filmov
tv
Welding Tricks! How to weld Steel to Cast
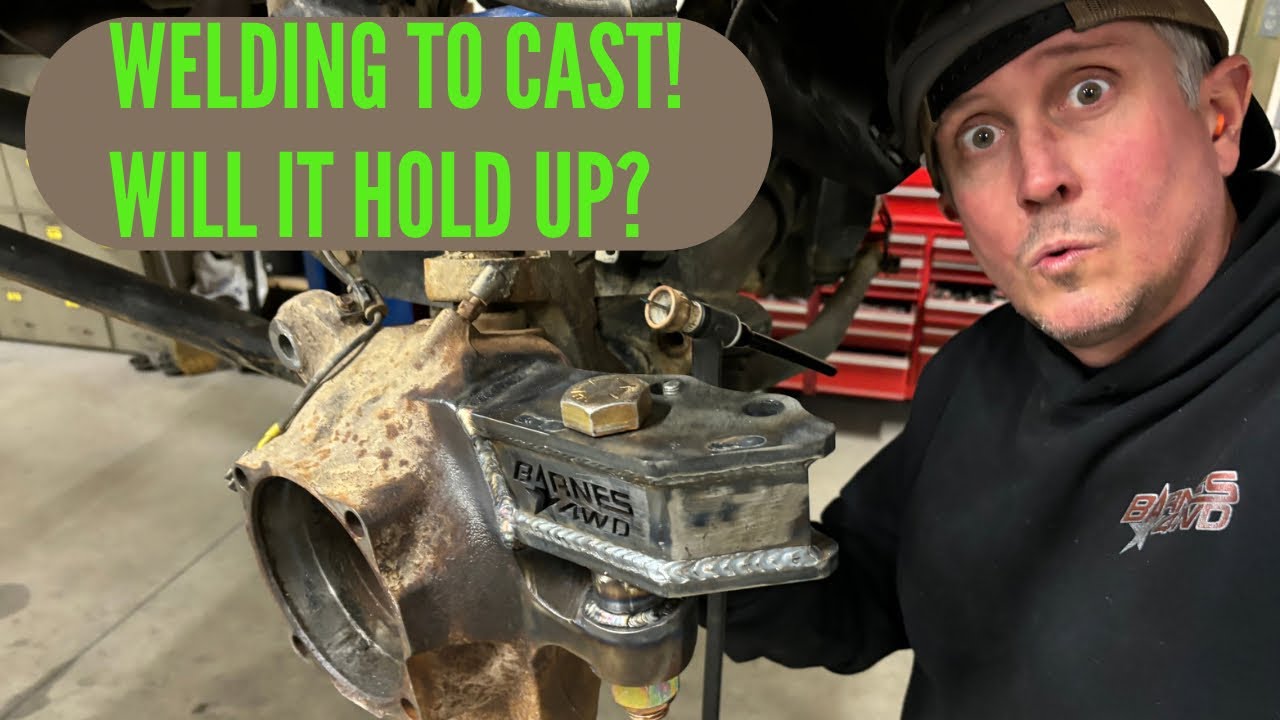
Показать описание
Here is a fun project! I show my tips and tricks when it comes to welding tabs, brackets, and most importantly , How to weld Steel plate to Cast steel.
Tools used..
Harris super Missile welding rod
Miller Multimatic 220 ac/dc multiprocess welder
Hobart Nickel99 welding rod
Barnes 4wd super duty high steer kit
keywords
fabrication
welding
tig welding
mig welding
dissimilar metals
barnes4wd
ford f250
super duty
welding tutorial
how to tig weld
dirt head shed
Tools used..
Harris super Missile welding rod
Miller Multimatic 220 ac/dc multiprocess welder
Hobart Nickel99 welding rod
Barnes 4wd super duty high steer kit
keywords
fabrication
welding
tig welding
mig welding
dissimilar metals
barnes4wd
ford f250
super duty
welding tutorial
how to tig weld
dirt head shed
Welding Basics for Beginners
Welding 101: How To Run A Straight Bead
How To Weld Holes In 7 Mins | Gasless Flux Core Welding Tips And Tricks |
How NOT TO Weld: Most Common MIG Welding Mistakes
novice welder may not know the best way to weld a thin square tube #howtoweldingforbeginners
After 20 Years Of Welding, I Learn How To Weld
7 Tips/Tricks To Make Your 110v Weld Like A 220v! (welding tips for beginners)
How to weld, Tips for Beginners
HOW TO MIG LIKE TIG WELD (Stacking Dimes) W/ OVERKILLRACINGANDCHASSIS w/ *Tips and Techniques*
Stick Welding Tips
What is a Better Way to Learn to TIG Weld?
How to Weld 7018 welding rod tips and tricks.
STICK WELDING 101: Getting Started With SMAW
Dialing in a Weld Procedure
Achieving Good Plastic Welding. Repost from @AutoPro1112 #yeswelder #shorts #welding #weld #plastic
How to MIG Weld for Beginners: MIG Welding Basics
How I Weld My Butt Joints | Tips & Tricks | MIG THIN METAL
Tips for Passing an Aerospace Weld Test on Stainless
How NOT to MIG weld: Variables in MIG welding
Tips On How To Mig Weld Thin Metal Auto Body Panels #welding #fabrication #howtoweldforbeginners
TIG weld 6G🤨🧐🧐root pasd welding
How to TIG Weld Aluminum part 1
How To Spot Weld Using Gasless Welding | Flux Core Welding Tips And Tricks
How To Weld Thin Metal Using Flux Core Gasless Welder | Flux Core Welding Tips And Tricks |
Комментарии