filmov
tv
How to consider safe spacing in PCB design? #PCB #FPC #PCBA #CIRCUITBOARD
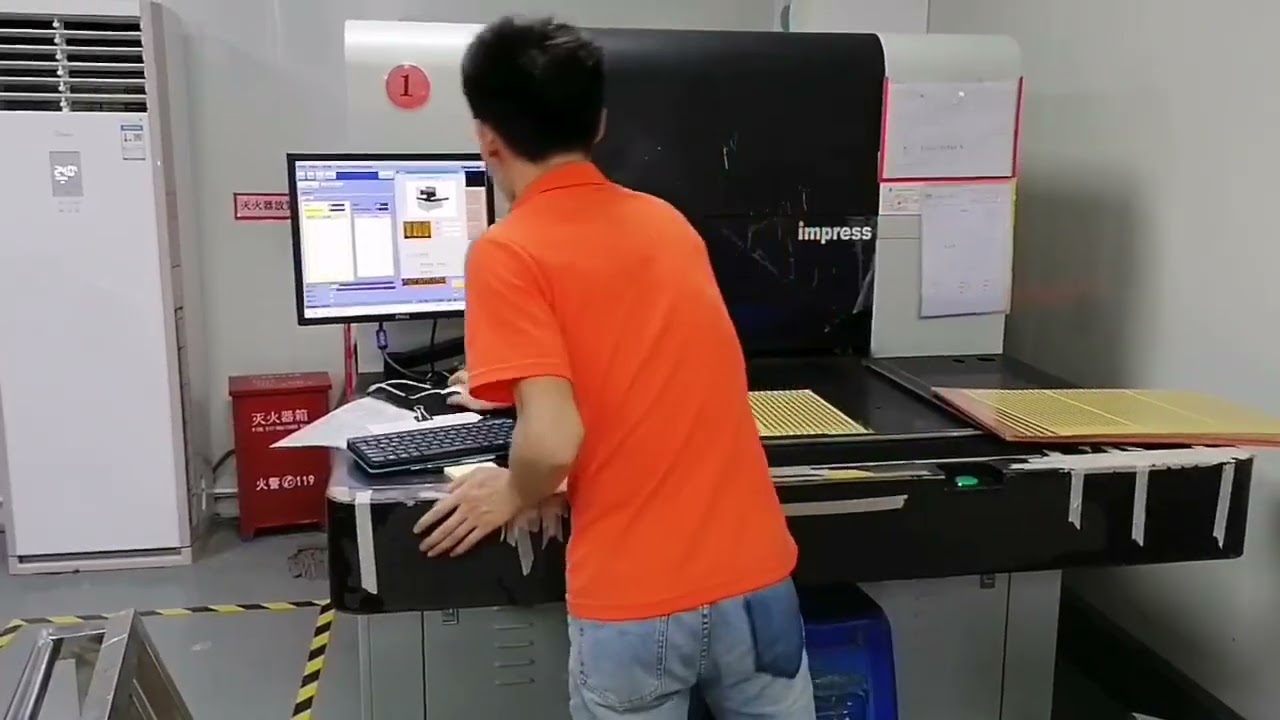
Показать описание
There are many areas in PCB design where safe spacing needs to be considered. Here, it is temporarily classified into two categories: one is electrical related safety spacing, the other is non-electrical related safety spacing.
Electrical related safety spacing
1. Spacing between wires
As far as the processing capacity of mainstream PCB manufacturers is concerned, the minimum spacing between wires shall not be less than 4mil. The minimum wire distance is also the distance from wire to wire and wire to pad. From the perspective of production, the bigger the better if possible, and 10mil is a common one.
2. Pad aperture and pad width
In terms of the processing capacity of mainstream PCB manufacturers, the aperture of the pad should not be less than 0.2mm if it is mechanically drilled, and 4mil if it is laser drilled. The aperture tolerance is slightly different according to the plate, generally can be controlled within 0.05mm, the minimum width of the pad should not be less than 0.2mm.
3. Spacing between pad
As far as the processing capacity of mainstream PCB manufacturers is concerned, the spacing between pads shall not be less than 0.2mm.
4. The distance between copper and plate edge
The spacing between the charged copper leather and the edge of the PCB board should be no less than 0.3mm. On the Design-Rules-Board outline page, set the spacing rule for this item.
If a large area of copper is laid, there is usually a shrinkage distance between the plate and the edge, which is generally set to 20mil. In the PCB design and manufacturing industry, under normal circumstances, due to the mechanical considerations of the finished circuit board, or to avoid the copper skin exposed on the edge of the board may cause edge rolling or electrical short circuit, engineers will often spread a large area of copper block relative to the edge of the board shrinkage 20mil, rather than the copper skin has been spread to the edge of the board.
This copper indention can be handled in a variety of ways, such as drawing a keepout layer along the edge of the plate, and then setting the distance between the copper and the keepout. A simple method is introduced here, that is, different safety distances are set for the copper laying objects. For example, the safety distance of the whole board is set to 10mil, and the copper laying is set to 20mil, which can achieve the effect of shrinking 20mil inside the edge of the board and eliminate the possible dead copper in the device.
Electrical related safety spacing
1. Spacing between wires
As far as the processing capacity of mainstream PCB manufacturers is concerned, the minimum spacing between wires shall not be less than 4mil. The minimum wire distance is also the distance from wire to wire and wire to pad. From the perspective of production, the bigger the better if possible, and 10mil is a common one.
2. Pad aperture and pad width
In terms of the processing capacity of mainstream PCB manufacturers, the aperture of the pad should not be less than 0.2mm if it is mechanically drilled, and 4mil if it is laser drilled. The aperture tolerance is slightly different according to the plate, generally can be controlled within 0.05mm, the minimum width of the pad should not be less than 0.2mm.
3. Spacing between pad
As far as the processing capacity of mainstream PCB manufacturers is concerned, the spacing between pads shall not be less than 0.2mm.
4. The distance between copper and plate edge
The spacing between the charged copper leather and the edge of the PCB board should be no less than 0.3mm. On the Design-Rules-Board outline page, set the spacing rule for this item.
If a large area of copper is laid, there is usually a shrinkage distance between the plate and the edge, which is generally set to 20mil. In the PCB design and manufacturing industry, under normal circumstances, due to the mechanical considerations of the finished circuit board, or to avoid the copper skin exposed on the edge of the board may cause edge rolling or electrical short circuit, engineers will often spread a large area of copper block relative to the edge of the board shrinkage 20mil, rather than the copper skin has been spread to the edge of the board.
This copper indention can be handled in a variety of ways, such as drawing a keepout layer along the edge of the plate, and then setting the distance between the copper and the keepout. A simple method is introduced here, that is, different safety distances are set for the copper laying objects. For example, the safety distance of the whole board is set to 10mil, and the copper laying is set to 20mil, which can achieve the effect of shrinking 20mil inside the edge of the board and eliminate the possible dead copper in the device.