filmov
tv
Annealing 3D Printed Nylon for high temperature resistance? Can it be done?
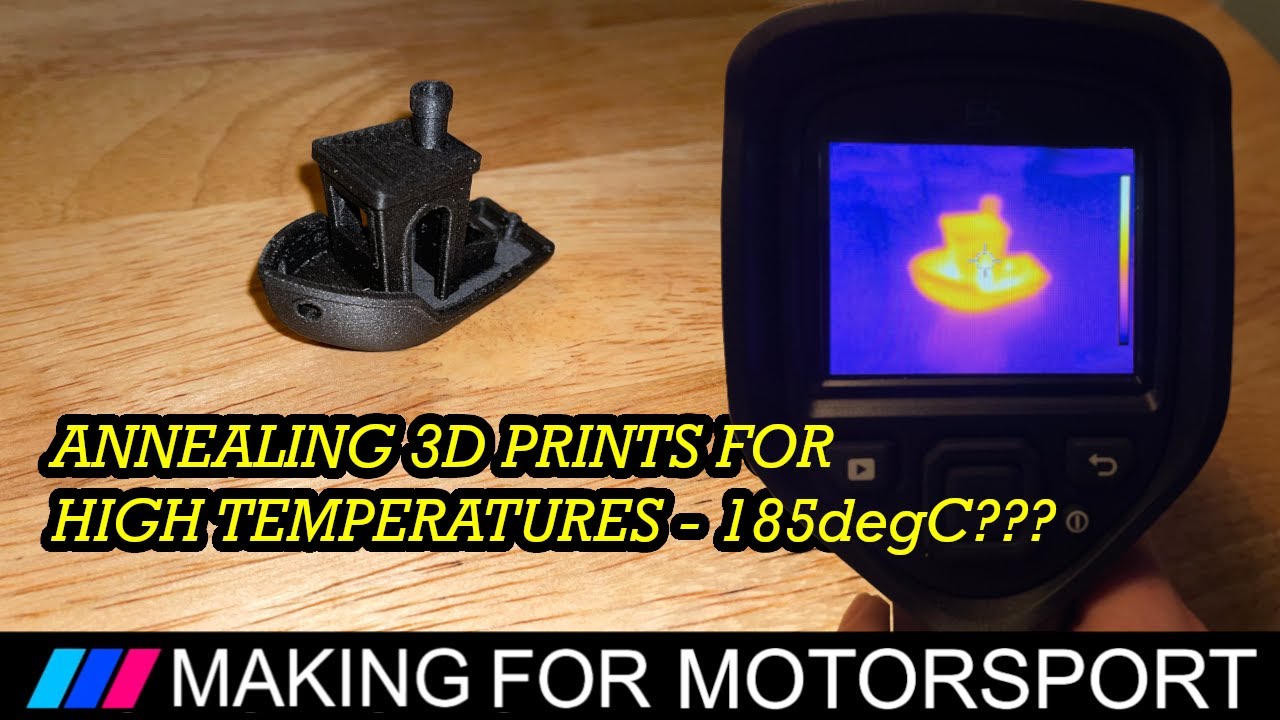
Показать описание
I have some Carbon Fibre (fiber) Nylon which I need to use in a high temperature (120degC) application, will it be suitable and can it be annealed to improve it?
Links: -
CNC Kitchens video on annealing materials...
A great piece on annealing of Semi-crystaline polymers (which Nylon is)...
More info on specific annealing for Nylon...
Credit for title sequence slooooo-mooooo - Fern Motorsport
Links: -
CNC Kitchens video on annealing materials...
A great piece on annealing of Semi-crystaline polymers (which Nylon is)...
More info on specific annealing for Nylon...
Credit for title sequence slooooo-mooooo - Fern Motorsport
Carbon Fiber Nylon FAQ Part 1 - We Answer Your Most Asked Questions About Printing CFPA Filaments
Annealing 3D Printed Nylon for high temperature resistance? Can it be done?
PLA IS BETTER Than Carbon Fiber Nylon?
Annealing Carbon Fiber 3d printed parts the easy way
Annealing: How to improve your 3D prints
How to Succeed When 3D Printing With Nylon
Annealing Nylon Prints In Oil to Prevent Moisture Absorption? Testing the Taulman Glass Fiber Nylon.
Annealing Nylon (12) Carbon Fiber 3D printed Lorenz Motors dronecar model in $6000 MakerBot printer
Which Nylon Filament is Best???
Annealing 3D Prints: Will it survive? 💪🏾
Why Choose Nylon 12?
Triple (x3) your Layer Strength by Annealing 3D Prints in Plaster!
[3D printing] Multi-material for annealing to enhance stiffness?
3D Printing Machine Parts with Carbon-Fiber Nylon | NylonX
Annealing for a stronger, more heat resistant part.
3D Printed Alloy910 Nylon Annealing Impact Strength Test
What's the temperature resistance of annealed PLA, PETG and ABS?
Guess what's cooking. Annealing Carbon fiber blend 3d prints.
The STRENGTH of 3D prints REMELTED in SALT
3d Printing Glass Filled Nylon For Beginners (Ender 3)
I Tested PPA-CF Filament and It's INSANELY Strong!
What is the strongest 3D printing material
Arcus 3D C1 - End effector v4.2, annealed and dyed nylon
What is Annealing? Do You Need To? | EDGE OF 3D
Комментарии