filmov
tv
This Forge Changes Everything
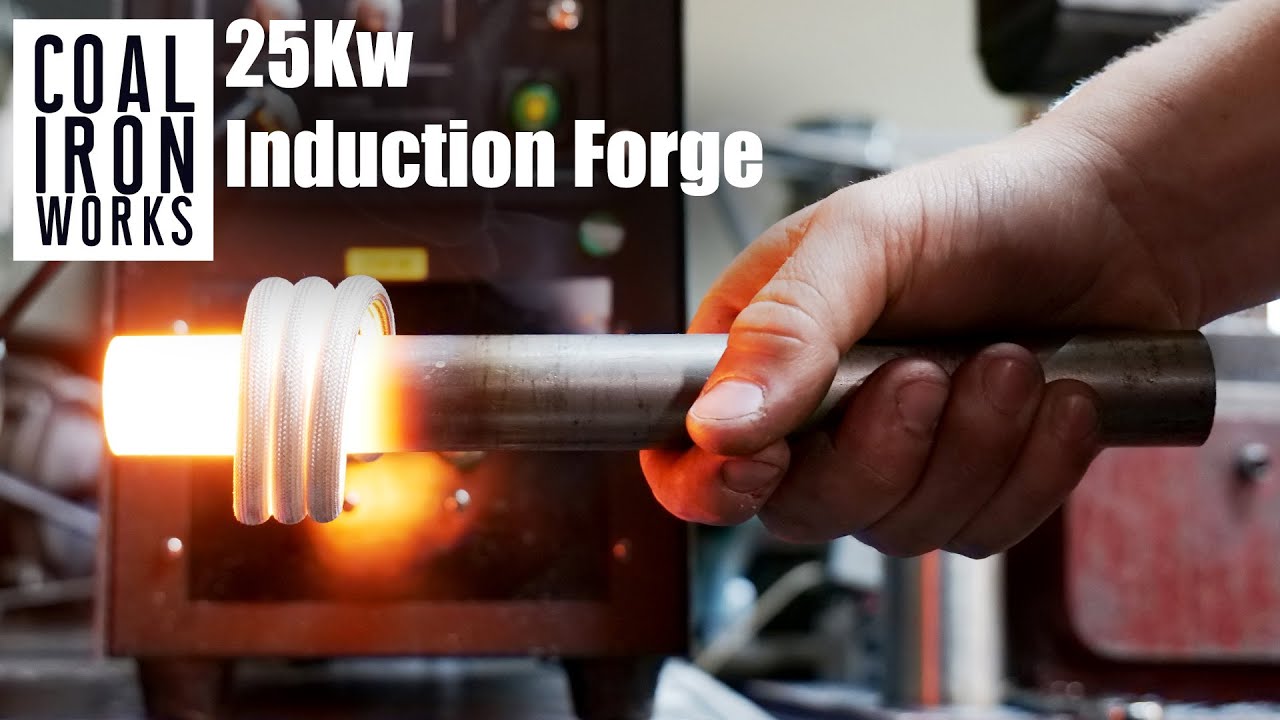
Показать описание
@CoalIronWorks
Make sure to check out Patreon! You'll get your name in the credit roll of the video, and it's the best way to directly support us.
Make sure to check out Patreon! You'll get your name in the credit roll of the video, and it's the best way to directly support us.
This Forge Changes Everything
This Forge Tip Changes EVERYTHING!!
Simple question 👀
10 Iranian Submarines Shadow USS Eisenhower – Then THIS Changed Everything | US Navy
The Most Realistic Minecraft Mod
This Minecraft Mod Will Change Everything! 🚀
BLOX FRUIT ALL FRUITS ON STOCK #roblox #robloxnpc #bloxfruits #bloxfruitsnoobtopro #bloxfruits
Losing All Of Your Fingernails 😱
Mind-Blowing Planet Days: How Long Is a Day on Other Worlds?
We Tried to Break Hero Forge! Kitbashing changes everything...
Minecraft Mods That Should Be In The Game Pt. 33 #minecraft #mods
The Reset That Changes Everything 🚀 | New version of Value Forge Esports
This Sonic X Shadow Generations Ability Changes EVERYTHING!
This Minecraft Mod Will Change Everything! 🚀
Mods That Improve Minecraft's Realism (1.18.2 Mods Pt. 13)
Finally a Unique Multi-Color 3D Printer - Flashforge AD5X
Quantum Computing Is Coming to IoT– And It Changes EVERYTHING
Minecraft, But Anything You Build You Turn Into…
Dog With Special Needs Makes Her First Friend at the Park! ❤️
How to get FULL BRIGHT in 1.19 and above!
Cool Minecraft Mods Pt. 10 #minecraft #minecraftmods #shorts
How Groot Changed Everything in Infinity War #shorts
Minecraft Mods That Make You PRO
the most popular mod ever...
Комментарии