filmov
tv
Improving Curved Surfaces | Design for Mass Production 3D Printing
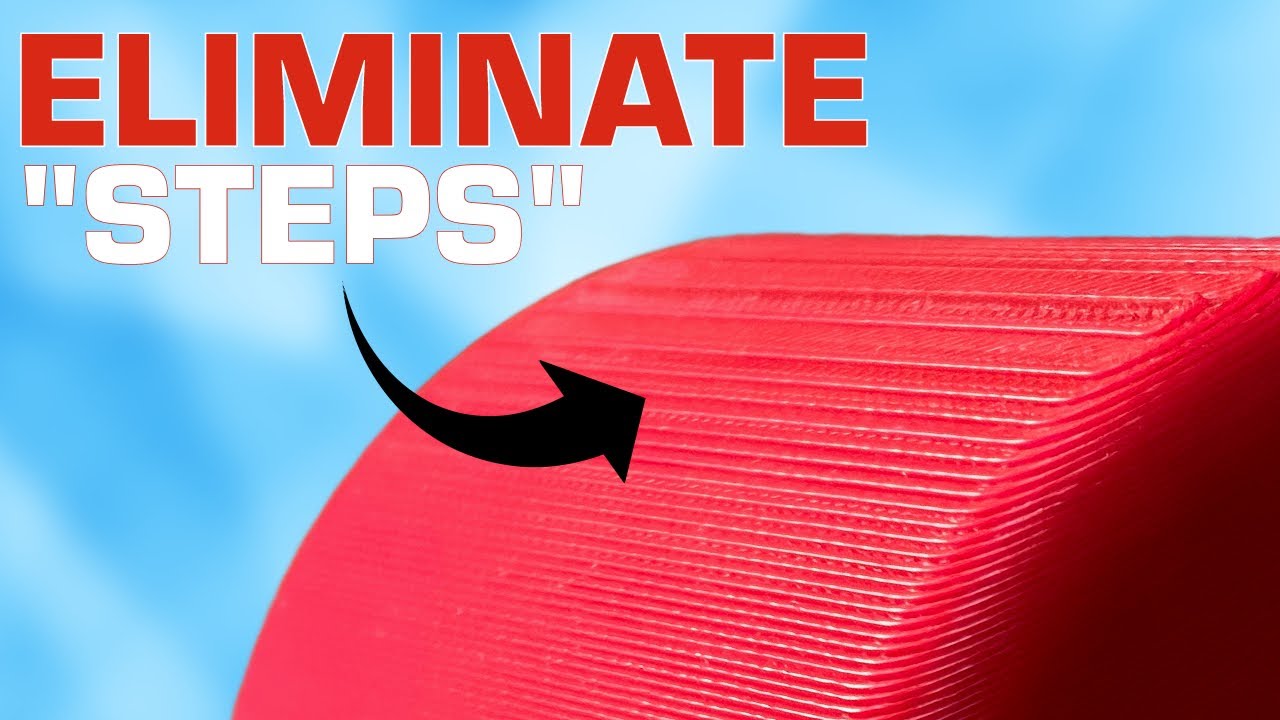
Показать описание
Curved surface finishes on 3D printed parts can often be challenging, especially with the appearance of layer lines as the part moves up the curve. In this video, we delve deep into the details of why these layer lines appear more distinct, especially on the top of curved surfaces. We'll guide you through multiple solutions that will help you improve the appearance of your parts. Whether you're aiming for a smoother finish or seeking innovative ways to enhance aesthetics, these design tips will open up new possibilities for your 3D printed parts.
If you would like to learn more about how to change your approach towards manufacturing products with Mass Production 3D Printing, make sure to SUBSCRIBE to Slant 3D!
00:00 What Causes "Stair Stepping" on Round Prints?
00:56 Increasing Print Resolution to Improve Surface Finish
02:04 Print Vertically for Consistent Surface Finish
02:42 Use Angles and Flat Edges When Possible
03:48 Pixelated Parts Can Offer a Unique Aesthetic
04:52 Utilize Textures to Blend Layer Lines
🔗 IMPORTANT LINKS 🔗
About Slant 3D
🏭 High-Volume 3D Printing: Scalability Meets Flexibility
Slant 3D's Large-Scale 3D Print Farms utilize 1000's of FDM 3D printers working 24/7 to offer limitless scalability and unparalleled flexibility. Whether it's 100 or 100,000 parts, our system can handle it reliably, while still allowing for real-time design updates, ensuring products evolve with the times. This adaptability is key in today's fast-paced world.
🌿 Sustainable Manufacturing: Eco-Friendly Efficiency
Embrace a system that drastically reduces carbon emissions by eliminating carbon-intensive steps in the supply chain, such as global shipping and warehousing. Our approach minimizes this footprint, offering a more sustainable manufacturing option.
⚙️ Digital Warehouses: Parts On-Demand
Think of print farms as a "Digital Warehouse", meaning we can store your parts digitally on a server rather than physically on a shelf. parts are available on-demand, reducing the need for extensive physical inventory.
*As an Amazon Associate, I earn commission from qualifying purchases.*
Produced by Slant Media
If you would like to learn more about how to change your approach towards manufacturing products with Mass Production 3D Printing, make sure to SUBSCRIBE to Slant 3D!
00:00 What Causes "Stair Stepping" on Round Prints?
00:56 Increasing Print Resolution to Improve Surface Finish
02:04 Print Vertically for Consistent Surface Finish
02:42 Use Angles and Flat Edges When Possible
03:48 Pixelated Parts Can Offer a Unique Aesthetic
04:52 Utilize Textures to Blend Layer Lines
🔗 IMPORTANT LINKS 🔗
About Slant 3D
🏭 High-Volume 3D Printing: Scalability Meets Flexibility
Slant 3D's Large-Scale 3D Print Farms utilize 1000's of FDM 3D printers working 24/7 to offer limitless scalability and unparalleled flexibility. Whether it's 100 or 100,000 parts, our system can handle it reliably, while still allowing for real-time design updates, ensuring products evolve with the times. This adaptability is key in today's fast-paced world.
🌿 Sustainable Manufacturing: Eco-Friendly Efficiency
Embrace a system that drastically reduces carbon emissions by eliminating carbon-intensive steps in the supply chain, such as global shipping and warehousing. Our approach minimizes this footprint, offering a more sustainable manufacturing option.
⚙️ Digital Warehouses: Parts On-Demand
Think of print farms as a "Digital Warehouse", meaning we can store your parts digitally on a server rather than physically on a shelf. parts are available on-demand, reducing the need for extensive physical inventory.
*As an Amazon Associate, I earn commission from qualifying purchases.*
Produced by Slant Media
Комментарии