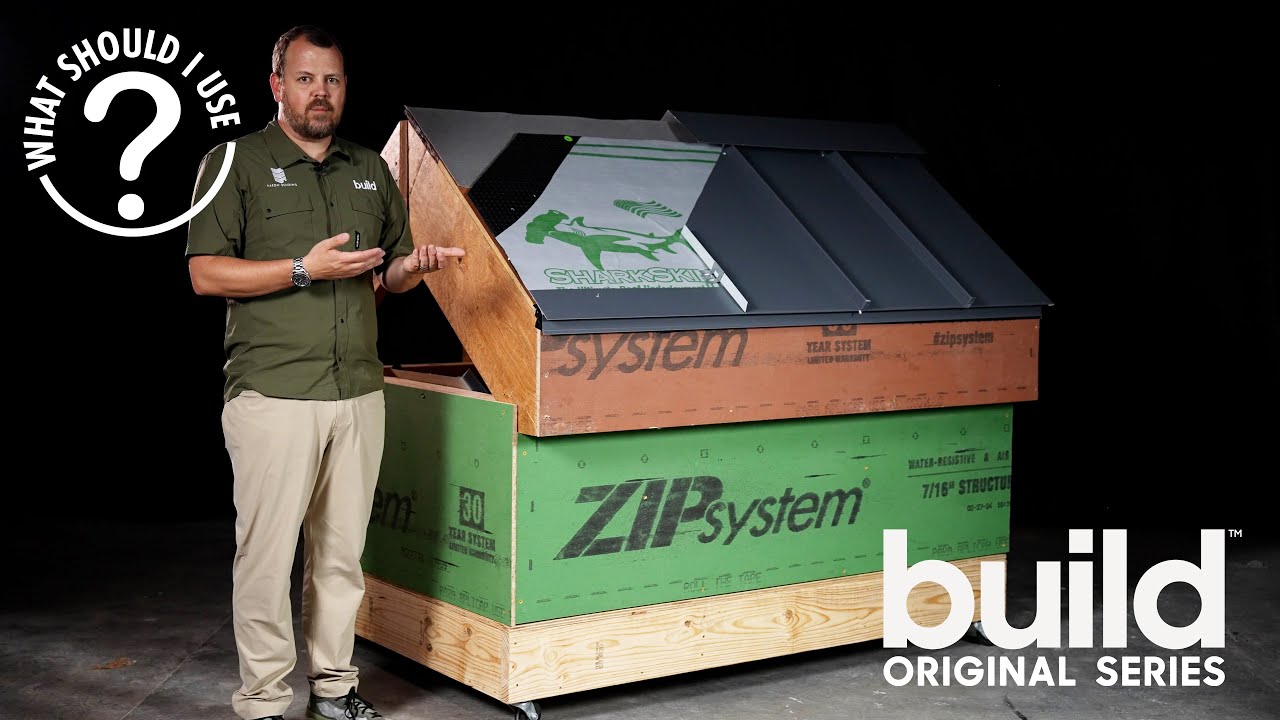
Показать описание
In this episode of "What Should I Use?" hosted by Jake Bruton, we dive deep into roofing, exploring the intricacies of roofing codes, with a focus on metal roofs and the importance of durability. Jake begins with a key excerpt from the IRC 2021 on roof drainage, emphasizing its relevance in expansive soil areas. The discussion shifts to the pros and cons of asphalt shingles versus metal roofs, and the cost-benefit analysis of each. With special guest Peter Yost from Building - Wright, we delve into the specifics of unvented attic assemblies and the significance of vapor diffusion ports in maintaining roof integrity. Jake also shares insights on fortified roofing standards and why choosing the right materials can significantly impact the longevity and durability of your roof.
This episode is sponsored by Sharkskin and Sheffield Metals.
Subscribe and follow my Podcast on Apple or Spotify!
Sign up for our twice-weekly newsletter:
To sponsor a video or advertise with us visit:
This episode is sponsored by Sharkskin and Sheffield Metals.
Subscribe and follow my Podcast on Apple or Spotify!
Sign up for our twice-weekly newsletter:
To sponsor a video or advertise with us visit:
Комментарии