filmov
tv
Making a nice BIG assembly table! | #shorts
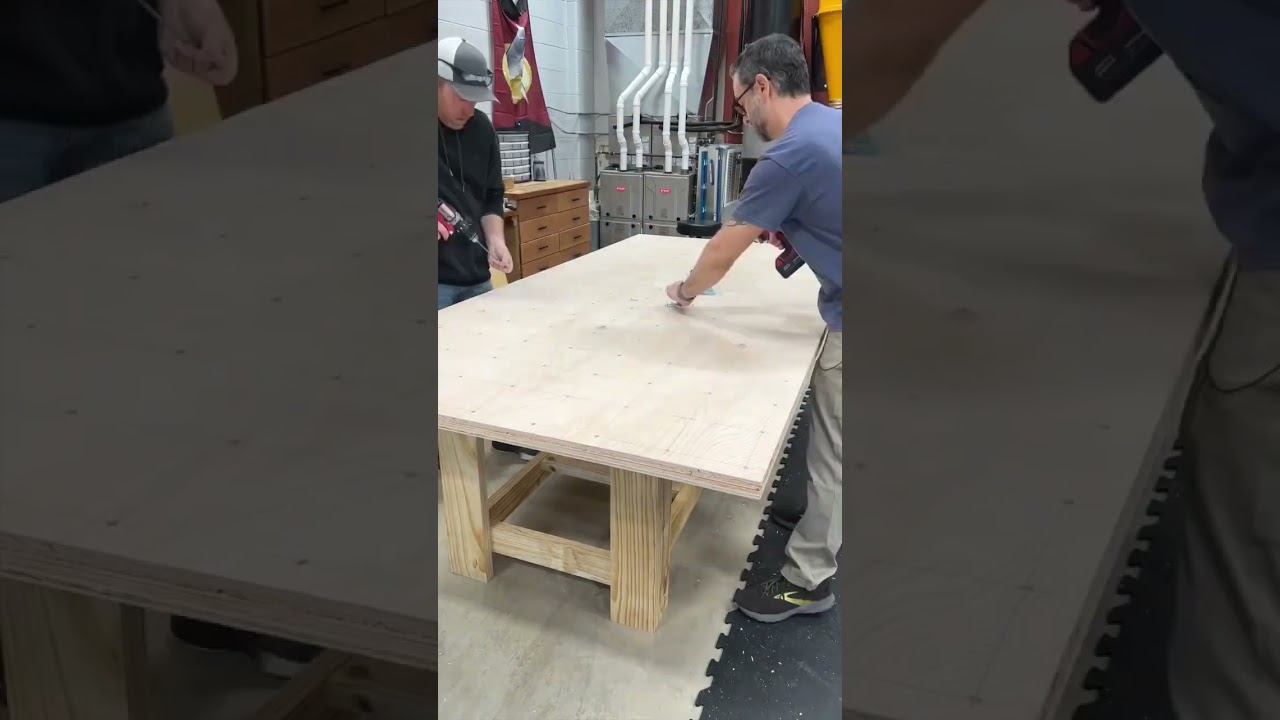
Показать описание
Who is Marc Spagnuolo? Watch Behind the Scenes with a YouTube veteran and find out!
Making a nice BIG assembly table! | #shorts
Large assemblies made easy
[Part 1] The Big Assembly Adventure: Taming Large Assemblies in SOLIDWORKS
[Part 2] The Big Assembly Adventure: Taming Large Assemblies in SOLIDWORKS
How to make a Plastic Chair on an Injection molding machine #shorts
SOLIDWORKS - Large Assemblies: Options and Large Assembly Mode
Transformed my Quadricycle into Electric!
The Only Way You Should Add Blood To LEGO Minifigures #shorts
Amazing Big Assembly Roubo Bench Legs #woodworking #diy #shorts
How to design in the Assembly mode in SOLIDWORKS
SOLIDWORKS Tutorial - Large Assembly Best Practices
Simple tips for drone making
BMW Motorcycle Engine Assembly | HOW IT'S MADE
Stowing Away Folding Assembly Table
MASSIVE Assembly Table with Custom Storage Underneath
FAKE BLOOD! SPOOKY SFX HALLOWEEN MAKEUP!! #shorts
Hydraulic bearing rapid installation process- Good tools and machinery make work easy
Crocheted rose flower assembly
Large Assembly Performance - SOLIDWORKS 2019
1 SIMPLE Tip to Reduce Nerves When Public Speaking
Top 3 upgrades for $30!
Simple Programming, Amazing Results: DIY Bluetooth Speaker with #ESP32 and 2 Speakers
How To Make Bookshelves With Simple Tools
Quotes (thought) Of The Day//Good Thoughts for school assembly
Комментарии